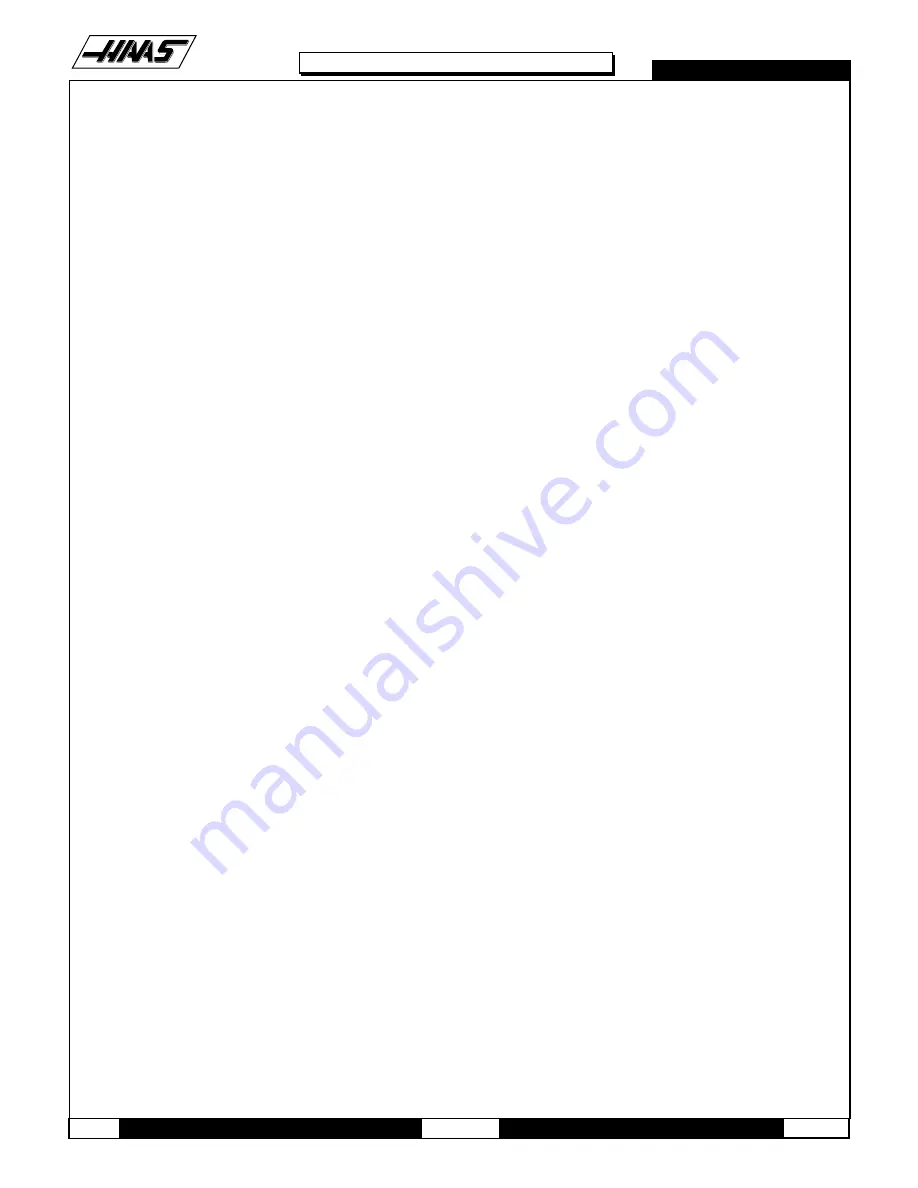
96-8100
1-15-96
HAAS
AUTOMATION, INC.
TROUBLESHOOTING
S E R V I C E M A N U A L
VF-S
ERIES
8
2.5 SPINDLE DRIVE
Low line voltage may prevent the spindle from accelerating properly. If the spindle takes a long time to accelerate, slows
down or stays at a speed below the commanded speed with the load meter at full load, the spindle drive and motor are
overloaded. High load, low voltage, or too fast accel/decel can cause this problem.
If the spindle is accelerated and decelerated frequently, the regenerative load resistor inside the control may heat up. If this
resistor heats beyond 100
o
C, a thermostat will generate an overheat alarm.
If the regen load resistors are not connected or open, this could then result in an overvoltage alarm. The overvoltage occurs
because the regenerative energy being absorbed from the motor while decelerating is turned into voltage by the spindle
drive. If this problem occurs, the possible fixes are to slow the decel rate or reduce the frequency of spindle speed changes.
2.6 ORIENTATION
´
Spindle loses correct orientation.
l
Check alarm history, looking for spindle overload and axis overcurrent alarms. These alarms the machine is not being
properly operated.
l
Check the orientation ring for tightness. Ensure the shaft on which the ring mounts is free of grease.
l
Check the orientation ring for cracks near the bolt holes or near the balancing holes.
Ø
If there are cracks, replace the ring.
l
Check the shot pin on the gearbox for binding, damage, and proper operation. Replace it if it is damaged.
l
Check the switch on the shot pin against the Diagnostic display. Replace the switch if it is found to be faulty.
2.7 TOOLS STICKING IN TAPER
´
Tool sticking in the taper causes ATC to be pulled up; accompanied by a popping noise as the
tool holder pops out of the spindle taper.
NOTE:
This problem may occur after loading a cold tool into a hot spindle (a result of thermal expansion of the tool
holder inside the spindle taper). It may also occur due to heavy milling, milling with long tooling, or cuts with heavy
vibration. If sticking only occurs during these situations, no service is necessary.
l
Check the condition of the tooling, verifying the taper on the tooling is ground and not turned. Look for damage to the
taper caused by chips in the taper or rough handling. If the tooling is suspected, try to duplicate the
symptoms with different tooling.
l
Check the condition of the spindle taper. Look for damage caused by chips or damaged tooling. Also, look for
damage such as deep gouges in the spindle taper caused by tool crashing.
l
Duplicate the cutting conditions under which the deflection occurs, but do not execute an automatic tool change. Try
instead to release the tool using the tool release button on the front of the spindle head. If sticking is observed, the
deflection is not caused by improper ATC adjustment, but is a problem in the spindle head on the machine.
l
Ensure the spindle is not running too hot.
Summary of Contents for VF-SERIES
Page 180: ...1 15 96 96 8100 177 TABLEOFCONTENTS TECHNICAL REFERENCE SERVICE M A N U A L VF SERIES ...
Page 235: ...96 8100 1 15 96 232 VF SERIES S E R V I C E M A N U A L ASSEMBLY DRAWINGS VF 1 COLUMN ...
Page 237: ...96 8100 1 15 96 234 VF SERIES S E R V I C E M A N U A L ASSEMBLY DRAWINGS VF 1 LEADSCREW ...
Page 239: ...96 8100 1 15 96 236 VF SERIES S E R V I C E M A N U A L ASSEMBLY DRAWINGS VF 3 COLUMN ...
Page 241: ...96 8100 1 15 96 238 VF SERIES S E R V I C E M A N U A L ASSEMBLY DRAWINGS VF 3 LEADSCREW ...
Page 245: ...96 8100 1 15 96 242 VF SERIES S E R V I C E M A N U A L ASSEMBLY DRAWINGS 3 4 2 1 ...