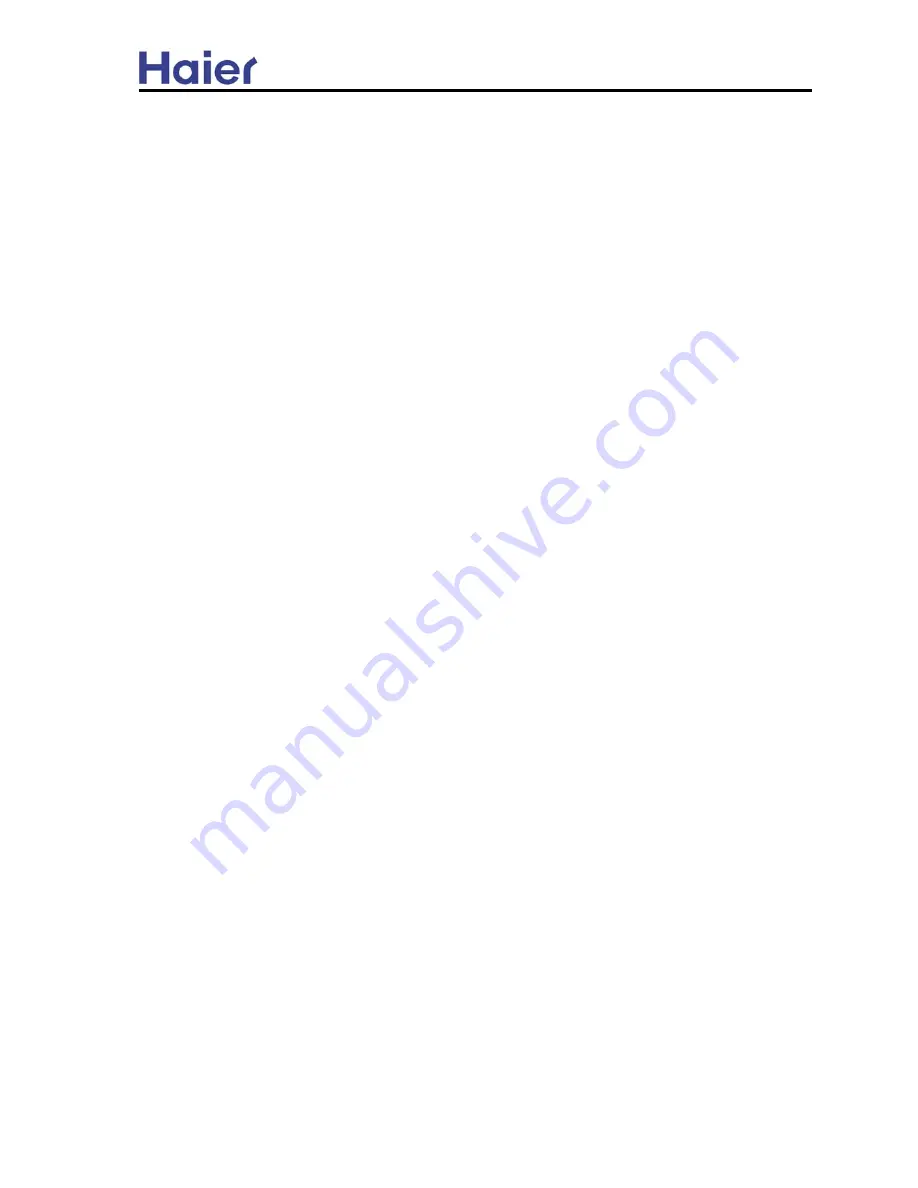
4. Remove the failed compressor.
A. Unsolder the suction and discharge lines at the compressor stubs.
B. Remove the compressor hold down bolts.
C. Place the failed compressor on a smooth surface to remove the mounting grommets and
sleeves for use with the new compressor .
D. Prevent any contamination from entering the refrigerant lines.
5. Conduct an acid test on the oil from the failed compressor .
A. Secure a generous sample of oil from the failed compressor.
B. Follow the oil test kit instructions to determine the degree of compressor burn out.
.
●
As a general rule, oil with a test number less than 0.05 indicates a mild burn out.
●
As a guide ,burn out classifications are as follows:
Note: Dispose of any contaminated refrigerant oil in accordance with all environmental regulations
6.
discharge lines to determine the extent of contamination.
together.
Warnings:
1.
2.
3.
●
Some oil test kits indicate severity by color change .
oil clear, no color, the compressor may have had a mechinial failure and not a burn-out.
and procedures.
oil clear, slight color, the compressor may have had a mild burn-out .
●
Oil with a test number greater than 0.05 indicates a severe burn-out .
oil very dirty, strong odor test >0.05, the compressor may have had severe burn-out.
Use the following procedures with units suspected of having mild to severe burn outs.
A. After compressor removal, insert a clean, lint free swab into the system‘s suction and
D. Place the new compressor in the unit and install the mounting bolts.
C. Confirm that the new compressor has no shipping damage. The line connections must come
electrical characteristics as the original.
sealed from the factory. Verify that the replacement compressor is the same model number and
F. If any burn detected replace the liquid line filter drier with an oversized core filter drier, if the
burn was severe, and a suction line filter drier.
E. Remove the caps from the compressor stubs, clean the lines and stubs, and braze joints
TACK APPROPRIATE STEPS TO KEEP CONTAMINATIONS OUT OF THE LINES, WHILE
THESE LINE ARE OPEN TO ATMOSPHERE.
B. If contamination is noted for a considerable depth, consider replacing the lines with new tubing.
USE A OFMINIMUM 5% SILVER FOR COPPER TO COPPER CONNECTIONS.
USE A OF MINIMUM 35% SILVER FOR COPPER TO STEEL CONNECTIONS.
operation. Replace any if necessary.
J.
WHEN BRAZING, PURGE DRY NITROGEN THROUGH THE LINES TO PREVENT THE
FORMATION OF OXIDES.
G. Inspect all other components such as check valve and electrical components for proper
H. After all connections are made, open the service valves and pressurize to 150 psi with dry nitrogen,
I. After leak testing ,recover any test refrigerant.
Leak test with liquid detergent. If a leak is found, repair it after removing the nitrogen ,and recheck.
Keep with (A) subpoints.
Use the largest connections and hoses possible to expedite the process.
charging procedures.
Evacuate through both high and low side connections to the system.
Break each vacuum with dry nitrogen to 3.0 psi.
K. Charge with clean, new or reclaimed R-22 refrigerant. Charge in accordance with proper
L. Re-check the system 24 hours of run time to verify the unit is free of acid.
Evacuate to a level of 1500 microns twice and 500 microns the last time.
31
Central Air Conditi
oning
Model: Heat Pump,
HR13-D2