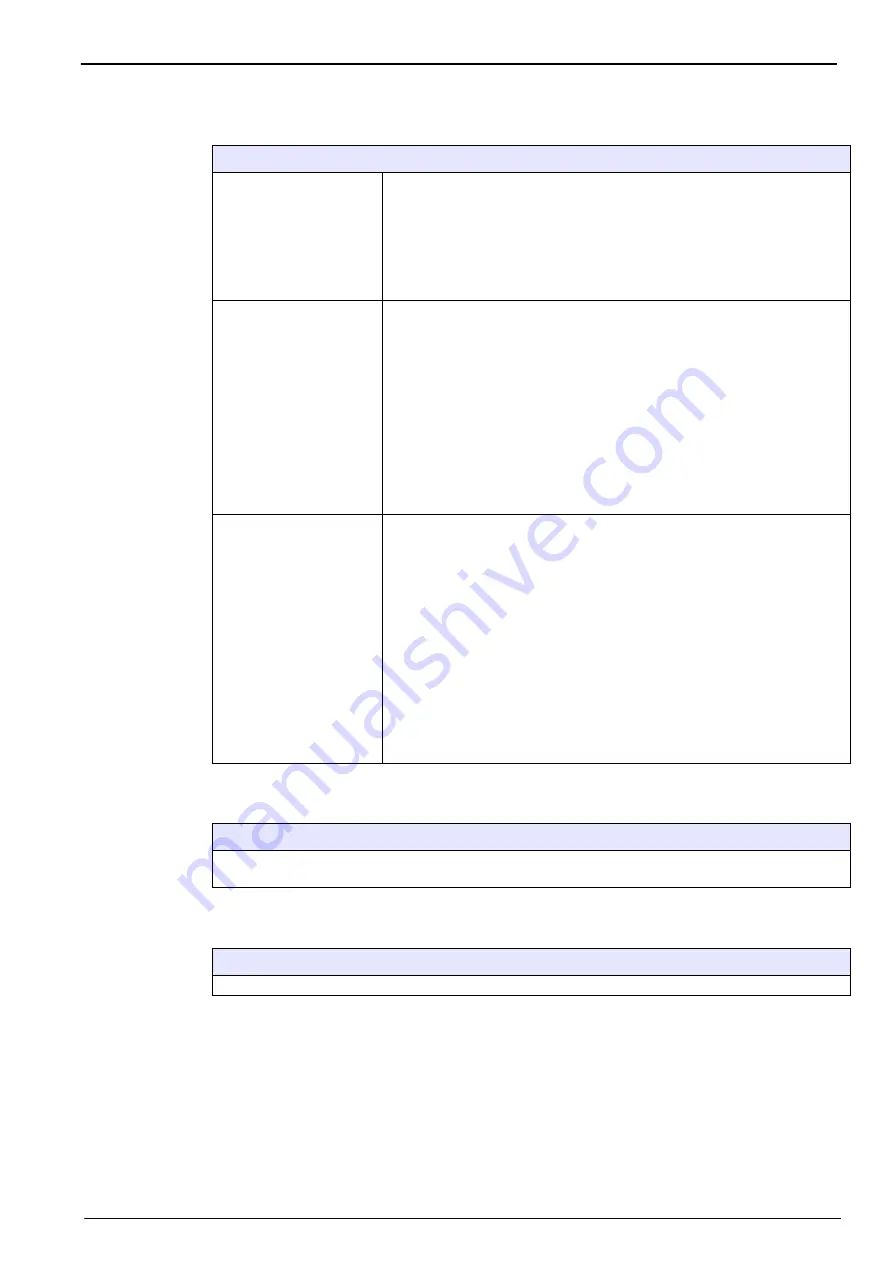
91
Services Menu
13.1 Sensor diagnostics
13.2 Language selection
13.3 Clock
Sensor diagnostics
Calibration timer
The instrument can automatically remind the user when the next sensor
calibration is due.
•
Select enable and enter a delay in days.
•
The display shows the current instrument date and time, next calibration
due date and time, and the remaining days.
The next calibration date is updated when the sensor is calibrated. The
event “Cal. required” is generated when the delay has elapsed.
Service timer
The instrument can automatically remind the user when the next sensor
service is due.
•
Select enable and enter a delay in days. This should be validated by a
level 3 user.
The display shows the current instrument date and time, the next sensor
service due date and time, and the remaining days.
The next service date is updated when the button
Service done
is pressed
after a service. The event “Service required” is generated when the delay
has elapsed.
The sensor attached to your instrument will require periodic servicing and
maintenance. For more information on this, please refer to the manual
delivered with the sensor.
Sensor
Select either
General
or
Zero diagnostic
from the menu.
General
will display values for the measurements in the sample, while
Zero
is used to display values when the gas concentration is at zero (e.g. during
a zero calibration using pure nitrogen as the calibration medium).
The screen layouts are identical for both diagnostic options, and show
useful information for troubleshooting purposes.
The first screen displays measurement information, with a status (OK or
NOK) alongside. A status of NOK indicates the value is outside of the
acceptable minimum or maximum value. To view the acceptable range limits
press the
Show criteria
button.
The criteria screen displays the acceptable range limits (minimum and
maximum values) for more in-depth troubleshooting.
Note:
If
Zero diagnostic
is selected, a warning message appears. Ensure
the sensor has been calibrated in pure N
2
before selecting this option.
Language selection
Check the language as required and restart the instrument to apply the change. The instrument will
restart in the language selected.
Clock
Type in each appropriate box the actual time and date, and select the display format for them.
Summary of Contents for ORBISPHERE K1200
Page 5: ...4 Table of Contents...
Page 13: ...12 General Information...
Page 39: ...38 Installation...
Page 45: ...44 User Interface...
Page 46: ...45 Section 5 View Menu Figure 34 View menu...
Page 49: ...48 View Menu...
Page 59: ...58 Calibration Menu...
Page 60: ...59 Section 8 Inputs Outputs Menu Figure 40 Inputs Outputs menu...
Page 62: ...61 Inputs Outputs Menu 8 4 Analog outputs Figure 41 Analog outputs menu...
Page 69: ...68 Inputs Outputs Menu...
Page 86: ...85 Section 11 Products Menu Figure 44 Products menu...
Page 89: ...88 Global Configuration Menu...
Page 90: ...89 Section 13 Services Menu Figure 46 Services menu Part 1...
Page 91: ...90 Services Menu Figure 47 Services menu Part 2...