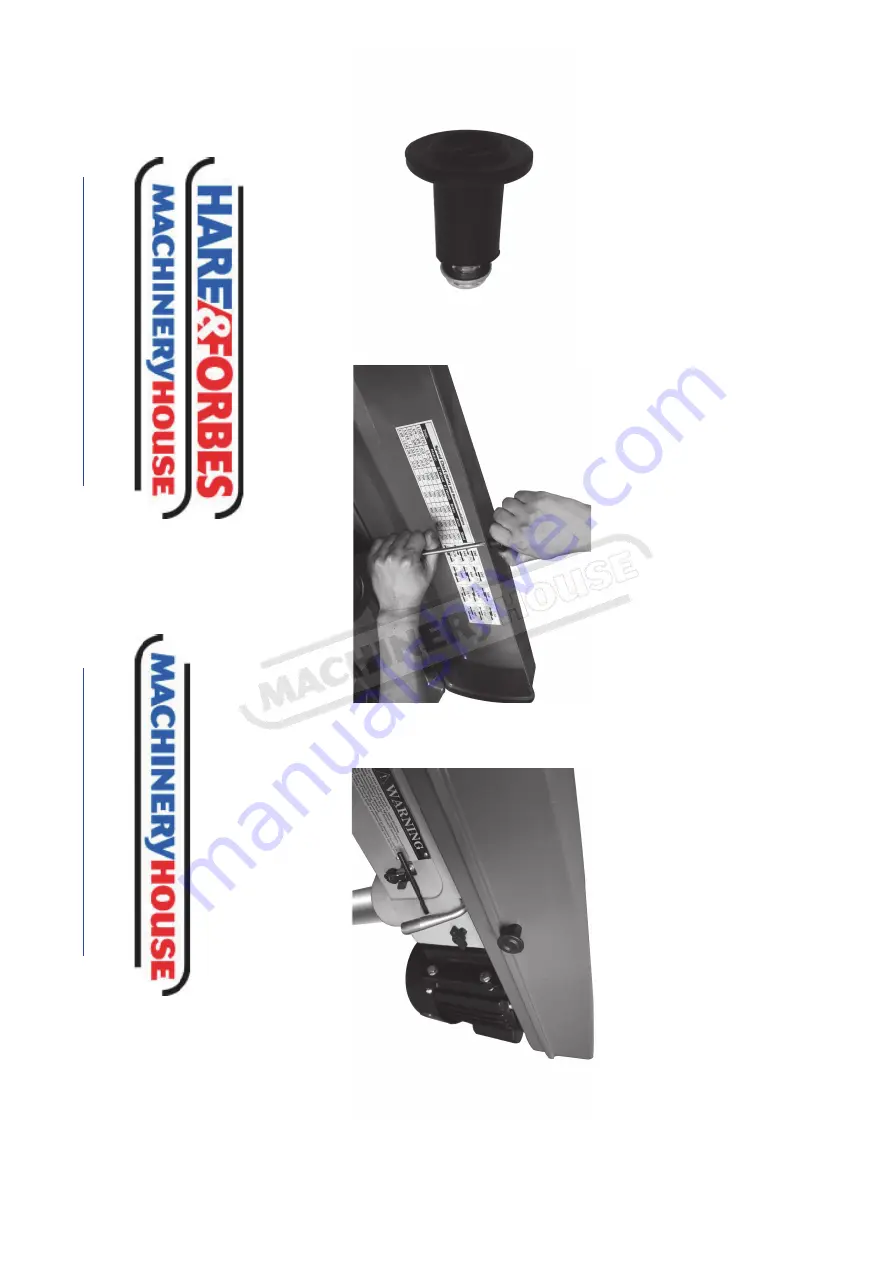
ADDITIONAL
SHEET
FOR PULLEY
COVER LIFT
KNOB
1.
Please take out the pulley cover
lift knob fr
om the bag as Fig 1.
V 2015-11-14
2.
Please use a Philips scr
ew driver
to tighten the scr
ew as Fig 2 befor
e operate the machine.
Fig 1
Fig 2
Fig 3
www
.machineryhouse.com.au
www
.machineryhouse.co.nz
Page 37
Instructions Manual for PD-440 (D598)
19/11/2015