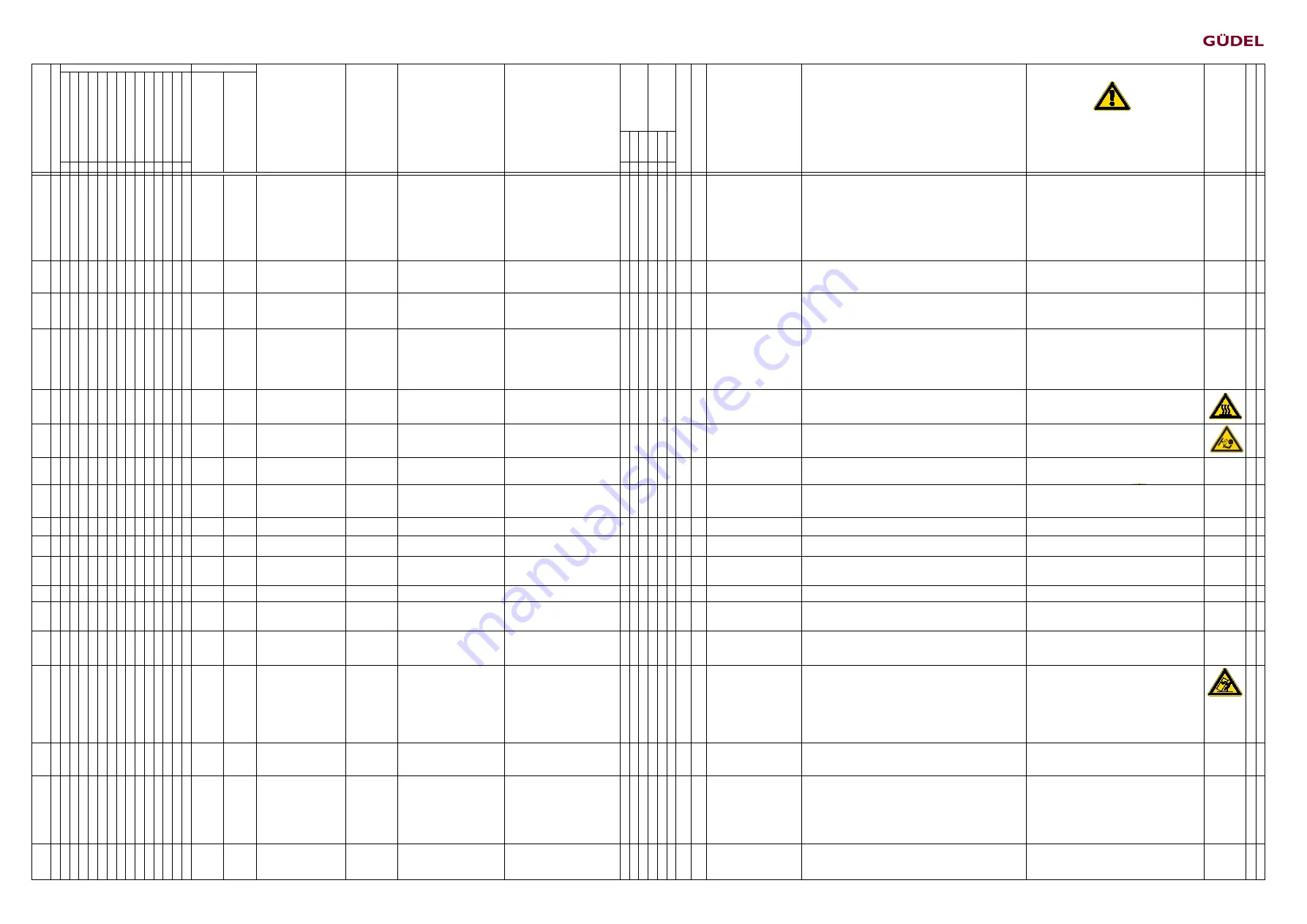
Author: Alain Thurner
Created: 12/11/2009
Process owner: Martin Knuchel
Released: 16.03.2018 / Version 34
Page 2 of 3
Risikobeurteilung_EN_V34.xlsx
M
inor
M
oder
at
e
S
ev
er
e
Ra
re
Ofte
n
F
requent
A
B
C
D
E
F
G
H
I
J
K
L
M
1
4
10
1
2
3
The following should be
prevented:
F
loor
-m
ount
ed dr
iv
e ax
is
R
ai
sed dr
iv
e ax
es
Recommendation to avoid residual risks
Hazard analysis / risk analysis
Machine type: all modules with/without control system
A
ffec
ted per
son(
s)
C
or
res
pondi
ng oper
at
ing
m
ode
Triggering factor
Event
(worst case)
(without protective measures)
S
et
up /
C
hangeov
er
C
leani
ng
T
roubl
es
hoot
ing /
R
epai
r
M
ai
nt
enanc
e
Dis
as
se
m
bly
D
is
pos
al
Source of danger
E
xt
ent
of
the
dam
age
C
at
egor
y /
P
Lr
(
S
IL)
m
ini
m
al
Risk assessment / safety goals / protective measures / residual risks
1)
Solution suggested to the customer (cursive, Times New Roman)
Güdel solution (Arial)
S
af
et
y r
equi
rem
ent
ful
fil
led [
Y
/N
]
O
per
at
ing m
anual
Protective measures
(existing protective measures)
Danger
symbol
Safety goal
(negation of the event)
P
robabi
lit
y of
oc
cur
renc
e
R
is
k as
ses
sm
ent
(
<=
3;
4-
8;
9-
20;
>
20
Int
er
nal
as
sem
bl
y
Special operating modes
N
or
m
al
oper
at
ion
H
az
ar
d no.
Int
er
nal
c
om
m
is
si
oni
ng
Int
er
nal
di
sas
sem
bl
y
C
om
m
is
si
oni
ng at
the
T
rai
ni
ng at
the c
us
tom
er
T
rans
por
t
A
ss
em
bl
y at
the c
us
tom
er
Application area
1.13
x x x
x
Suspended loads
(vertical axes, telescope
axes, counter balance
cylinders, and workpieces)
Maintenance
personnel,
cleaning
personnel
Unexpected start-up
Defective motor brake
Torn belt (telescope axis)
Pressure drop (load balance)
General problems in the drive train
Disassembly of the vertical axis
motor
Person is surprised by unexpected
situation and injured as a result.
x x
10 3/d Persons injured by vertical
axes falling down.
Workpieces have to be deposited beforehand in automatic or setup mode.
The system must be brought into a safe state (emergency off).
Vertical axes have to be secured with the supplied locking pins for the vertical axes
or with the transport securing device.
Appropriate safety devices (cables, auxiliary supports etc.) must be used to secure
telescope axes against falling down.
Avoid walking under suspended workpieces or vertical axes. Take
special care with telescope axes. Inspect belts for cracks and
tears before every maintenance procedure.
Workpieces must be deposited beforehand in automatic or setup
mode.
Vertical axes must be secured with the supplied locking pins for
the
vertical axes or with the transport securing device.
Appropriate safety devices (cables, auxiliary supports etc.) must
be used to secure telescope axes against falling down.
x Y
1.14
x
x x x
x x x x x
x
x
Risk of injury (cutting,
crushing) gearbox, racks
Technician,
commissioning
technician,
forwarding
Carelessness
Cutting injuries, crush injuries
x
x
1
1/b Cutting and crush injuries
occur
Wearing proper protective clothing
Application-specific protective measures
Y
1.15 x
x
x
x
x
x
Rotating parts
All
Contact with rotating parts
Persons are injured
x x
10 3/d Injuries occur
Attach protective cover or warning symbol
Wearing protective clothing
x Y
1.16 x
x
x
Manual workstations
Operators
Automatic movements at the
manual workstation
Someone is surprised by the
automation, body parts are crushed
and injuries result.
x
x
20 3/d Operating personnel or third
parties are injured during the
manual insertion or ejection of
the workpieces.
Insertion or ejection axes may only be moved in jog mode or with two-hand
operation. The drive configuration is such that only a slow axis speed is achieved
at maximum speed of the drive motor. The operating elements for insertion and
ejection must be configured so that the operator has a clear view of the movement
and cannot be endangered. Areas where body parts could be crushed are to be
prevented with design measures to the greatest possible extent.
Extra attention is required of the operator at manual
workstations.
Only perform movements if no other person is in the danger area
and none of your own body parts are in the line of danger of the
corresponding axis
x Y
1.17 x
x x
x x x x x x x
x
x
Hot surfaces.
All
During normal operation,
touching hot surfaces.
Person is injured by hot surface.
x
x
8
2/c Persons suffer burns.
Hot surfaces are covered by mechanical protective devices or marked by the
operator.
None
x Y
1.18 x x x x
x x x x x x x x
x
x
Hot oil squirted out due to
high pressure at the gearbox
All
Overload or non-compliance with
the intended use
Burns or eye injuries
x x
10 3/d Oil comes out.
Use of the product within the defined parameters.
Wearing protective clothing, in particular helmet, goggles, and
shoes
x Y
1.19
x
x
x
x
x
No, wrong, or insufficient
oil
Technician,
maintenance
personnel
Improper oil change
Failure of the transfer function as well
as increased temperature, resulting in
damage and injuries
x x
10 3/d Consequential damage occurs,
with injuries
Maintenance instructions must be observed
None
x Y
1.20 x x x
x x
x x x x
x
x
Oil running out due to leaks
All
Failure of the gasket
Environmental damage, slipping
hazard as well as consequential
damage due to the insufficient oil (see
1.18)
x x
10 3/d The occurrence of
consequential damage with
injuries and environmental
damage
Maintenance intervals must be maintained
Application-specific protective measures
x Y
1.21 x
x
x
x x
x
x
Wear (tooth breakage)
gearbox
All
Tooth breakage
Transfer function fails, resulting in
consequential damage with injuries
x x
10 3/d Consequential damage occurs,
with injuries
Maintenance intervals must be maintained
Application-specific protective measures
x Y
1.22 x
x
x
x
x
Noise
All
Overload or non-compliance with
the intended parameters
Unpleasant noise level, difficult
communication
x
x
2
1/b Excessive noise level occurs
Use of the product within the defined parameters. Vibrations and resonances must
be prevented.
None
Y
1.23 x
x x x x
x
x
Malfunction of protection
measures
Operator,
Maintenance
personnel
Aging, fatigue fracture, failure due
to vibration or overloading
Someone is surprised by the
unexpected situation and injured as a
result
x x
10 3/d A preventable hazard occurs.
The plant is equipped with emergency stop devices that trigger an emergency stop
of the plant. A lock-out (overview of the switch off locations) draws attention to the
switch-off devices.
Do not walk under suspended workpieces or vertical axes. Only
possible in setup mode. Permanent workstations are not
permitted in the direction of movement of the axes.
x Y
1.24
x
x x x x x x x x
x
Slipping
All
Inattention and/or careless
operation
Persons are injured
x
x
4
2/c Injuries occur
For the option of walkable drive axes, use anti-slip plates.
Otherwise, walking on the drive axis is contrary to intended use.
None
x Y
1.25
x
x x x x x x x x
x
x
Danger of tripping
All
Inattention and/or careless
operation
Persons are injured
x
x
4
2/c Injuries occur
Customer must provide for sufficient protection in accordance with the ambient
conditions.
None
x Y
1.26
x
x
x
x
Faulty assembly
All
Incorrectly assembled plant
Someone is surprised by the
unexpected situation and injured as a
result
x x
10 3/d The module is mounted
incorrectly.
The content of the operating manual is known to the technicians.
Before a Güdel device is transported to the location of use, unpacked, assembled,
and commissioned, the operating manual must first be read and understood.
None
x Y
1.27
x
x
x
x
Loss of stability
All
Inattention and/or careless
operation
Machine/plant tips over
x x
10 3/d It is possible for the module to
tip or equipment to fall down.
Equipment without base supports:
To connect to customer supports, the specified screw configuration according to
the Güdel layout has to be used with the corresponding screws.
Equipment with base supports:
The supplied screws for assembly have to be used. For the connection of the
supports to the floor, the anchoring suggestion according to the Güdel layout
needs to be taken into consideration.
Fall protection has to be mounted for area gantries.
The operating manual must be read and understood.
Check the connections that are responsible for the stability of the
device before starting the plant.
x Y
1.28
x
x
x
Improper disposal can cause
environmental damage.
All
Disposal regulations are not
observed
Environmental hazard
x x
10 3/d The device and its
consumables are not disposed
of properly at the end of their
service life.
National regulations regarding disposal of the plant must be observed.
None
x Y
1.29
x
x
x
Malfunction of the control
system
Setters
Failure of control unit components Someone is surprised by the
unexpected movement and injured as
a result
x x
10 3/d The risk of potential hazards
becomes too high.
Only drive systems are used that comply with the state of the art and the standards
referenced in the machine directive.
Work in this mode requires a high level of individual
responsibility from the operator/setter.
There is no way to completely ensure that a malfunction of the
control system does not create a hazard by moving the axes.
The operator must therefore try to never be in the possible
direction of travel of the axes and ensure that no third parties are
in the possible danger zones.
x Y
1.30 x
x
x
Malfunction of the control
system
Operator,
Maintenance
personnel
Failure of control unit components Someone is surprised by the
unexpected movement and injured as
a result
x x
10 3/d The effects of a control system
malfunction endanger the
operator or third parties.
The areas of movement are to be enclosed by mechanical safety fences, light
curtains and light grids so that it is not possible to enter this area from any side.
Movements must transition to static states as quickly as possible.
In normal operation, all protective hoods must be closed,
removable protective hoods must be screwed securely.
Required conduct: Inspect the protective hoods before starting
normal operation.
x Y
Summary of Contents for MLB 1-3 V2
Page 4: ...Revision history OPERATING MANUAL MLB 1 3 V2 881017611_v1 0_EN US 4 ...
Page 14: ...Table of contents OPERATING MANUAL MLB 1 3 V2 881017611_v1 0_EN US 14 ...
Page 86: ...Operation OPERATING MANUAL MLB 1 3 V2 881017611_v1 0_EN US 86 ...
Page 159: ...9 4 Maintenance schedules Maintenance OPERATING MANUAL MLB 1 3 V2 881017611_v1 0_EN US 159 ...
Page 160: ...Maintenance OPERATING MANUAL MLB 1 3 V2 881017611_v1 0_EN US 160 ...
Page 162: ...Maintenance OPERATING MANUAL MLB 1 3 V2 881017611_v1 0_EN US 162 ...
Page 164: ...Maintenance OPERATING MANUAL MLB 1 3 V2 881017611_v1 0_EN US 164 ...
Page 166: ...Maintenance OPERATING MANUAL MLB 1 3 V2 881017611_v1 0_EN US 166 ...
Page 170: ...Maintenance OPERATING MANUAL MLB 1 3 V2 881017611_v1 0_EN US 170 ...
Page 172: ...Maintenance OPERATING MANUAL MLB 1 3 V2 881017611_v1 0_EN US 172 ...
Page 174: ...Maintenance OPERATING MANUAL MLB 1 3 V2 881017611_v1 0_EN US 174 ...
Page 176: ...Maintenance OPERATING MANUAL MLB 1 3 V2 881017611_v1 0_EN US 176 ...
Page 178: ...Maintenance OPERATING MANUAL MLB 1 3 V2 881017611_v1 0_EN US 178 ...
Page 180: ...Maintenance OPERATING MANUAL MLB 1 3 V2 881017611_v1 0_EN US 180 ...
Page 206: ...Repairs OPERATING MANUAL MLB 1 3 V2 881017611_v1 0_EN US 206 ...
Page 212: ...Decommissioning storage OPERATING MANUAL MLB 1 3 V2 881017611_v1 0_EN US 212 ...
Page 217: ...13 Spare parts supply Spare parts supply OPERATING MANUAL MLB 1 3 V2 881017611_v1 0_EN US 217 ...
Page 218: ...Spare parts supply OPERATING MANUAL MLB 1 3 V2 881017611_v1 0_EN US 218 ...
Page 224: ...Spare parts supply OPERATING MANUAL MLB 1 3 V2 881017611_v1 0_EN US 224 ...
Page 234: ...List of illustrations OPERATING MANUAL MLB 1 3 V2 881017611_v1 0_EN US 234 ...
Page 238: ...List of tables OPERATING MANUAL MLB 1 3 V2 881017611_v1 0_EN US 238 ...
Page 246: ...Index OPERATING MANUAL MLB 1 3 V2 881017611_v1 0_EN US 246 ...
Page 248: ...Appendix OPERATING MANUAL MLB 1 3 V2 881017611_v1 0_EN US ...
Page 249: ...Hazard analysis Risk analysis Appendix OPERATING MANUAL MLB 1 3 V2 881017611_v1 0_EN US ...
Page 250: ...Appendix OPERATING MANUAL MLB 1 3 V2 881017611_v1 0_EN US ...
Page 255: ...Appendix OPERATING MANUAL MLB 1 3 V2 881017611_v1 0_EN US ...
Page 258: ...Technical data Appendix OPERATING MANUAL MLB 1 3 V2 881017611_v1 0_EN US ...
Page 259: ...Appendix OPERATING MANUAL MLB 1 3 V2 881017611_v1 0_EN US ...
Page 260: ...Layout Appendix OPERATING MANUAL MLB 1 3 V2 881017611_v1 0_EN US ...
Page 261: ...Appendix OPERATING MANUAL MLB 1 3 V2 881017611_v1 0_EN US ...
Page 262: ...Spare parts lists Appendix OPERATING MANUAL MLB 1 3 V2 881017611_v1 0_EN US ...
Page 263: ...Appendix OPERATING MANUAL MLB 1 3 V2 881017611_v1 0_EN US ...
Page 264: ...Options Appendix OPERATING MANUAL MLB 1 3 V2 881017611_v1 0_EN US ...
Page 265: ...Appendix OPERATING MANUAL MLB 1 3 V2 881017611_v1 0_EN US ...
Page 266: ...Third party documentation Appendix OPERATING MANUAL MLB 1 3 V2 881017611_v1 0_EN US ...
Page 267: ...Appendix OPERATING MANUAL MLB 1 3 V2 881017611_v1 0_EN US ...