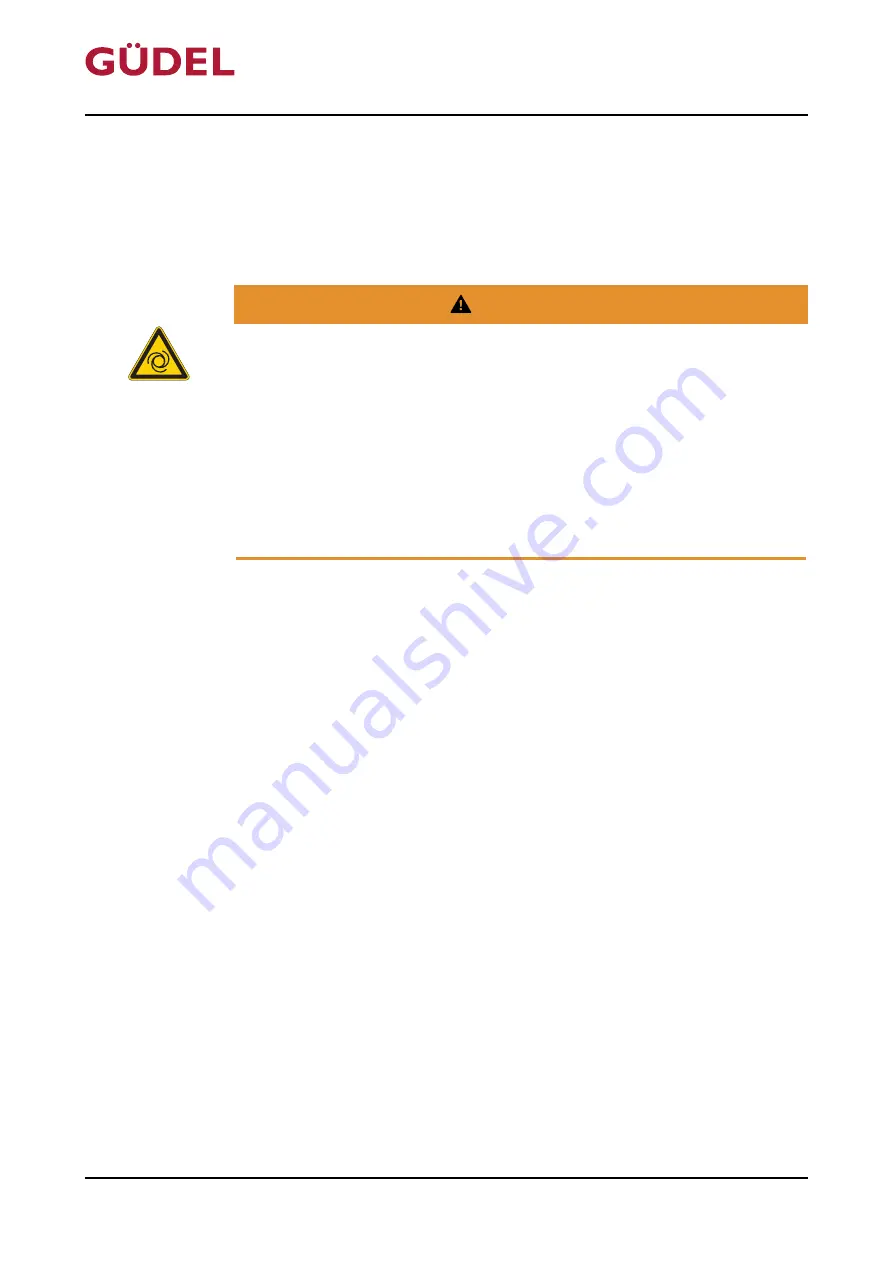
6.3
Safety
Only perform the tasks described in this chapter after you have read and un-
derstood the chapter "Safety".
It concerns your personal safety!
WARNING
Automatic startup
During work on the product, there is danger of the machine starting up auto-
matically. This can lead to severe or fatal injuries!
Before working in the danger area:
• Secure vertical axes (if equipped) against falling.
• Switch off the superordinate main power supply. Secure it against being
switched on again (main switch for the complete system)
• Before switching on the system again, make sure that no one is in the dan-
ger area
Operation
OPERATING MANUAL Automatic lubrication system
FlexxPump 402 / 402B
90071992656444683_v9.0_
EN-US
64