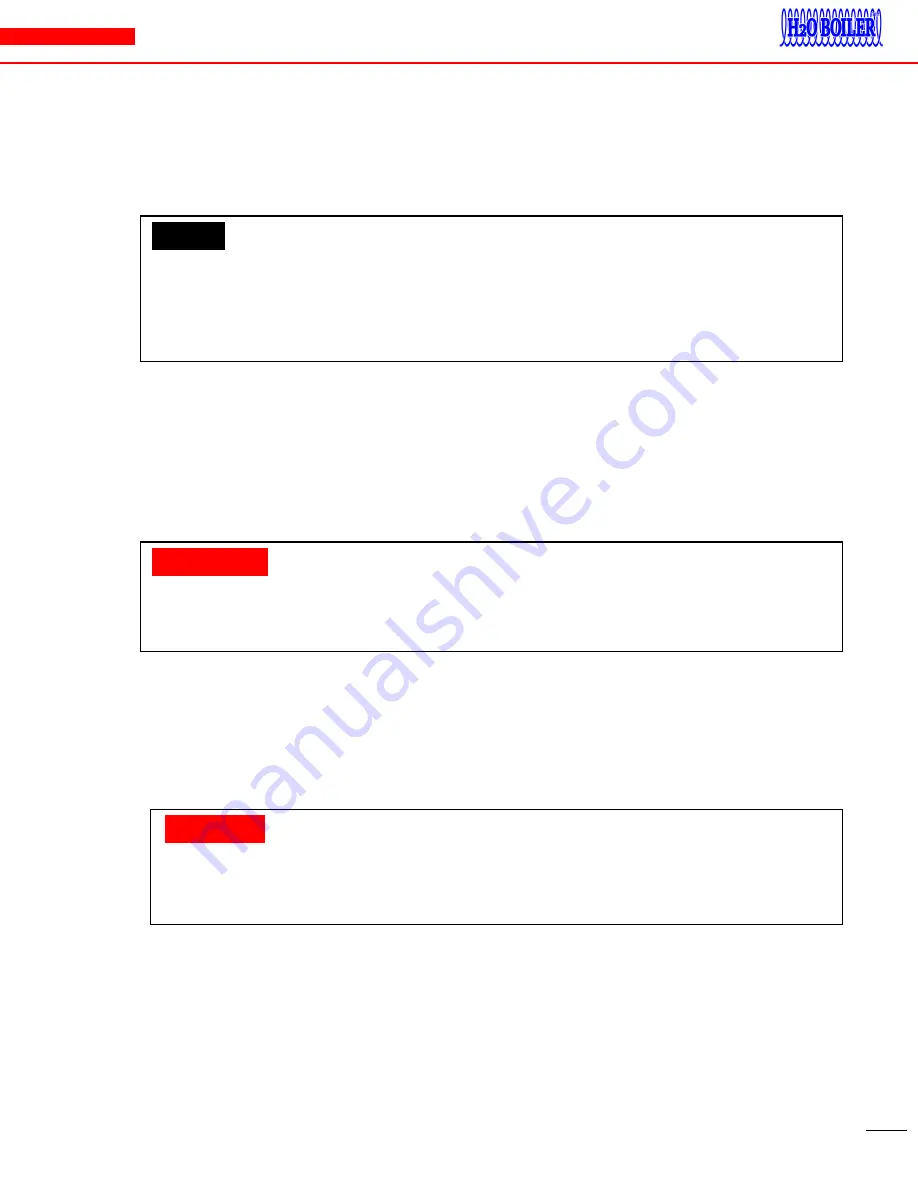
SECTI
O
N
2
: I
NSTA
L
L
AT
IO
N
18
H2O BOILER
HC SERIES IOM Manual
instruments (main gas valve, boiler/water heater gas regulator, and low gas pressure switch) could
be easily isolated and removed, whenever necessary. The valve should be clearly marked, located
outside the unit’s housing, readily visible and accessible for turning on and off. If the unit is to be
installed in, under, or directly attached to a pool, or spa, structure, the said manual valve should be
located outside the structure.
2.9
Electrical connection
If an external electrical source is utilized, the appliance, when installed, must be electrically
grounded in accordance with local codes or, in the absence of local codes, with the
National
Electrical Code
, ANSI/NFPA 70 and/or the CSA C22.1,
Canadian Electrical Code, Part 1
.
2.10
Vent Connection
For US and Canadian installations, vent termination must be in accordance and not less than those
specified in the current ANSI Z223.1/NFPA 54
National Fuel Gas Code
or CSA B149.1,
Natural
Gas and Propane Installation Codes
, as applicable.
Provisions for adequate combustion and ventilation air in accordance with one of the following:
The
National Fuel Gas Code, ANSI Z223.1/NFPA 54
(Current Edition);
CSA B149.1, Natural Gas and Propane Installation Code
(Current Edition); or
Applicable provisions of the local building code.
NOTE:
Inlet gas pressure upstream of the unit must always remain within the 7” – 14” WC
range. The maximum inlet gas pressure must not exceed the value specified by the
manufacturer and that the minimum value listed is for the purposes of input
adjustment.
Warning:
Use of cellular core PVC (ASTM F891), cellular core CPVC, or Radel®
(polyphenylsulfone) in non-metallic venting systems is prohibited.
Covering non-metallic vent pipe and fittings with thermal insulation is prohibited.
CAUTION:
Label all wires prior to disconnection when servicing controls. Wiring errors can
cause improper and dangerous operation. Verify proper operation after servicing.
D-VAC Sales Inc. Email: dmann@dvachvac.com Tel: (516) 256-3131 www.dvachvac.com