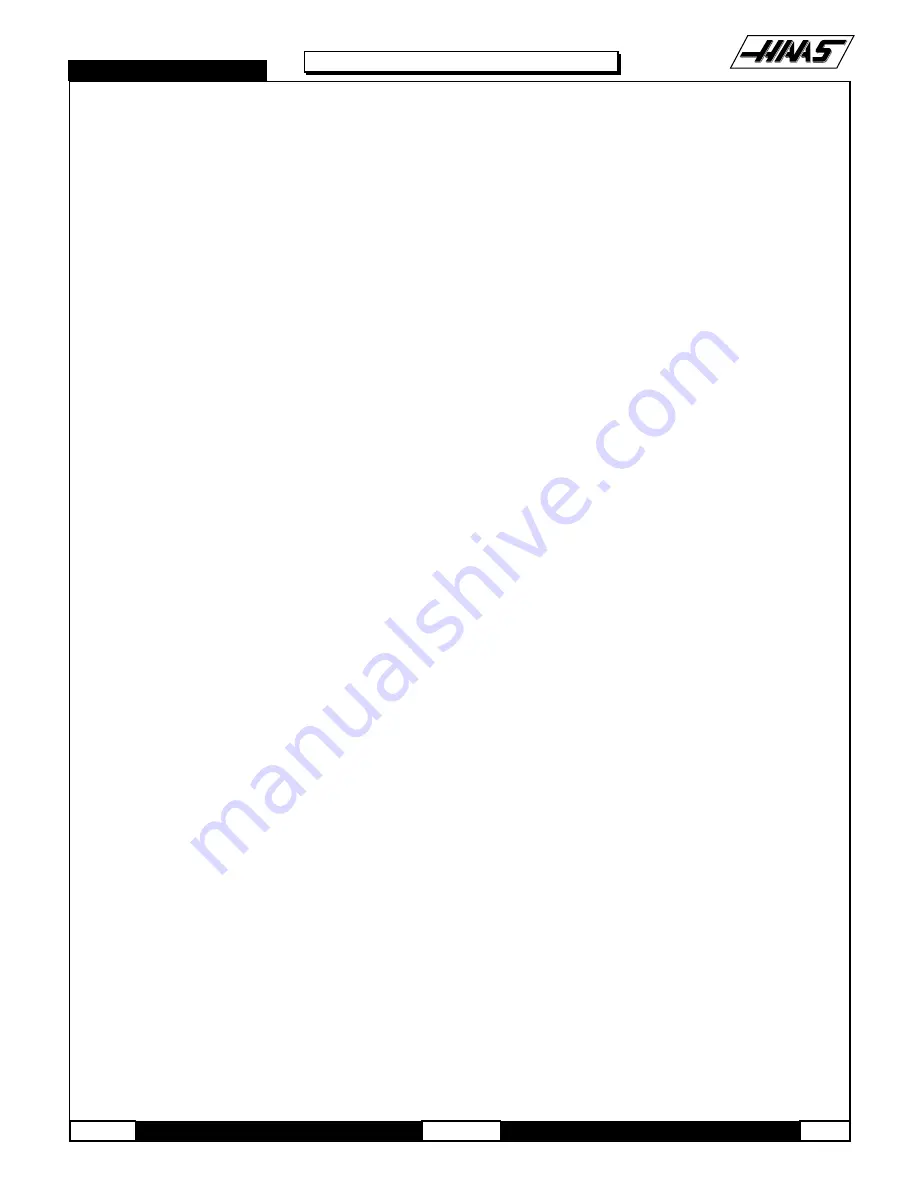
1-15-96
96-8100
15
TABLE OF CONTENTS
HAAS
AUTOMATION, INC.
TROUBLESHOOTING
S E R V I C E M A N U A L
VF-S
ERIES
4. AUTOMATIC TOOL CHANGER
4.1 DEFLECTION
Deflection is usually caused by ATC misalignment, and sometimes caused by damaged or poor quality tooling, a damaged
spindle taper, or a damaged drawbar. Before beginning any troubleshooting, observe the direction of the ATC deflection.
´
During a tool change, ATC appears to be pushed down.
l
Check to see if pull studs on the tool holder are correct and tight.
l
Check the adjustment of the Z offset ("Setting Parameter 64").
NOTE:
If the offset is incorrect a tool changer crash has occured and a thorough inspection of the ATC is necessary at
this time.
l
Check the adjustment of the Z offset check parameters 71, 72, and 143 against the values that are in the
documentation sent with the machine.
l
Ensure the tool holders are held firmly in place by the extractor forks.
l
Ensure the balls on the drawbar move freely in the holes in the drawbar when the tool release button is pressed. If they
do not move freely, the a ATC will be pushed down about 1/4" before the tool holder is seated in the taper, resulting in
damage to the roller bolts on the ATC shuttle. Replace the drawbar.
´
Tool holder sticking in the spindle taper causes the ATC to be pulled up as the spindle head
is traveling up; accompanied by a popping noise as the tool holder pops out of the spindle
taper.
NOTE:
This problem may occur after loading a cold tool into a hot spindle (a result of thermal expansion of the tool
holder inside the spindle taper. It may also occur in cuts with heavy vibration. If sticking occurs only during these
circumstances, no service is necessary.
l
Check the condition of the customers tooling, verifying the taper on the tool holder is ground and not turned. Look for
damage to the taper caused by chips in the taper or rough handling. If the tooling is suspected, try to duplicate the
symptoms with different tooling.
l
Check the condition of the spindle taper. Look for damage caused by chips or damaged tooling. Also, look for damage
such as deep gouges in the spindle taper caused by tool crashing. See "Spindle Assembly" section for spindle
cartridge replacement.
l
Duplicate the cutting conditions under which the deflection occurs, but do not execute an automatic tool change. Try
instead to release the tool using the tool release button on the front of the spindle head. If sticking is observed, the
deflection is not caused by improper ATC adjustment, but is a problem in the spindle head on the machine. See the
"Spindle Assembly" section in Mechanical Service for spindle cartridge replacement.
´
During a tool change, ATC appears to be pulled up; no popping noises.
l
Check the adjustment of the Z offset ("Setting Parameter 64" section). NOTE: If the offset is incorrect, a tool
changer crash has occurred, and a thorough inspection of the ATC is necessary at this time.
Summary of Contents for VF-SERIES
Page 180: ...1 15 96 96 8100 177 TABLEOFCONTENTS TECHNICAL REFERENCE SERVICE M A N U A L VF SERIES ...
Page 235: ...96 8100 1 15 96 232 VF SERIES S E R V I C E M A N U A L ASSEMBLY DRAWINGS VF 1 COLUMN ...
Page 237: ...96 8100 1 15 96 234 VF SERIES S E R V I C E M A N U A L ASSEMBLY DRAWINGS VF 1 LEADSCREW ...
Page 239: ...96 8100 1 15 96 236 VF SERIES S E R V I C E M A N U A L ASSEMBLY DRAWINGS VF 3 COLUMN ...
Page 241: ...96 8100 1 15 96 238 VF SERIES S E R V I C E M A N U A L ASSEMBLY DRAWINGS VF 3 LEADSCREW ...
Page 245: ...96 8100 1 15 96 242 VF SERIES S E R V I C E M A N U A L ASSEMBLY DRAWINGS 3 4 2 1 ...