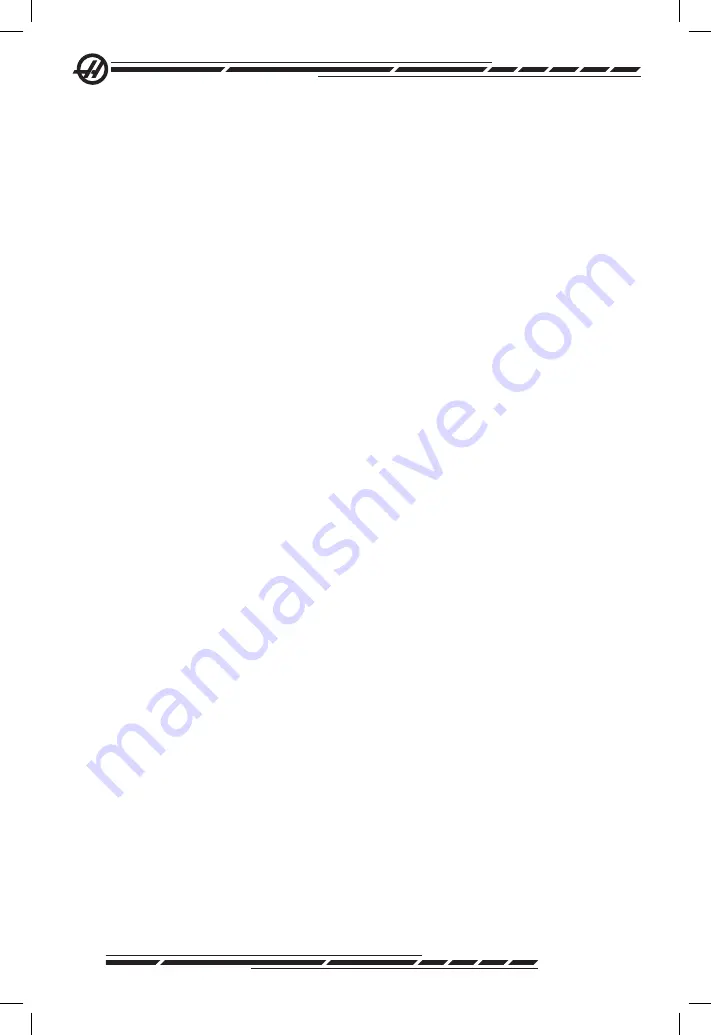
4
96-0041 Rev V
March 2012
Tool Wear
Tool life is dependant upon the following criteria:
• Cutting feedrate
• Tool and workpiece material
• How much material is being removed
• Proper workholding device
• Use of coolants
• Use of correct SFPM (RPM) for tool and material
Tools are subject to gradual wear from the following elements:
Abrasion
(Friction and rubbing removes material from the cutter.)
Caused by:
• Friction on the outside of the cutter as it passes through the material.
Adhesion
High pressure/temperatures weld small chip particles to cutter.
Caused by:
• Low cutting speed
• High feed rate
• Negative cutting geometry
• ‘Sticky’ materials such as some stainless steels and pure aluminum
• Lack of coolants
Chipping
The cutting edge is broken off instead of being worn away.
Caused by:
• Excessive feed rate
• Interrupted cut
• Insert geometry too weak
• Chatter
Cratering
Characterized by a smooth depression on the face of the insert.
Caused by:
• Excessive cutting speed
• Ineffective use of coolant
• Friction
• Normal wear
Oxidation
• Occurs during very high cutting temperatures
• Weakens tool tips
Chemical wear:
Cutter/workpiece reaction begins to corrode insert
(corrosion)
Coolant
There are a number of reasons why coolant is used in the machining process;
it is used to dissipate heat generated during machining, reduces cutter fric-
tion, and promotes chip clearance. It also allows for high speed machining and
increases tool life.
Coolant is not recommended when machining cast iron or steel, or when using
carbide cutters. Carbide cutters can withstand high temperatures but not ther-
mal shock of coolant.