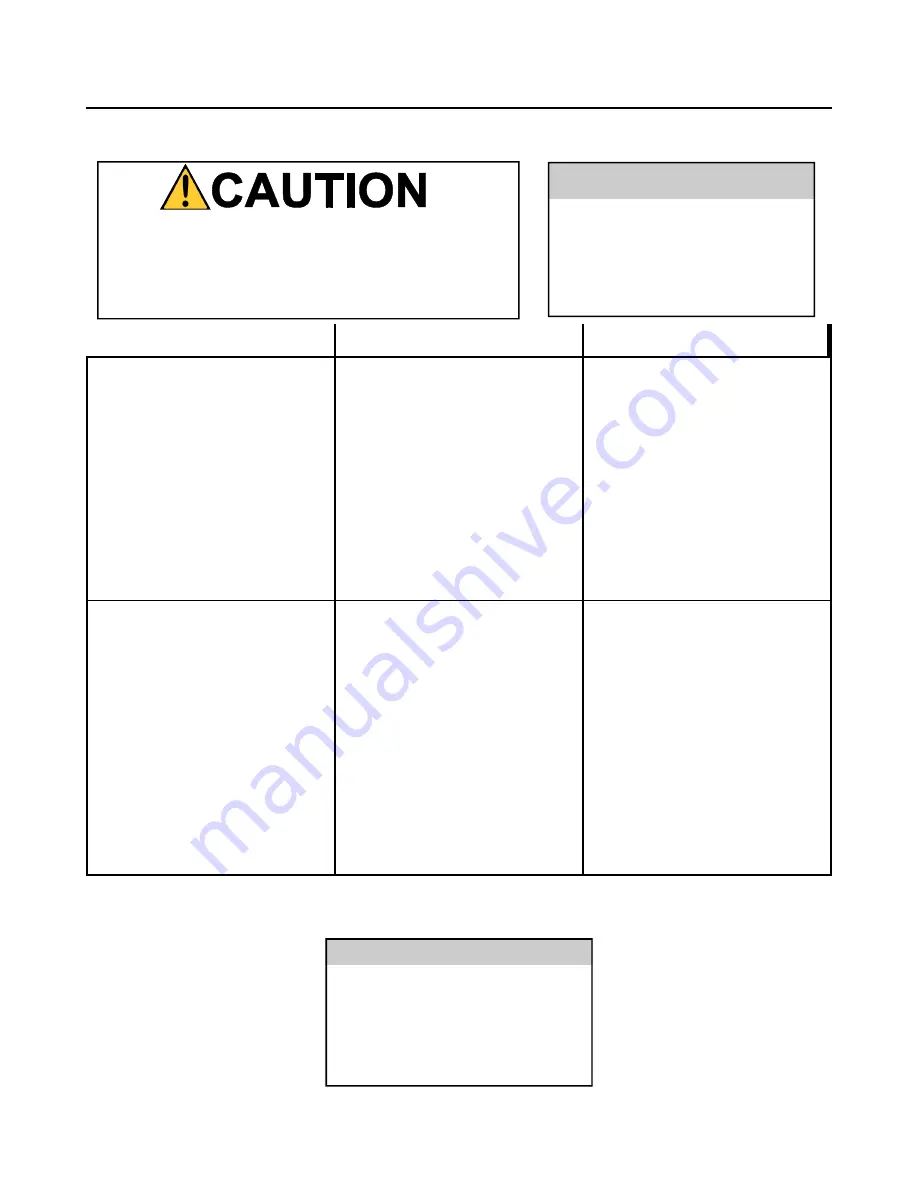
8.8
E. ELECTRICAL
Batteries contain sulfuric acid. Avoid contact with
skin, eyes, or clothing. Do not inhale fumes or ingest
liquid. Batteries contain gases which can explode.
Keep sparks and flame away while servicing.
NOTE:
Disconnect battery when servicing
any part of electrical system to
prevent system damage.
VIII.
TROUBLE SHOOTING
PROBLEM
POSSIBLE CAUSE
SUGGESTED REMEDY
Entire electrical system is dead
•
Dead battery
•
Poor battery connection
•
Low charging rate
•
No charging rate
•
Battery master switch is in OFF
position
•
Replace battery
•
Clean and tighten battery con-
nections
•
Tighten alternator belt
•
Replace alternator
•
Turn battery master switch to
ON position
Light system does not function
•
Poor ground
•
Burned out bulb
•
Separation or short in wire
•
Blown fuse
•
Faulty switch
•
Ignition switch is off
•
Clean and tighten ground
•
Replace bulb
•
Check continuity and replace
wire
•
Replace fuse
•
Replace switch
•
Turn ignition switch to ON posi-
tion
NOTE:
Refer to the Raven installation and
operation manual for trouble shoot-
ing guide on Raven console and
system