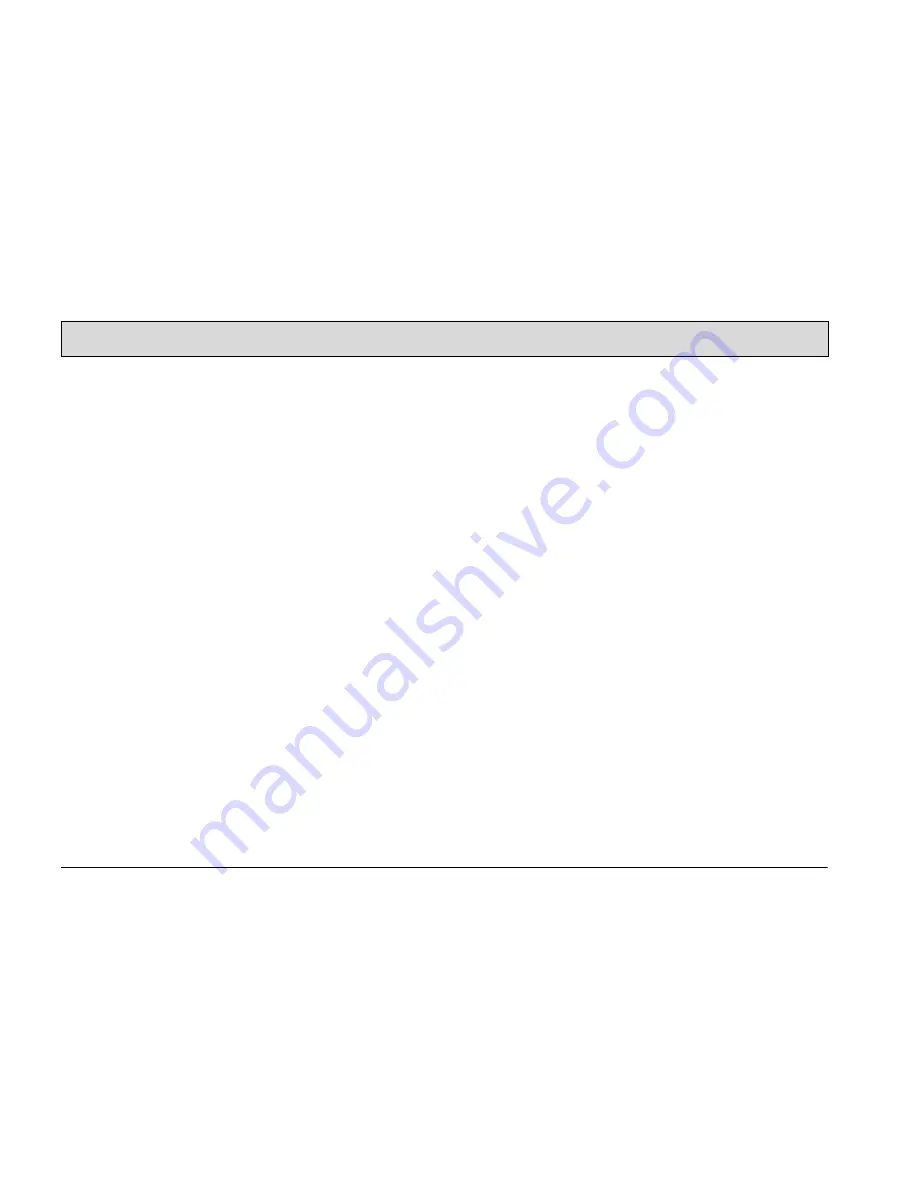
2
Preface
Dear Customer,
We are certain that the excellent quali-
ties of the vehicle will justify the faith
you have shown in us through your pur-
chase.
Please read the Chapter "Safety Infor-
mation" prior to starting the vehicle to
ensure it is operated and used safely.
Your safety, and that of others, basical-
ly lies in your ability to control and oper-
ate the vehicle. Before using the
equipment for the first time, read this
original manual thoroughly, act accord-
ing to the information contained and
keep it in a safe place for future refer-
ence or subsequent owners. The oper-
ating manual contains all the most
important information regarding opera-
tion, maintenance and service.
Throughout this manual, texts which
concern safety are indicated by the cor-
responding danger pictogram. Should
you have any questions in respect of
the vehicle or operating instruction
manual, your authorized Hako dealer is
available to provide help at any time.
We explicitly point out that no legal
claims may be asserted based on the
information contained in this manual.
Ensure only original spare parts are
used should any repairs be necessary.
Only such original spare parts warrant
that the equipment is reliably ready to
use at all times. We reserve the right to
make technical modifications in the in-
terest of further development.
Valid as of: April 2014
Hako GmbH
D-23843 Bad Oldesloe
Hamburger Str. 209-239
Telephone: +49 04531 806-0
Intended use
The Scrubmaster B115 R is a scrubber
dryer for the wet cleaning of hard floors.
This machine is intended for commer-
cial use, for example in hotels, schools,
hospitals, factories, shops, offices and
rental businesses. Any use beyond this
is regarded as improper use. The man-
ufacturer is not considered liable for any
damage resulting from improper use;
the user is solely responsible for all the
potential risks involved. Intended use
also includes maintaining and observ-
ing the operating, maintenance and re-
pair conditions prescribed by the
manufacturer.
The Scrubmaster B115 R may only be
operated, serviced and repaired by per-
sonnel who are familiar with the work
involved and are aware of the risks.
The applicable accident prevention
laws must be observed and any gener-
ally accepted health and safety direc-
tives must be maintained.
Based on the conception, design and
construction of the vehicle introduced
onto the market by us, the vehicle com-
plies with the applicable basic safety
and health requirements stipulated in
the EC Directive (refer to the Declara-
Introduction