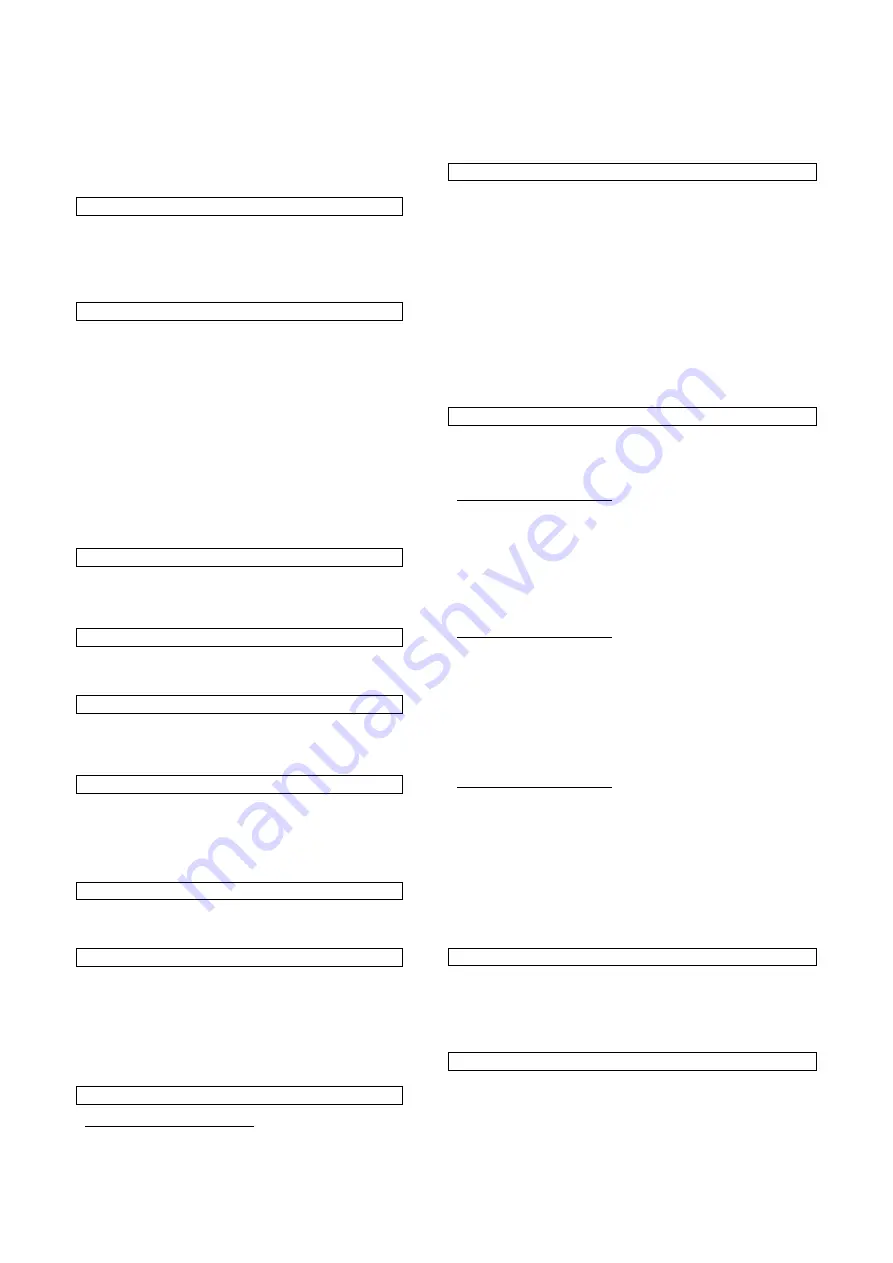
immediately after it has been used. If you seek help,
state the following pieces of information:
1. Accident
site
2. Accident
type
3.
Number of injured persons
4. Injury
type(s)
Using the appliance as designated
The compressor has exclusively been designed for the
production and accumulation of compressed air.
The compressed air is only suitable for pneumatic tools
/appliances/ of a machine. Any other use is conflict with
the compressor designation.
Residual Dangers
Direct electric contact
A faulty cable or faulty connector plug may lead to a
fatal accident caused by electric current.
Have always the faulty cables and connector plugs
replaced at a specialist. Use the device at a connector
equipped with current protector (RCD) only.
Indirect electric contact
Injury by parts of the machine that are live or by
faulty constructional elements of the machine.
Always pull the connector plug out of socket at
maintenance works. Operate with current protector only.
Insufficient local lighting
Insufficient lighting represents a high safety risk.
Always ensure sufficient lighting at work with this device.
Disposal
Instructions for disposal result from icons on the device,
or more precisely, on the package. Description of each
meaning can be found in the “Marking“ chapter.
Operating Staff Requirements
The operating staff must thoroughly read the operating
instructions before using the machine.
Qualification
No additional qualification is needed for using the device
apart from detailed training by a person with expert
knowledge.
Minimum Age
The device may only be operated by persons that have
reached 16 years of age.
An exception includes device use by juveniles within job
preparation for purpose of reaching skills under
instructor's supervision.
Training
Appropriate training is only needed for device use. No
special training is necessary.
Transportation and Storage
If the device is stored for a longer period of time it
needs to be thoroughly cleaned and stored so that it
was not accessible to unauthorised persons.
The compressor must never be stored or transported
laying or under pressure!
Pressure in the air jet may be reduced at
compressed air cooling.
Power supply
Only 400-volt devices (Fig. 4):
Be sure to rotation (see arrow Motor eighth) of
the motor, as a corrupt operation in the wrong
direction, the oil pump.
In this case, void the warranty. If necessary, change
direction by reversing the polarity of the plug. See figure
(only for three-phase models)!
In case of problems, contact a specialist.
Assembly / First Putting into Operation
If the compressor is supplied without wheels assemble it with a
screw wrench according to
pic. 2
. The sequence of screws, nuts
and washers is evident from
pic. 2
. In case of need, a rubber foot
also needs to be screwed on. Jointing materials, such as screws,
nuts, etc. are included in the supply.
Visser le filtre à air sur les deux côtés dans le thread approprié
(12).
Transport stopper of the oil tank needs to be exchanged for
throat for oil adding and correct oil level needs to be ensured
(see the "Handling Throat for Oil Adding and Oil Level
Inspection" chapter) before putting the compressor into
operation)
Check the oil level at every startup (pic. 3).
Handling
The compressor may be put into operation after reading and
understanding the
general safety instructions and safety
instructions.
Proceed as follows:
Switching the appliance on
Connect the compressor power cord to the electrical
network.
Pull the switch (1) up.
The compressor is fitted with an automatic pressure switch
that switches the compressor off after reaching the upper
operating pressure and switches it automatically on again
when air is needed again. Switching pressure 6 bar, max.
pressure 8 bar.
Operating pressure control
The operating pressure can be set in an easy way. If turning
the knob (2) in the + direction, the operating pressure
increases. If turning in the – direction, the operating pressure
decreases. The operating pressure can be fixed by
tightening the lock ring.
The compressor is fitted with an automatic safety valve that
releases pressure in case of overpressure. The air nozzle
can be depressurized manually by pulling the ring on the
valve (10).
Switching the appliance off
The compressor must always be switched off by the switch
(1) and when you do not intend to use the appliance then
disconnect it from mains.
Remove the transport oil peg, add oil to the neck and make sure
there is appropriate oil level, using the oil gauge included in the
supply.
The filter insert should be cleaned from time to time. Remove the
foam filter. It can be cleaned by warm soap water solution. Dry
the foam filter and refit it.
Throat for Oil Adding and Oil Level Inspection
Transport stopper needs to be exchanged for throat for oil adding
and correct oil level needs to be ensured before putting the
compressor into operation.
Check the oil level at every startup!!!
Oil change
Since arriving on the piston can chip, it is absolutely necessary
after the first 10 hours of operation to carry out an oil change. We
recommend that you are our compressor (SKU: 40056). Later,
depending on the operation of the compressor, all 100 to 200
hours of operation an oil change place. In order to carry out oil
changes, open the drain screw (13) and begin the process of
waste oil in a suitable container.
13