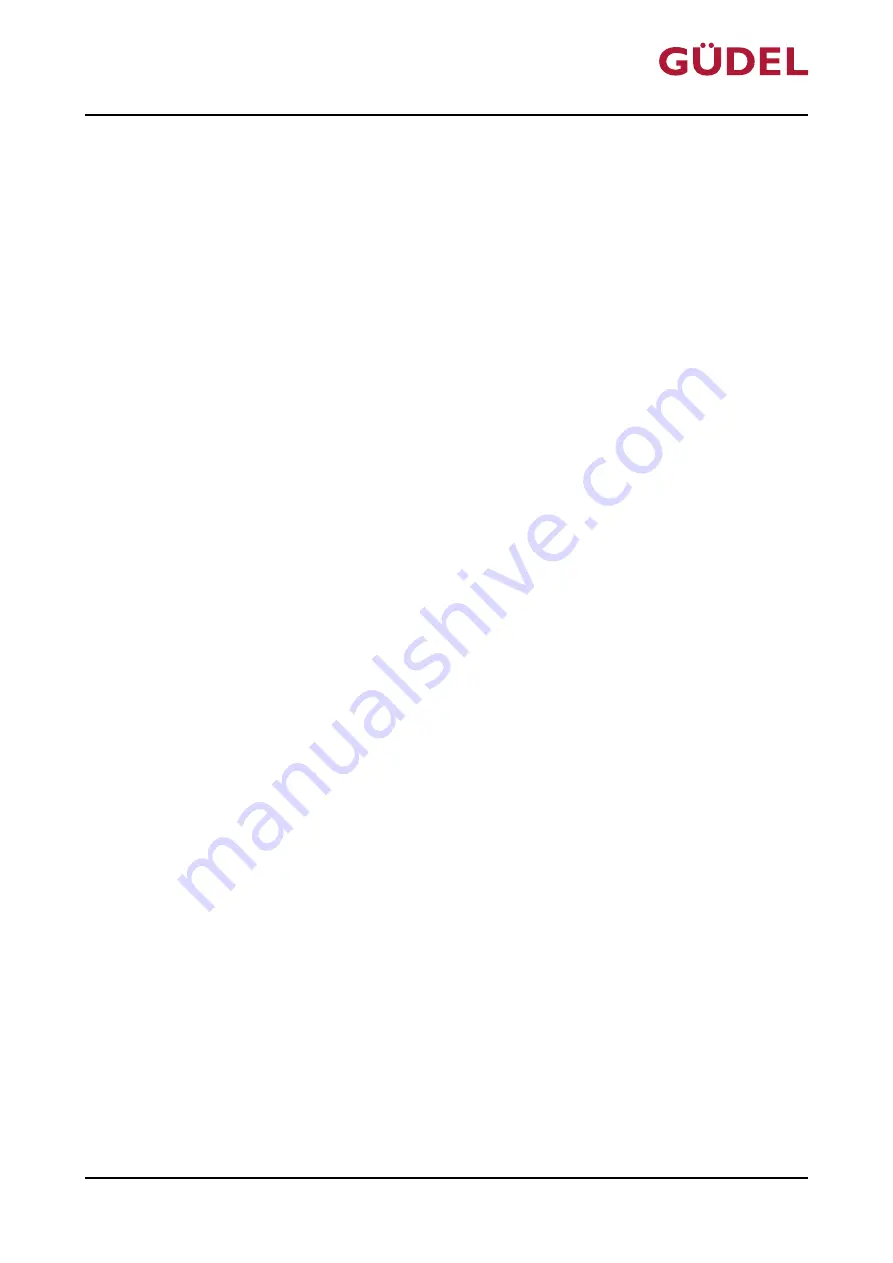
7.5
Installing
7.5.1
Installing the motor
7.5.1.1
Information on initial assembly
The range of motors for the gearbox unit is very broad. The same applies to
the dimensions of the motor shafts. A design solution was selected that al-
lowed for the greatest variety of motor to be mounted on the gearbox unit.
The increased expense for the initial assembly was consciously taken into ac-
count. It normally occurs only once during the entire service life of the gear-
box unit. For maintenance tasks and repair, the motor is simply disassembled
and remounted with one half of the elastomer coupling.
7.5.1.2
Prerequisites
Three conditions must be fulfilled simultaneously to allow you to install the
motor on the gearbox unit:
• The gearbox flange is aligned to allow the coupling screws to be tightened
through the drill holes of the gearbox flange with a torque wrench
• The input shaft with installed wedge must be positioned with the coupling
attached to allow the coupling screws to be tightened through the drill
holes of the gearbox flange
• In the event of angled motor flanges, the motor must be aligned to the mo-
tor flange to allow the motor screws to be fitted and tightened
Commissioning
OPERATING MANUAL MLB 1-3 V2
881017611_v1.0_
EN-US
51
Summary of Contents for MLB 1-3 V2
Page 4: ...Revision history OPERATING MANUAL MLB 1 3 V2 881017611_v1 0_EN US 4 ...
Page 14: ...Table of contents OPERATING MANUAL MLB 1 3 V2 881017611_v1 0_EN US 14 ...
Page 86: ...Operation OPERATING MANUAL MLB 1 3 V2 881017611_v1 0_EN US 86 ...
Page 159: ...9 4 Maintenance schedules Maintenance OPERATING MANUAL MLB 1 3 V2 881017611_v1 0_EN US 159 ...
Page 160: ...Maintenance OPERATING MANUAL MLB 1 3 V2 881017611_v1 0_EN US 160 ...
Page 162: ...Maintenance OPERATING MANUAL MLB 1 3 V2 881017611_v1 0_EN US 162 ...
Page 164: ...Maintenance OPERATING MANUAL MLB 1 3 V2 881017611_v1 0_EN US 164 ...
Page 166: ...Maintenance OPERATING MANUAL MLB 1 3 V2 881017611_v1 0_EN US 166 ...
Page 170: ...Maintenance OPERATING MANUAL MLB 1 3 V2 881017611_v1 0_EN US 170 ...
Page 172: ...Maintenance OPERATING MANUAL MLB 1 3 V2 881017611_v1 0_EN US 172 ...
Page 174: ...Maintenance OPERATING MANUAL MLB 1 3 V2 881017611_v1 0_EN US 174 ...
Page 176: ...Maintenance OPERATING MANUAL MLB 1 3 V2 881017611_v1 0_EN US 176 ...
Page 178: ...Maintenance OPERATING MANUAL MLB 1 3 V2 881017611_v1 0_EN US 178 ...
Page 180: ...Maintenance OPERATING MANUAL MLB 1 3 V2 881017611_v1 0_EN US 180 ...
Page 206: ...Repairs OPERATING MANUAL MLB 1 3 V2 881017611_v1 0_EN US 206 ...
Page 212: ...Decommissioning storage OPERATING MANUAL MLB 1 3 V2 881017611_v1 0_EN US 212 ...
Page 217: ...13 Spare parts supply Spare parts supply OPERATING MANUAL MLB 1 3 V2 881017611_v1 0_EN US 217 ...
Page 218: ...Spare parts supply OPERATING MANUAL MLB 1 3 V2 881017611_v1 0_EN US 218 ...
Page 224: ...Spare parts supply OPERATING MANUAL MLB 1 3 V2 881017611_v1 0_EN US 224 ...
Page 234: ...List of illustrations OPERATING MANUAL MLB 1 3 V2 881017611_v1 0_EN US 234 ...
Page 238: ...List of tables OPERATING MANUAL MLB 1 3 V2 881017611_v1 0_EN US 238 ...
Page 246: ...Index OPERATING MANUAL MLB 1 3 V2 881017611_v1 0_EN US 246 ...
Page 248: ...Appendix OPERATING MANUAL MLB 1 3 V2 881017611_v1 0_EN US ...
Page 249: ...Hazard analysis Risk analysis Appendix OPERATING MANUAL MLB 1 3 V2 881017611_v1 0_EN US ...
Page 250: ...Appendix OPERATING MANUAL MLB 1 3 V2 881017611_v1 0_EN US ...
Page 255: ...Appendix OPERATING MANUAL MLB 1 3 V2 881017611_v1 0_EN US ...
Page 258: ...Technical data Appendix OPERATING MANUAL MLB 1 3 V2 881017611_v1 0_EN US ...
Page 259: ...Appendix OPERATING MANUAL MLB 1 3 V2 881017611_v1 0_EN US ...
Page 260: ...Layout Appendix OPERATING MANUAL MLB 1 3 V2 881017611_v1 0_EN US ...
Page 261: ...Appendix OPERATING MANUAL MLB 1 3 V2 881017611_v1 0_EN US ...
Page 262: ...Spare parts lists Appendix OPERATING MANUAL MLB 1 3 V2 881017611_v1 0_EN US ...
Page 263: ...Appendix OPERATING MANUAL MLB 1 3 V2 881017611_v1 0_EN US ...
Page 264: ...Options Appendix OPERATING MANUAL MLB 1 3 V2 881017611_v1 0_EN US ...
Page 265: ...Appendix OPERATING MANUAL MLB 1 3 V2 881017611_v1 0_EN US ...
Page 266: ...Third party documentation Appendix OPERATING MANUAL MLB 1 3 V2 881017611_v1 0_EN US ...
Page 267: ...Appendix OPERATING MANUAL MLB 1 3 V2 881017611_v1 0_EN US ...