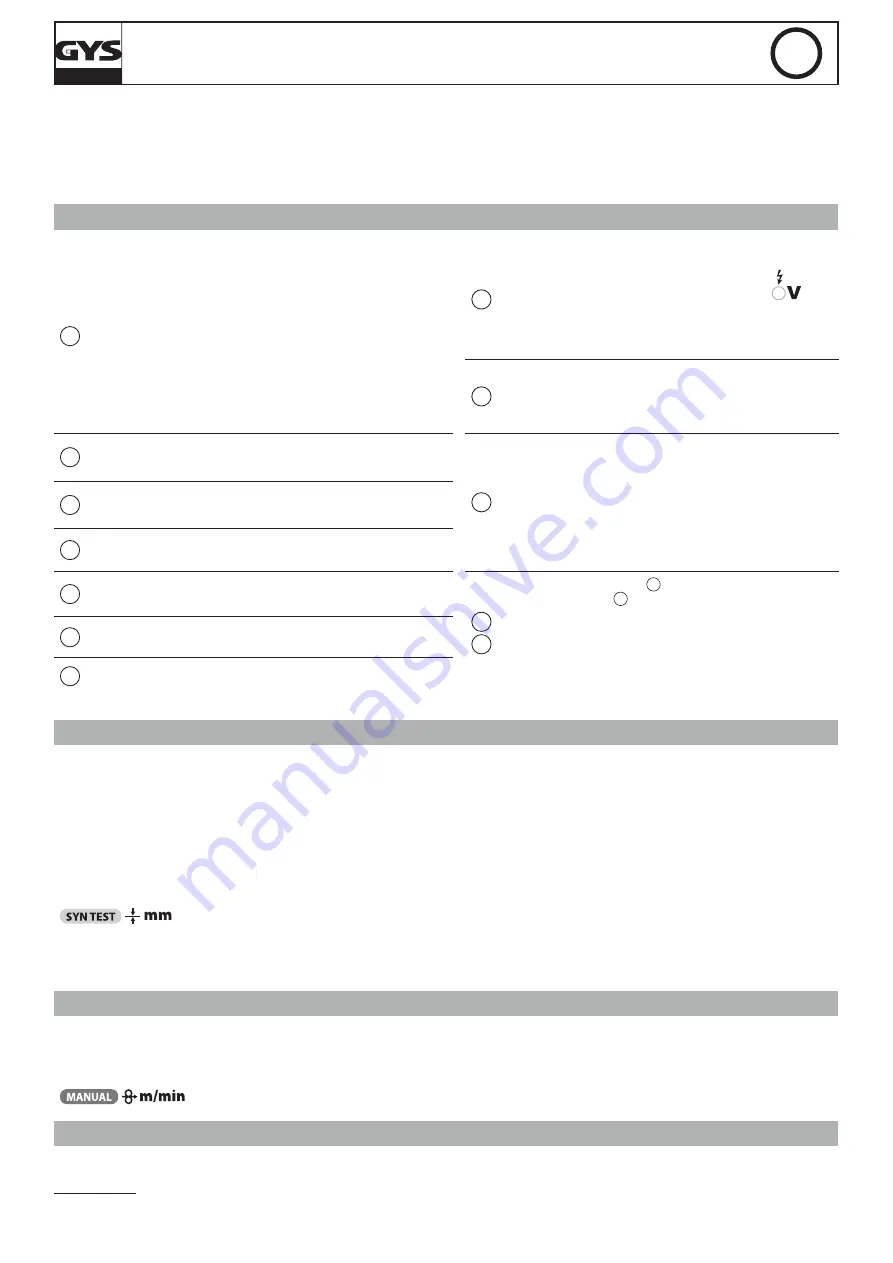
18
MAGYS 400-4 / 400 GR / 500 GR / 500 WS
EN
• Always respect the basic rules of welding.
• Do not block/cover the ventilation holes of the machine.
• Leave the device plugged in after welding to allow proper cooling down.
• Thermal protection: The LED(8) switches on when the unit is on safety mode. The cooling time (forced ventilation) is by cycle of 10 minutes for the
400-4 and 20 minutes (forced venti pump) for the MAGYS 400 GR/500 GR/500 WS depending on the external temperature.
• Ventilation: the fan is only active during the welding and the cooling cycles.
CONTROL PANEL (FIG-4)
1
Welding mode selection / test:
- 2T: two-stage welding / 4T: four-stage welding.
- SPOT: Spot welding with adjustable spot diameter
- Delay: intermittent welding modes for an optimised operating
procedure
2 modes to make easier the setting up of the welding unit: «
Manual » or « Synergic ».
- Test function: The LED switches on when you push the button
(1). Read chapter «Welding unit settings»
Access to the hidden mode and Expert mode setting
(see next page)
9
Voltage display: By pulling the trigger (The LED
indicates that your torch is on) the voltage will be displayed
according to the parameters selected.
12
Power adjustment switch:
20 positions for the Magys 400-
4, 400 GR and 30 for the 500 GR / 500 WS.
3
SPOT / DELAY potentiometer:
To adjust the welding time of a
point, the size of the point and the time between each point.
2
Wire speed setting:
Potentiometer to adjust the wire speed.
The speed can vary from 1 to 24 m/minute.
Note
for the MAGYS 400 GR/500 GR/500 WS: It is possible to
select either the potentiometer of the separate wire feeder or
the generator.
See chapter «wire speed potentiometer» and the sticker inside
the wire feeder
4
Arc dynamics potentiometer: To adjust automatically or
manually the arc dynamics.
5
Metal selection and manual mode:
Read chapter «Welding
unit settings»
6
Mode « Synergic »: Read chapter «Welding unit settings»
10
11
Welding current display
10
:
indicates the amperage (LED «
A ») or the thickness
11
recommended according to the power
selected (read « test » function in the chapter « Welding unit
settings »).
Note:
« NOP » on the display indicates that the welding cur-
rent selected is superior to the one recommended taking into
account the parameters (type and diameter of the wire).
7
Wire diameter:
Select the wire diameter used.
8
Thermal protection LED:
Read chapter «Thermal protection».
WELDING UNIT SETINGS (FIG-4)
« SYNERGIC » MODE
This function automatically controls the wire speed. There is no need to set the wire speed manually.
- Position the potentiometer (2) in the middle of the « Optimal synergic » zone
- Select: Wire type (5), wire diameter (7), power mode (with the 2 power switches on the front (12)).
From the settings chosen, the unit determines the optimum wire speed and is ready to weld. It is also possible to manually adjust the wire speed (+
or –) if necessary using the potentiometer (2). The last welding configuration is saved in the memory automatically (wire diameter, wire type, mode).
« Test » function
Only in the synergic mode, I twill indicate you the thickness you can weld with the parameters selected without using
any gas or wire. These values are calculated on the basis of a welding on the flat surface.
Attention:
you have current
in the torch, so avoid any contact with any metallic part.
NOTE:
If the gas, the wire diameter, and the metal used are different from the ones selected in the synergic mode, you will need to switch to the
manual mode to set up the welding unit.
«MANUAL » MODE
To set your device, proceed as follows:
- Choose the welding voltage using the 2 power switches according to the thickness to weld.
- Adjust the wire speed using the potentiometer (12).
When in manual this function displays the wire speed setting on display (10).
MODIFICATION OF THE ORIGINAL PARAMETERS (FIG-4)
The device controls the arcing speed, the burn back and the post gaz. These parameters are set up in the factory, but it is possible to modify them
directly on the circuit board. Attention: this intervention must be done by a qualified electrician.
IMPORTANT :
Make sure the product is not connected to the power supply before any intervention