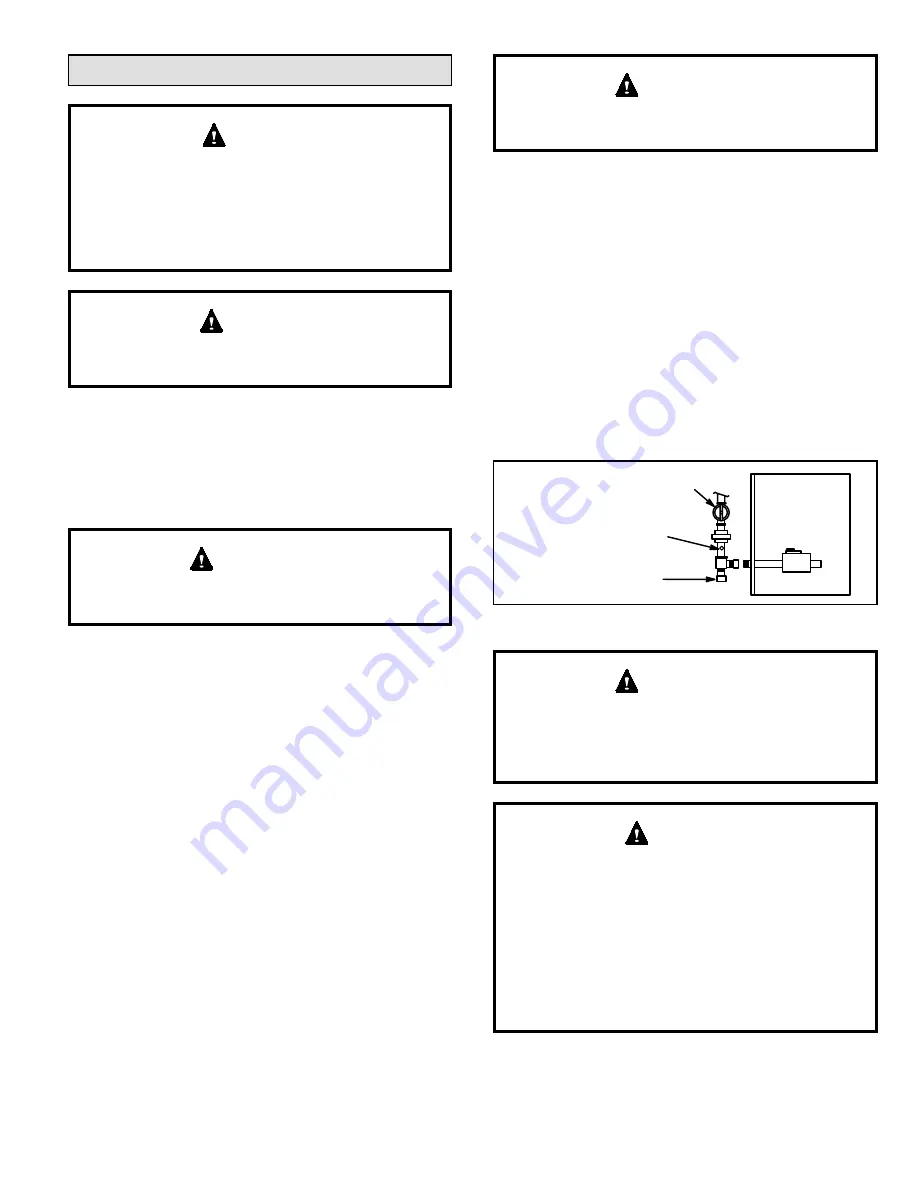
507769-05G / 31-5000656
Page 33 of 55
Issue 2223
Gas Piping
If a flexible gas connector is required or allowed by
the authority that has jurisdiction, black iron pipe shall
be installed at the gas valve and extend outside the
furnace cabinet. The flexible connector can then be
added between the black iron pipe and the gas supply
line.
CAUTION
Do Not
exceed 600 in. lbs. (50 ft. lbs.) torque when
attaching the gas piping to the gas valve.
WARNING
1. Gas piping may be routed into the unit through either
the left or right hand side. Supply piping enters into the
gas valve from the side of the valve as shown in Figure
47. Move bellows grommet to side of the cabinet which
the gas line enters. Ensure opposite gas line entrance
is plugged with supplied plug.
A low inlet pressure switch in LP/propane applications
is recommended.
IMPORTANT
2. When connecting gas supply, factors such as length
of run, number of fittings and furnace rating must be
considered to avoid excessive pressure drop. Table 11
lists recommended pipe sizes for typical applications.
NOTE:
Use two wrenches when connecting gas piping
to avoid transferring torque to the manifold.
3. Gas piping must not run in or through air ducts,
clothes chutes, chimneys or gas vents, dumb waiters
or elevator shafts. Center gas line through piping hole.
Gas line should not touch side of unit. See Figure 47.
4. Piping should be sloped 1/4 inch per 15 feet (6 mm per
5.6 m) upward toward the gas meter from the furnace.
The piping must be supported at proper intervals,
every 8 to 10 feet (2.44 to 3.05 m), using suitable
hangers or straps. Install a drip leg in vertical pipe runs
to serve as a trap for sediment or condensate.
5. A 1/8” N.P.T. plugged tap or pressure post is located
on the gas valve to facilitate test gauge connection.
6. In some localities, codes may require installation of a
manual main shut off valve and union (furnished by
installer) external to the unit. Union must be of the
ground joint type.
Compounds used on threaded joints of gas piping must
be resistant to the actions of liquified petroleum gases.
IMPORTANT
Leak Check
After gas piping is completed, carefully check all field-
installed piping connections for gas leaks. Use a
commercially available leak detecting solution specifically
manufactured for leak detection. Never use an open flame
to test for gas leaks.
The furnace must be isolated from the gas supply
system by closing the individual manual shut-off valve
during any gas supply system at pressures greater than
or equal to 1/2 psig (3.48 kPa, 14 inches w.c.). This
furnace and its components are designed, manufactured
and independently certified to comply with all applicable
ANSI/CSA standards. A leak check of the furnace and its
components is not required.
Figure 46.
MANUAL MAIN SHUT−OFF
VALVE WILL NOT HOLD
NORMAL TEST PRESSURE
CAP
FURNACE
ISOLATE
GAS VALVE
1/8" N.P.T. PLUGGED TAP
When testing pressure of gas lines, gas valve must be
disconnected and isolated (see Figure 46). Gas Valves
can be damaged if subjected to pressures greater than
1/2 psig (3.48 kPa).
IMPORTANT
FIRE OR EXPLOSION HAZARD
Failure to follow the safety warnings exactly could
result in serious injury, death, or property damage.
Never use an open flame to test for gas leaks. Check
all connections using a commercially available soap
solution made specifically for leak detection. Some
soaps used for leak detection are corrosive to certain
metals. Carefully rinse piping thoroughly after leak test
has been completed.
WARNING