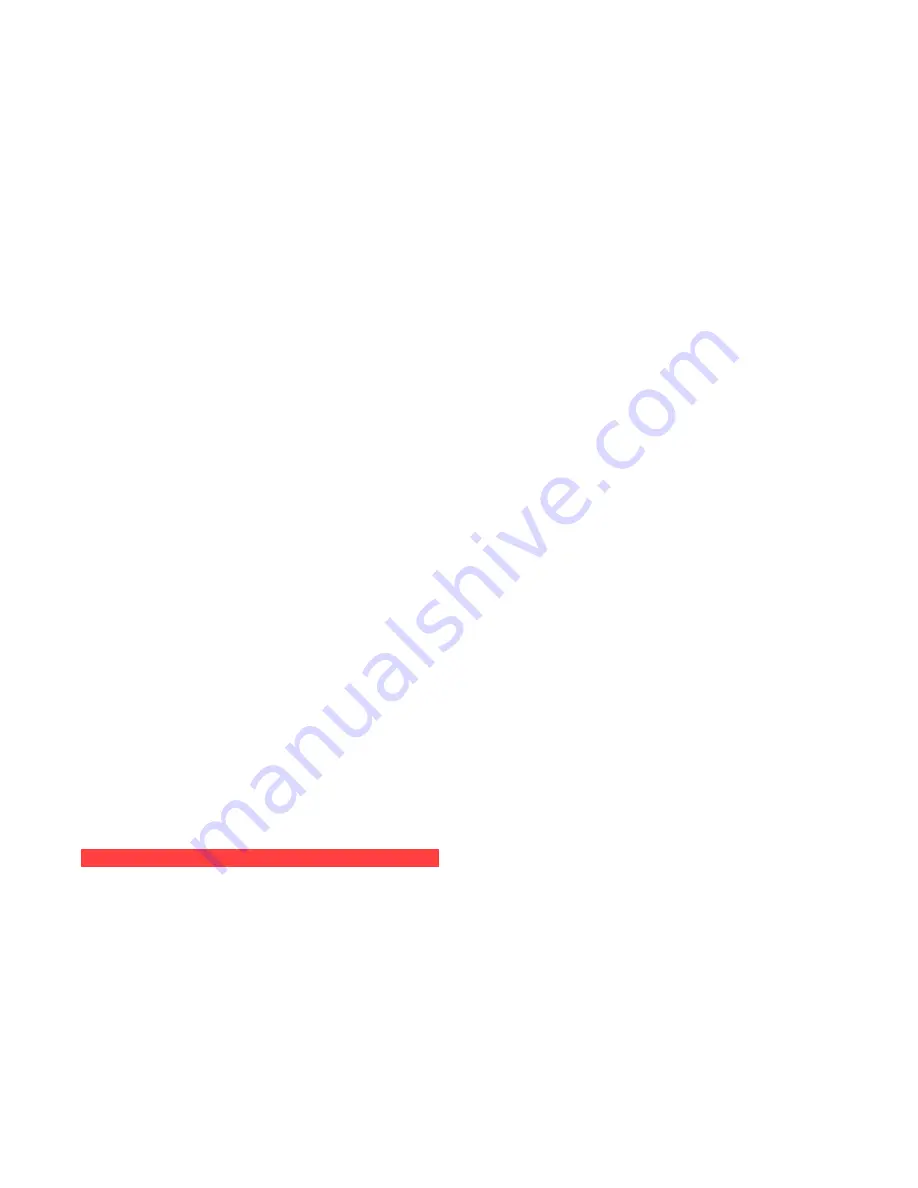
ES0755 rev A 1/11
3
while in use. The anchoring bolts (in accordance with the anchoring instructions) should be installed prior to
the machine being set in place.
The X-axis auger trough must be removed before mating the column base to the table base. The auger trough
will remain off the table base until the leveling and squaring procedures are completed.
The installation process will be further aided if, when each base assembly is set in place, a very rough level-
ing procedure be done. The theoretical distance from the floor to the bottom of the two bases is 2 inches.
The use of a machinist scale or small gauge blocks will expedite the process. While all leveling screws and
leveling pads are in place measure from the floor to the bottom of each base until the distance is very close to
the 2 inch height. This will accomplish two things: First, that the machine is set to the proper height to receive
the coolant tank and, second, that the machine will be very much closer to level than without having done this
procedure.
The installation procedure will necessarily follow the general outline below (a more detailed explanation fol-
lows). Depending on the available space and equipment it may be simpler to place the column base assembly
before the table base assembly. This outline considers that it is easier to place the table base assembly first.
Regardless of which assembly is placed first, the concepts of the general outline need to be adhered to:
• Remove the column base assembly from the truck
• Remove the front shipping bracket (VS machines)
• Stone and clean the table base mating flange
• Stone and clean the column base mating flange
• Remove the table base assembly from the truck and set 12" away from the column
• Remove the X-axis auger trough
• Move the column base to mate with the table base
• Be certain that all connecting bolts are in place but not tightened
• Attach the Pendant and Pendant Arm Support Assembly to the front of the table base
• Run the Pendant electrical wires under the table and connect them in the wire covers on the back of
the table
• Rough level the column base assembly
• Remove the dust covers from the column assembly
• Install the counterbalance cylinder and charge the system
• Remove shipping blocks from the table base assembly
• Connect all air/electrical/oil lines between the two assemblies
• Remove shipping blocks from the column base assembly
• Power up the control
• Fine level the table base assembly
• Fine level/square the column base assembly
• Fully tighten the connecting bolts and adjust fine level/square
• Fully check machine geometry
• Replace the X-axis auger trough
• Install the coolant supply system
• Check all motors for rotation/phasing
s
ettinG
the
m
achine
in
P
lace
Ensure the anchoring preparations are in accordance with the anchoring instructions prior to setting the ma-
chine in place.Use a small amount of grease on the leveling pads before placing the machine.
1. Prepare the table base for mating
• Remove the X-axis auger and auger trough
• Stone and clean thoroughly the mating flange surface. This is an extremely important step
that must be well and properly done before the bases are moved into position with respect
to each other. (Failure to properly prepare the surfaces and preserve their cleanliness may
require separation of the main components for corrective action).
• Clean the holes in the table base.
• Ensure the air/electrical/oil lines and connectors are bundled and safely away from the