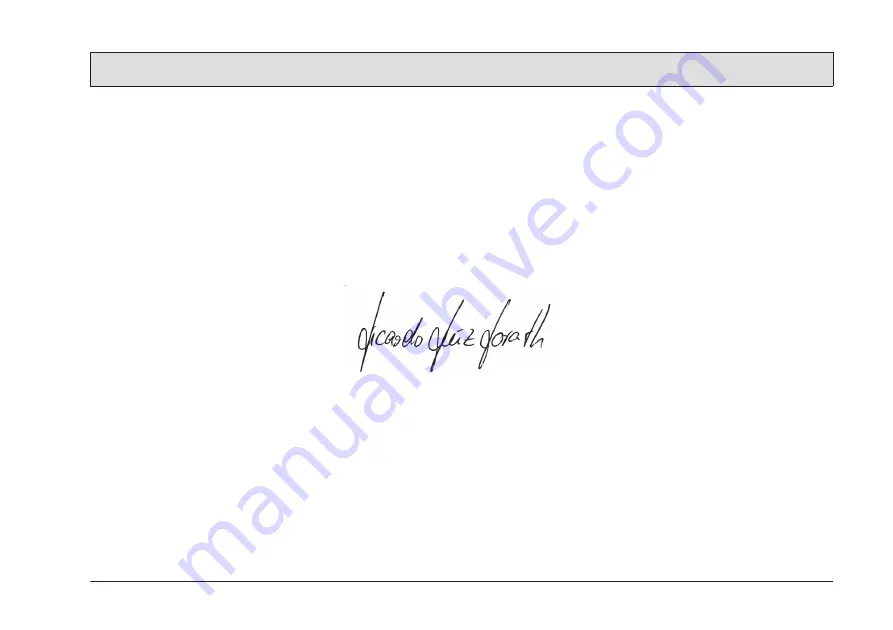
99
+DNR*PE+
+DPEXUJHU6WUDH
'%DG2OGHVORH
declares that the products
6FUXEPDVWHU%5
6FUXEPDVWHU%5&/
7\SH
to which this declaration relates, con-
form to the relevant provisions of the
safety and health requirements stipulat-
ed in EC Directive 2006/42/EU and is in
accordance with 2014/30/EU
and
2014/53/EU
.
Reference was made to the following
standards and/or norms and/or techni-
cal specifications to ensure proper im-
plementation of the safety and health
requirements in the EU Directive:
',1(1
',1(1
',1(1
Bad Oldesloe,
23.01.2018
Name of the authorized person who
compiles technical documents for Ha-
ko:
Ludger Lüttel
EC Declaration of Conformity (in accordance with EC Directive 2006/42/EC)
K
5LFDUGR5XL]3RUDW
5LFDUGR5XL]3RUDWK
U
3URGXFWOLQH0DQDJH
3URGXFWOLQH0DQDJHU
\
&OHDQLQJ7HFKQRORJ
&OHDQLQJ7HFKQRORJ\
Summary of Contents for Scrubmaster B310 R/TB 1020
Page 1: ...QVWUXFWLRQ 0DQXDO 6FUXEPDVWHU 5 7...
Page 98: ...98 Maintenance and Service...