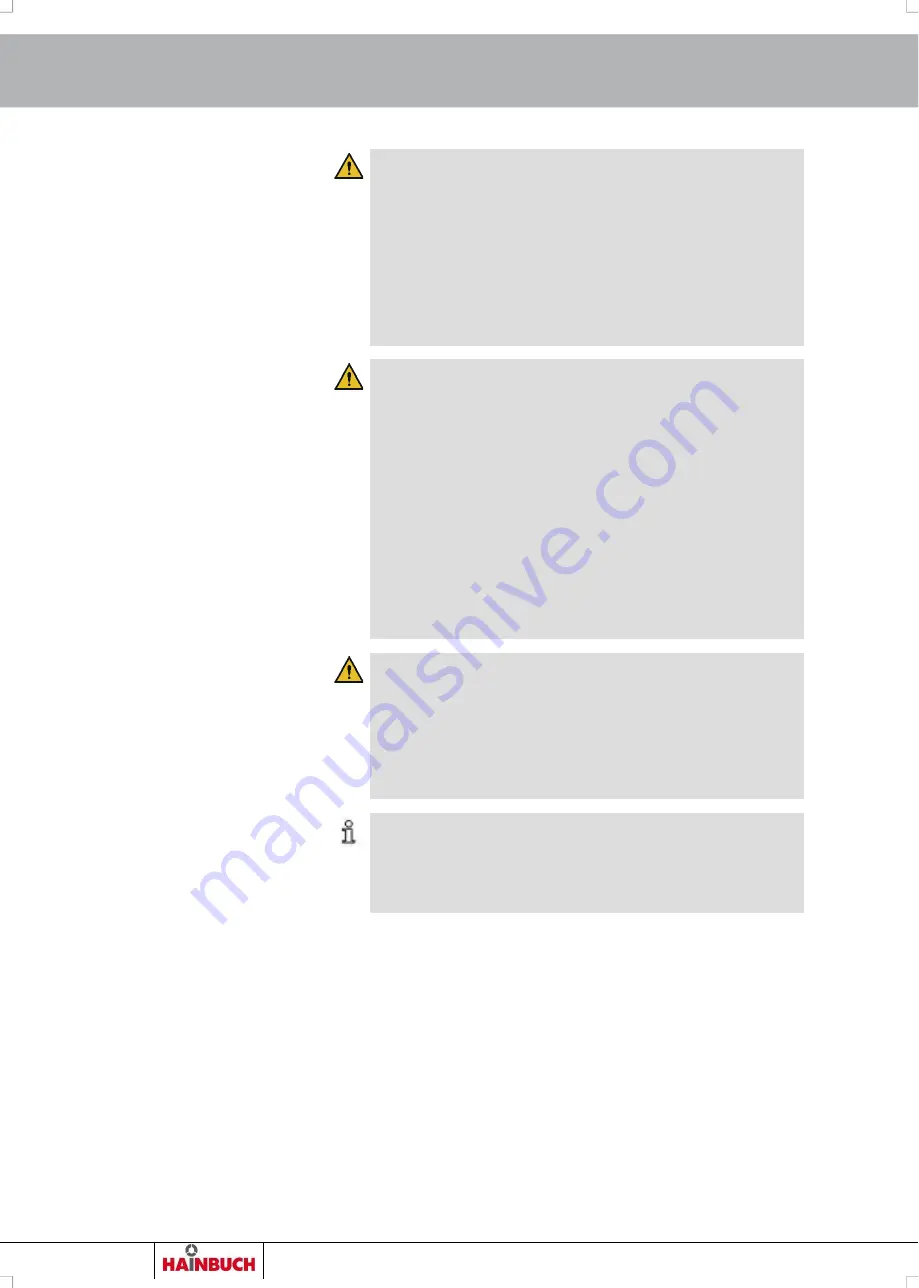
ms dock
Removal
54
Order h49 7144.907-333
WARNING
Serious crushing injuries caused by improper ma-
chine movement during installation or removal!
Machine movements are only permitted in set-up
mode during installation and removal.
Never reach into a gap.
Pay attention to the gap dimensions of moving
parts.
WARNING
Serious head injuries caused by bending into the
working area of the machine!
Only ever bend into the working area of the ma-
chine if there are no cutting tools or sharp objects
in it, or if these are covered.
Never move body parts under parts in the working
area of the machine with the potential to drop
down.
Depending on weight, use an appropriate mount-
ing aid for installation or installing on a vertically
suspended machine spindle.
WARNING
High level of physical strain due to the weight of
the product or of its components if not trans-
ported properly!
From a weight of 10 kg, use appropriate transport
equipment, lifting gear and lifting tackle.
INFORMATION
If necessary, use any forcing / extraction threads in
the components of the product, changing parts or
clamping elements.
10.2 Preparing the machine for removal
1. Set the machine into set-up mode.
2. Remove cutting tools and/or sharp objects from the
working area of the machine, or cover them.
3. Remove operating and auxiliary materials as well as re-
maining processing materials and dispose of them in an
environmentally responsible manner.
Summary of Contents for ms dock
Page 1: ...Operating instructions incl installation manual ms dock EN...
Page 57: ...ms dock Removal Order hotline 49 7144 907 333 57 6 Remove the product from the machine table...
Page 68: ...ms dock Annex 68 Order hotline 49 7144 907 333...
Page 69: ...ms dock Annex Order hotline 49 7144 907 333 69...
Page 71: ...ms dock Order hotline 49 7144 907 333 71 U Unpacking 29 W Warranty 10...