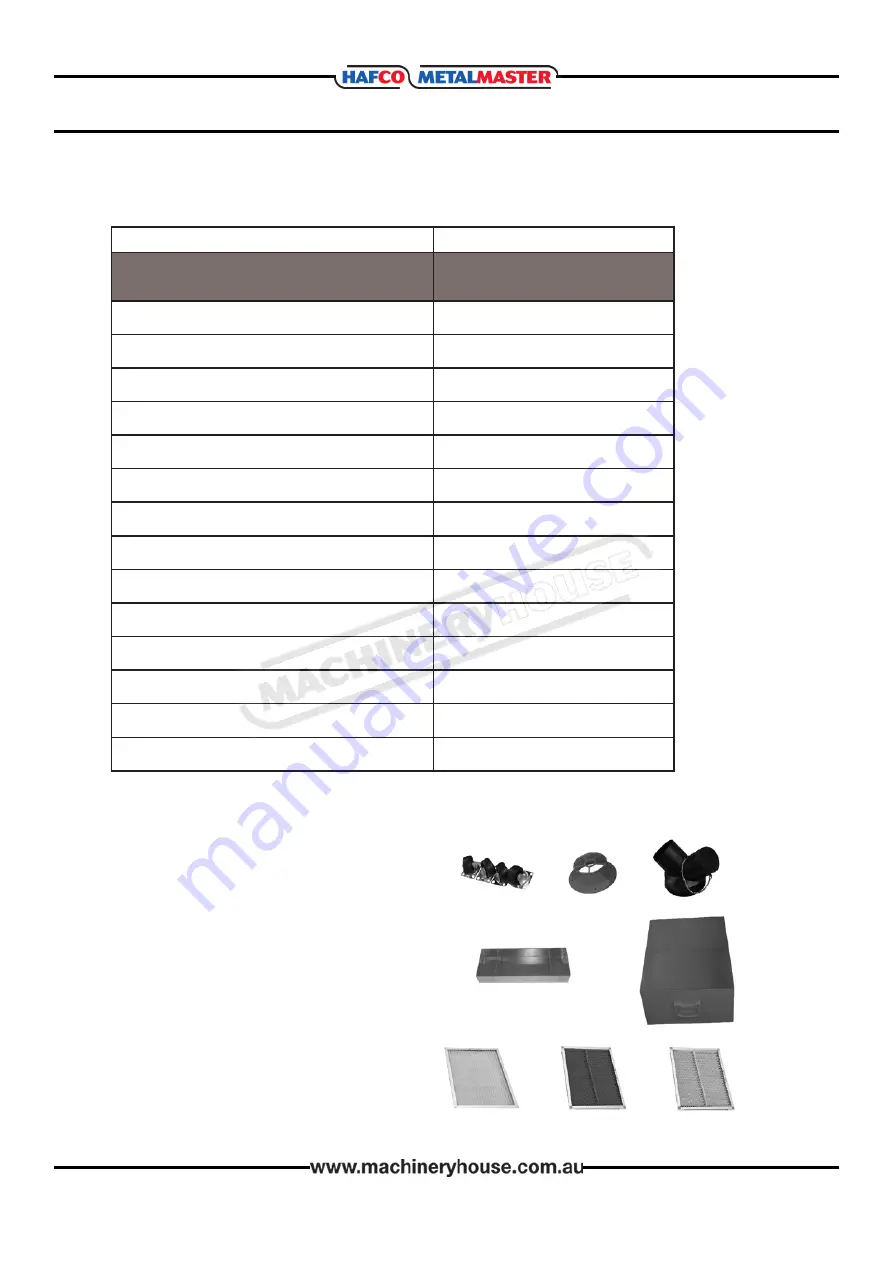
4
OPERATION MANUAL
1.1 SPECIFICATION
Order Code
W321
MODEL
DCM-202
Dust Collector Type (Application)
Metal
Airflow (cfm)
650
Main Inlet Size (inch)
6
Adapter Inlets / Diameter (No/inch)
2/4
First-Stage Filter Type
Stainless Steel Mesh
Second-Stage Filter Type
Active Carbon
Second-Stage Filter Rating (Micron)
5
Third Stage Filter Type
Pleated Micro Filter
Third Stage Filter Rating (Micron)
1
Motor Power (hp)
1.5
Voltage (V/Hz)
240/50
Amps (A)
10
Dimensions (L x W x H) (mm)
725 x 508 x 1092
Weight (kg)
90.5
1.2 ACCESSORIES INCLUDED
4 x Casters
1 x Dust Port
1 x Y-Inlet
1 x Collection Drawer
1 x Pleated Micro Filter
1 x Active Carbon Filter
1 x Stainless-Steel Mesh Filter
1 x Dust Tray