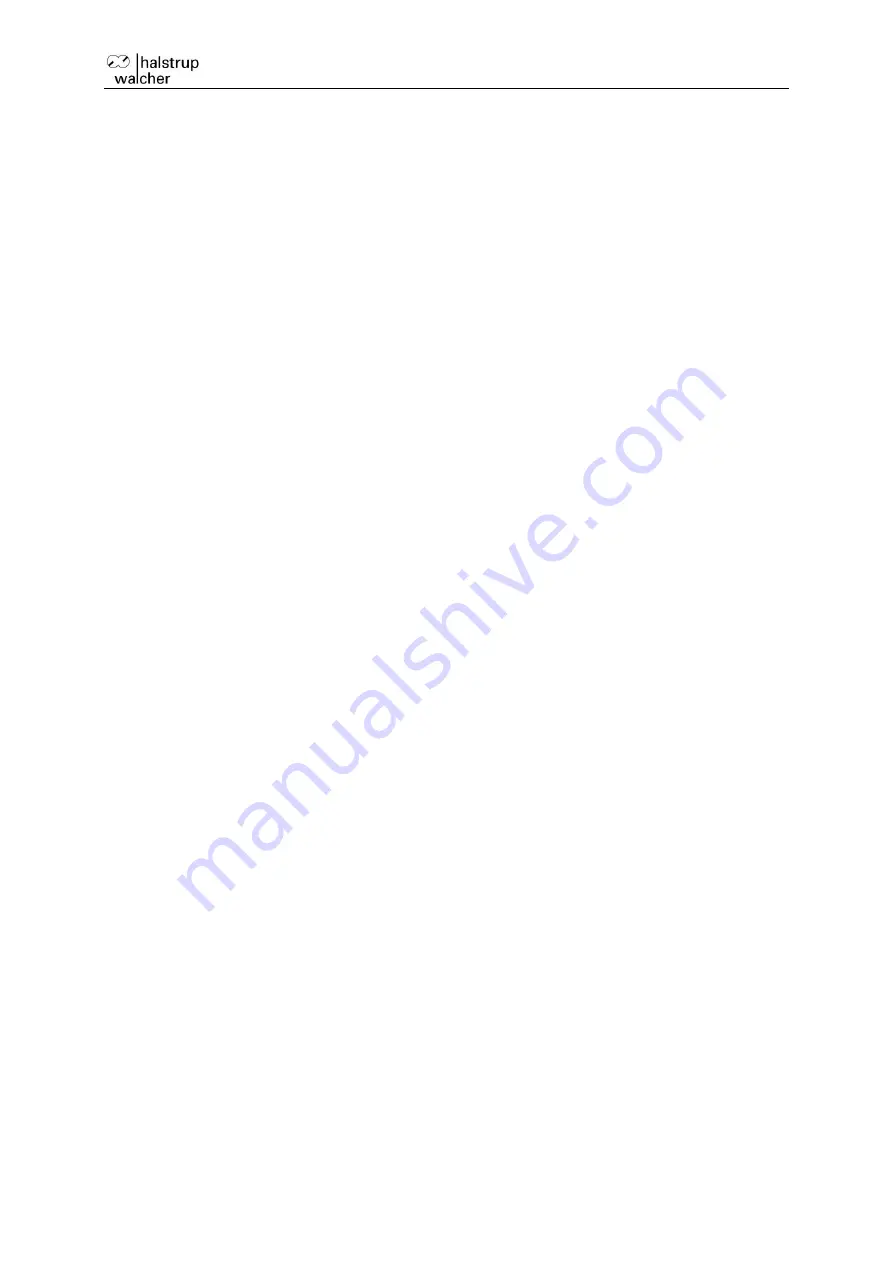
Instruction Manual PSx3xxEIP
27
2.9.5. Detailed description of control bits
Bit 0
:
manual run to larger values
Bit 1
:
manual run to smaller values
Bit 2
:
transfer target value
The target value in the process data is being accepted as a new valid target
value, if this bit is set. A positioning run which starts simultanously or later
uses this target value as new target position. If together with taking over the
target value the positioning run s
hall start immediately, bit 4 (“release”) has to
be set additionally.
If bit 2 is not set, the target value will not be taken over, instead there might be
a positioning run to the target value which has been sent at last and which has
been marked as valid.
Bit 3
:
Enable manual movement in jog mode: In jog mode (movement by keys if bit
5 is set; or with bit 8 or 9 set in the control word if bits 4 and 5 are not set),
manual movement is only activated if bit is set, when the key is pressed for a
long time (or a jog movement bit is activated for a long time). If the bit is
cleared, only single steps are possible in jog mode.
Bit 4
:
Release
Run commands will only be executed if this bit is set.
This bit must be set for positioning runs and manual runs.
If this bit is cleared during a run, the run will be aborted and status bit 5 will be
set (“positioning run aborted”).
Bit 5
:
Enable jog mode with keys: If the bus connection is active, jog mode via keys
is only possible if this bit is set and bit 4 is not set. For jog operation via bus
(bits 8 or 9 in the control word), this bit must not be set.
Bit 6
:
Driving without a loop
If this bit is set, all destinations are approached directly during positioning
movements (regardless of the current value of par. 42) without any loop.
Bit 7
:
Execute switch-on loop
5/8 turns against loop direction and then 5/8 in loop direction with manual
speed (for default value of loop length par. 42). The control word is ignored
during a switch-on loop movement until it changes. Thus a switch-on loop can
be aborted with control word = 0.
Bit 8
:
Jog to larger values: Corresponds functionally to a pressed key forward (bit 3
in status). Bits 4 must be set in this operating mode!
Bit 9
:
Jog to smaller values: Functionally corresponds to a pressed key backwards
(bit 2 in status). Bits 4 must be set in this operating mode!
Bits 10-15
: reserved, must be programmed to 0