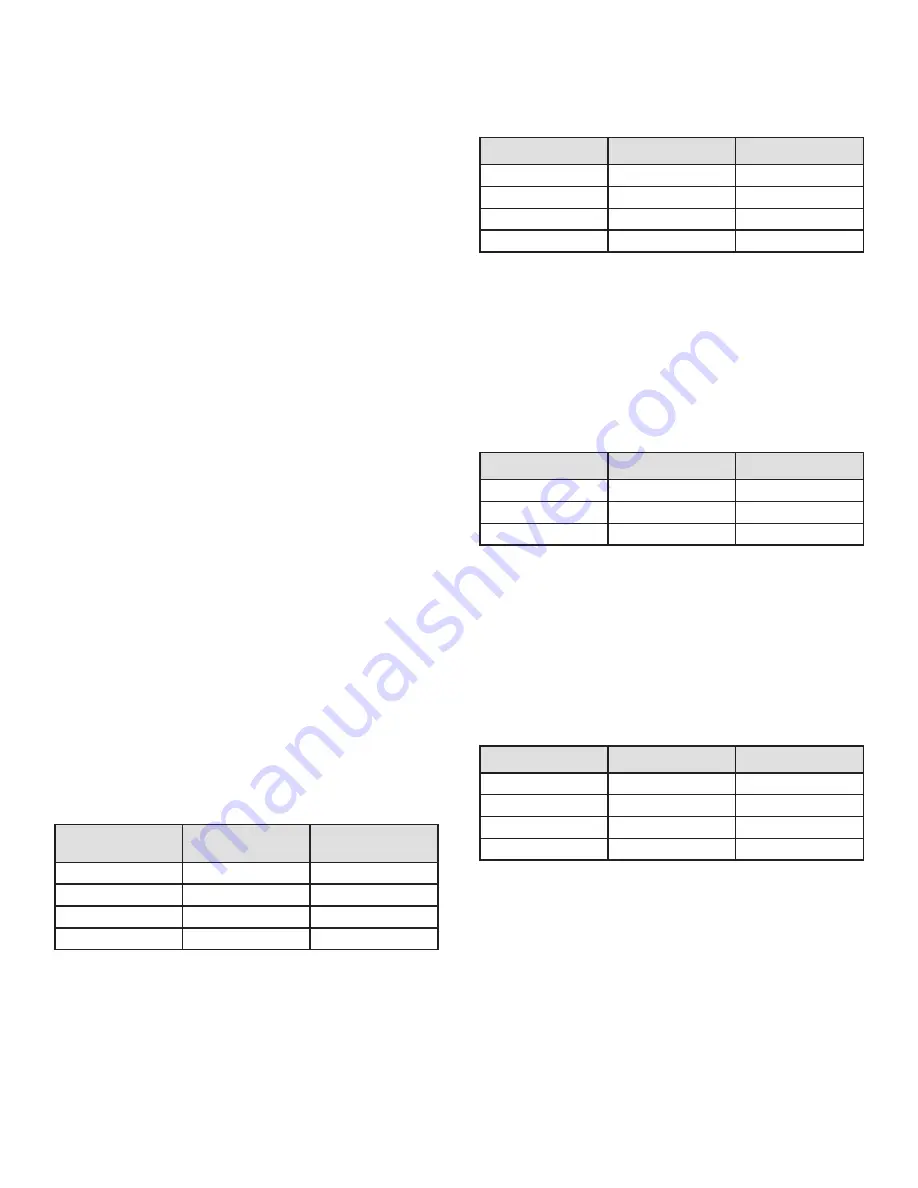
Page 16
31-5000734 Rev. 0
DIP Switch Settings
Heating Operation DIP Switch Settings
Switch 1 -- Thermostat Selection --
This unit may be
used with either a single-stage or two-stage thermostat.
The thermostat selection is made using a DIP switch which
must be properly positioned for the particular application.
The DIP switch is factory-positioned for use with a twostage
thermostat. If a single-stage thermostat is to be used, the
DIP switch must be repositioned.
1. Select “OFF” for two-stage heating operation controlled
by a two-stage heating thermostat (factory setting);
2. Select “ON” for two-stage heating operation controlled
by a single-stage heating thermostat. This setting
provides a timed delay before second-stage heat is
initiated.
Switch 2 -- Second Stage Delay (Used with Single-Stage
Thermostat Only) --
This switch is used to determine the
second stage on delay when a single-stage thermostat is
being used. The switch is factory-set in the OFF position,
which provides a 7-minute delay before secondstage heat
is initiated. If the switch is toggled to the ON position, it
will provide a 12-minute delay before secondstage heat is
initiated. This switch is only activated when the thermostat
selector jumper is positioned for SINGLEstage thermostat
use.
Switches 3 and 4 -- Blower-Off Delay --
The blower-on
delay of 30 seconds is not adjustable. The blower-off delay
(time that the blower operates after the heating demand
has been satisfied) can be adjusted by moving switches
3 and 4 on the integrated control. The unit is shipped
from the factory with a blower-off delay of 90 seconds.
The blower off delay affects comfort and is adjustable to
atisfy individual applicationsAdjust the blower off delay to
achieve a supply air temperature between 90° and 110°F at
the exact moment that the blower is de-energized. Longer
off delay settings provide lower supply air temperatures;
shorter settings provide higher supply air temperatures.
Table 5 provides the blower off timings that will result from
different switch settings.
Blower Off Delay
Seconds
Switch 3
Switch 4
60
On
Off
90 (factory)
Off
Off
120
Off
On
180
On
On
Table 5.
Blower Off Delay Switch Settings
Indoor Blower Operation DIP Switch Settings
Switches 5 and 6 -- Cooling Mode Blower Speed --
The unit is shipped from the factory with the dip switches
positioned for high speed (4) indoor blower motor operation
during the cooling mode. Table 6 provides the cooling mode
blower speeds that will result from different switch settings.
Switches 5 and 6 set the blower cfm for secondstage cool.
The integrated control automatically ramps down to 70% of
the second-stage cfm for first-stage cfm. Refer to tables for
corresponding cfm values.
Speed
Switch 5
Switch 6
Low
On
On
Medium Low
Off
On
Medium High
On
Off
High (factory)
Off
Off
Table 6. Cooling Mode Blower Speeds
Switches 7 and 8 -- Cooling Blower Speed Adjustment
-- The unit is shipped from the factory with the dip switches
positioned for NORMAL (no) adjustment. The dip switches
may be positioned to adjust the blower speed by +10% or
-10% to better suit the application. Table 7 below provides
blower speed adjustments that will result from different
switch settings. Refer to tables for corresponding cfm
values.
Adjustment
Switch 7
Switch 8
+10% (approx)
On
Off
Factory Default
Off
Off
-10% (approx)
Off
Off
Table 7. Cooling Blower Speed Adjustment
Switches 9 and 10 -- Cooling Mode Blower Speed
Ramping --
Blower speed ramping may be used to
enhance dehumidification performance. The switches
are factory set at option A which has the greatest effect
on dehumidification performance. Table 8 provides the
cooling mode blower speed ramping options that will result
from different switch settings. The cooling mode blower
speed ramping options are detailed below.
Ramping
Switch 9
Switch 10
A (Factory)
Off
Off
B
Off
On
C
On
Off
D
On
On
Table 8. Cooling Mode Blower Speed Ramping