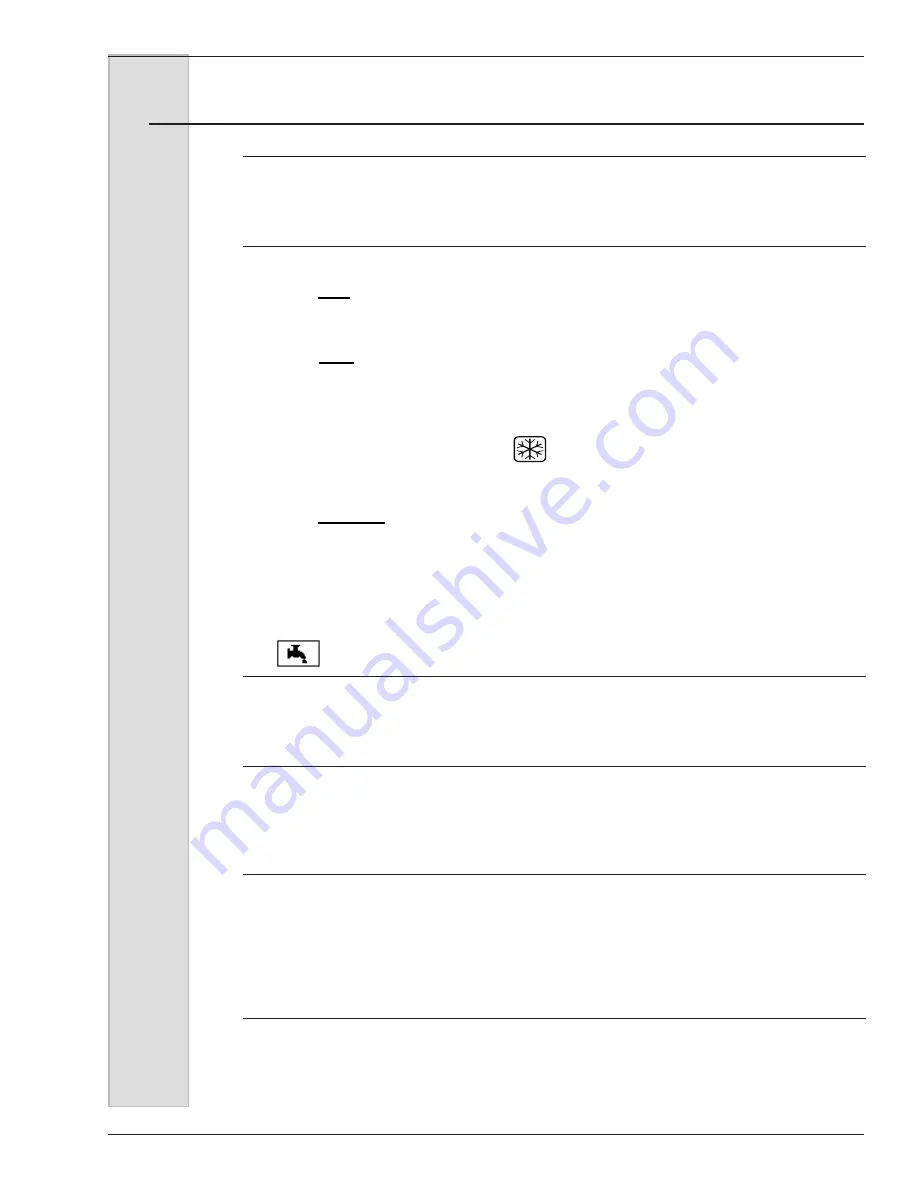
ELECTRO FREEZE Soft Serve Model GEN-5099
185242
15
5. Left or Right side Control Indicator
Left indicates controls for left side cylinder and hopper. “Right” Indicates controls
for right side of freezer cylinder and hopper.
6. Mode of Operation Indicator
There are three primary modes of operation:
a.
OFF
–This is the indicator when power is applied to freezer and when
(OFF) button is pressed. In this mode, the refrigeration and beater motor
will not operate.
b.
FRZ
– This is the indicator when Freeze button is pressed. In this
mode, the freezer is in automatic freeze mode and both the beater motor
and refrigeration will activate as needed. Use this position for dispensing
product from freezer. Cabinet will also be refrigerated as needed to
maintain product below 41°F.
Important:
Do not use the
freeze position with water or sanitizer
in the cylinder or hopper. The freezer will be damaged.
c.
Standby
– This is the indication when the Night button is pressed. In this
mode, an energy-saving feature will activate and reduce product
refrigeration. The freezer will automatically cycle to maintain temperatures
in the cylinder and cabinet below 41°F and keep product from deteriorating.
Use this position when the freezer will not be in use for periods of more
than one hour.
7.
Wash or Clean Mode
Press the function button directly below icon to activate clean mode. Also allows
individual activation of the mix pump & beater.
8. Information Window
This window is normally blank when unit is functioning properly. This window will
give you indication when mix in hopper is low and other error messages. Refer to
Troubleshooting Section of manual for details on error messages.
9. Standby Indicator
This is the indication when the Night button is pressed. In this mode, an energy-
saving feature will activate and reduce product refrigeration. The freezer will
automatically cycle to maintain temperatures in the cylinder and cabinet below 41°F and
keep product from deteriorating. Use this position when the freezer will not be in use for
periods of more than one hour.
10. Hidden Operator Menu Key
Press this key to enter the operator menu to adjust the freezers settings.
5 Operator Controls
(continued)
Summary of Contents for Electro Freeze GENESIS GEN-5099
Page 2: ......
Page 10: ......
Page 18: ...ELECTRO FREEZE Soft Serve Model GEN 5099 8 185242 4 Part Names and Functions...
Page 74: ......
Page 76: ......
Page 88: ...ELECTRO FREEZE Soft Serve Model GEN 5099 12 185242 Figure 11 Side Back View Breakdown...
Page 94: ......
Page 95: ...ELECTRO FREEZE Soft Serve Model GEN 5099 185242 19 O Ring Chart...