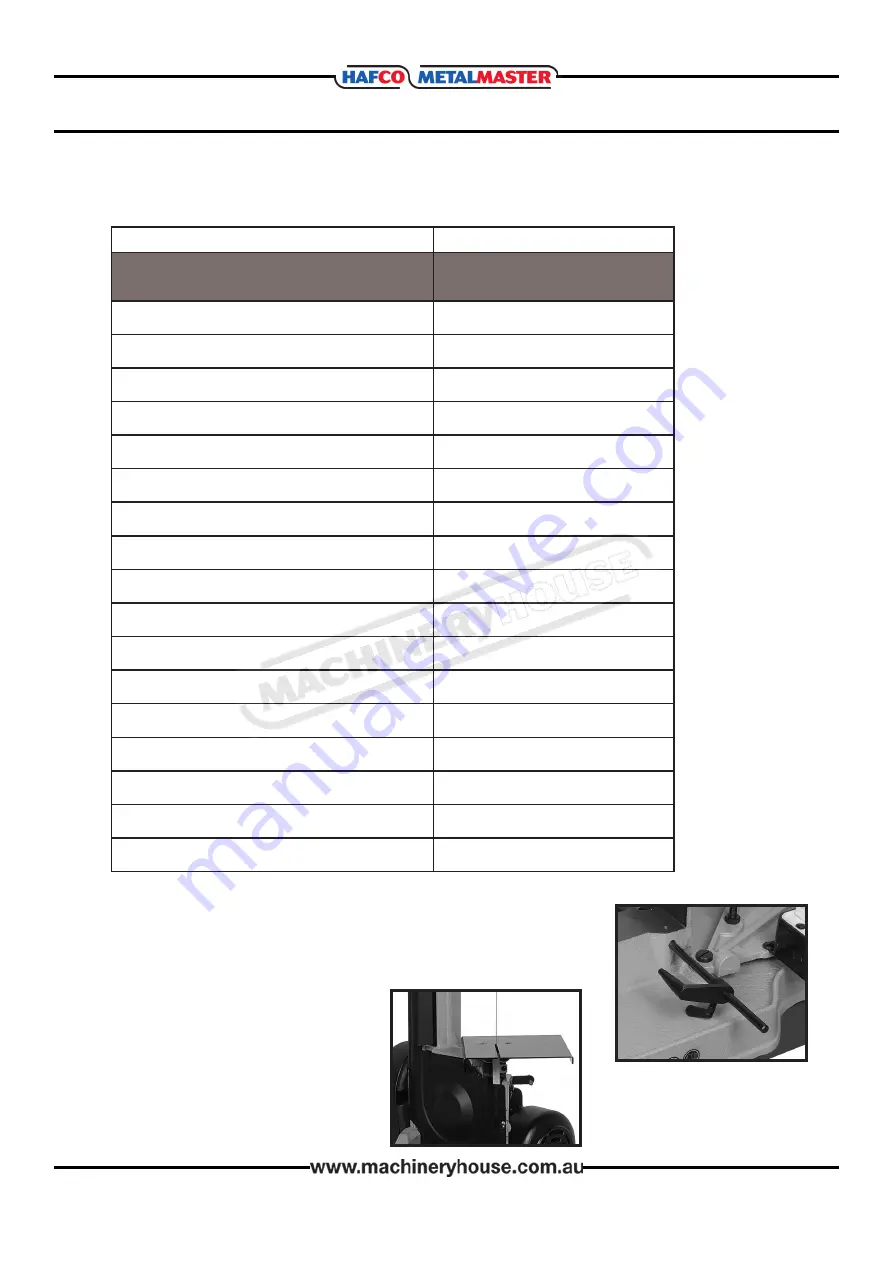
4
OPERATION MANUAL
1.1 SPECIFICATION
Order Code
B003
MODEL
BS-5S
Operation Type
Swivel Head
Capacity Round @ 90º (mm)
125
Round @ 45º (mm)
80
Square @ 90º (mm)
125
Square @ 45º (mm)
75
Rectangle @ 90º (W x H) (mm)
200 x 125
Rectangle @ 45º (W x H) (mm)
125 x 72
Table Working Height (mm)
680
Cutting Head Beam Type
Manual
Cutting Head Down Feed Control
Fixed Spring Type
Vice Clamping Fixture
Manual
Blade Steps / Speeds (m/mm)
10 - 29 - 50
Blade Size (L x W x T) (mm)
1727 x 12.7 x 0.65
Motor Power (kW / hp))
0.375 / 0.5
Voltage / Amperage (V / amp)
240 / 10
Dimensions ( L x W x H) (mm)
995 x 420 x 1162
Weight (kg)
65
1.2 ACCESSORIES INCLUDED
1 x Adjustable length stop for repetition cutting
1 x Vertical cutting table included
1 x Band Saw Blade