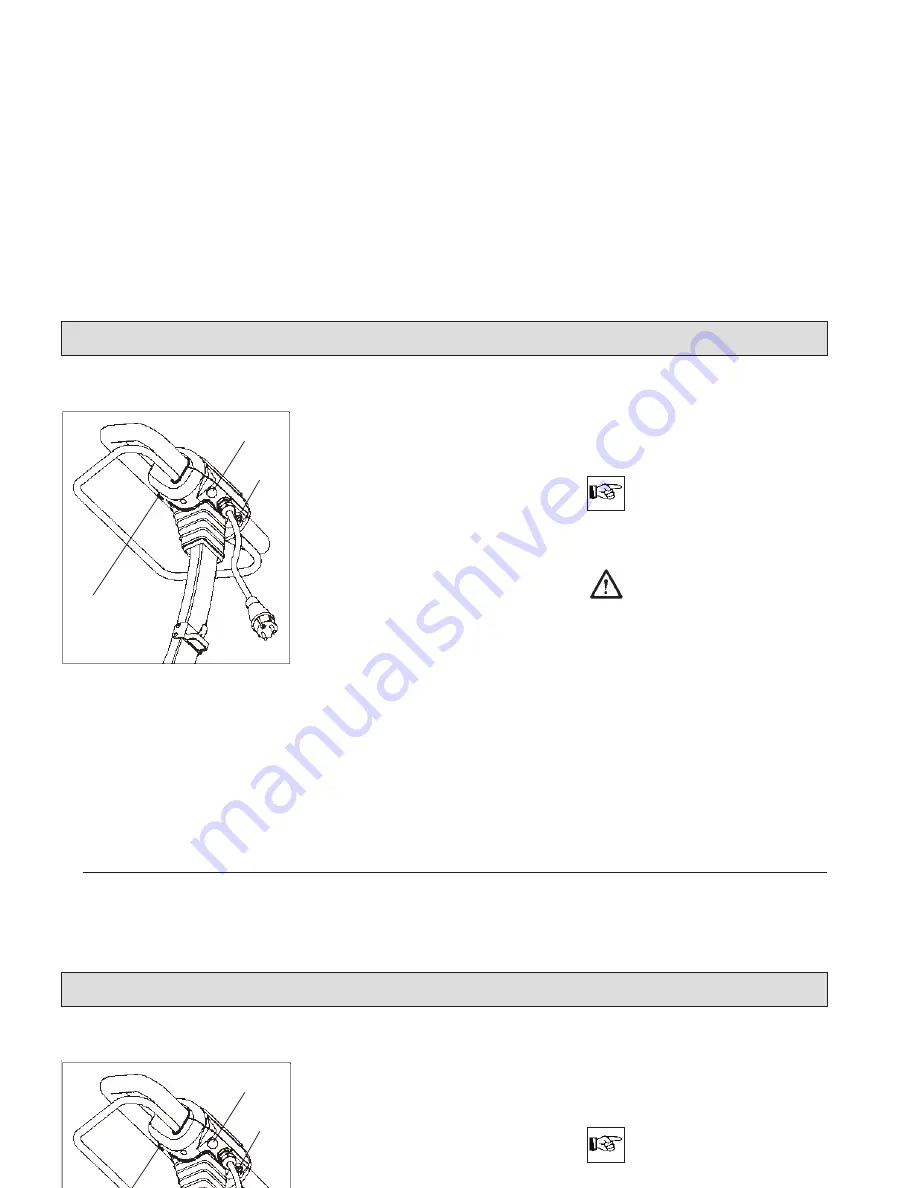
20
Electric System
E Suction motor fuse
F Pump fuse
G Brush motor cut-out
The electric system of the Hakomatic
E
1
0 operates at a mains voltage of
230V/50Hz.
After opening the machines top, the
brush motor and the suction turbine
are well accessible.
A T 6.3 A fuse (E) protects the suction
turbine and has to be replaced by the
same type if blown (T stands for slow-
blow).
The suction turbine is a low-mainte-
nance type; its carbon brushes only
have to be checked after every 200
hours of operation.
The brush motor is protected by a cut-
out (G) which can be manually reset.
In case of tripped cut-out, detect the
cause and remedy before re-starting
the machine.
The pump is protected by a T0.5A
fuse (F). Replace by the same type of
fuse.
Reset the cut-out by pushing down the
transparent dome of the fuse box.
After tripping, wait for approx. 30 sec-
onds before resetting.
In case of repeated fuse
blowing detect the cause.
We recommend having all
work at the electric system
done by qualified personnel
only.
Before staring work at the
electric system, disconnect
the mains plug. After work
at the electric system is fin-
ished, proceed to a safety
test according to VDE stan-
dard 0701,
paragraph 1 and 3.
Operation
F
G
E
20
Electric System
E Suction motor fuse
F Pump fuse
G Brush motor cut-out
The electric system of the Hakomatic
E
1
0 operates at a mains voltage of
230V/50Hz.
After opening the machines top, the
brush motor and the suction turbine
are well accessible.
A T 6.3 A fuse (E) protects the suction
turbine and has to be replaced by the
same type if blown (T stands for slow-
blow).
The suction turbine is a low-mainte-
nance type; its carbon brushes only
have to be checked after every 200
hours of operation.
The brush motor is protected by a cut-
out (G) which can be manually reset.
In case of tripped cut-out, detect the
cause and remedy before re-starting
the machine.
The pump is protected by a T0.5A
fuse (F). Replace by the same type of
fuse.
Reset the cut-out by pushing down the
transparent dome of the fuse box.
After tripping, wait for approx. 30 sec-
onds before resetting.
In case of repeated fuse
blowing detect the cause.
We recommend having all
work at the electric system
done by qualified personnel
only.
Before staring work at the
electric system, disconnect
the mains plug. After work
at the electric system is fin-
ished, proceed to a safety
test according to VDE stan-
dard 0701,
paragraph 1 and 3.
Operation
F
G
E
Summary of Contents for Scrubmaster E10
Page 1: ...Instruction manual Scrubmaster E10 7739 03 ...
Page 26: ...26 Maintenance Maintenance ...
Page 29: ...Notes ...