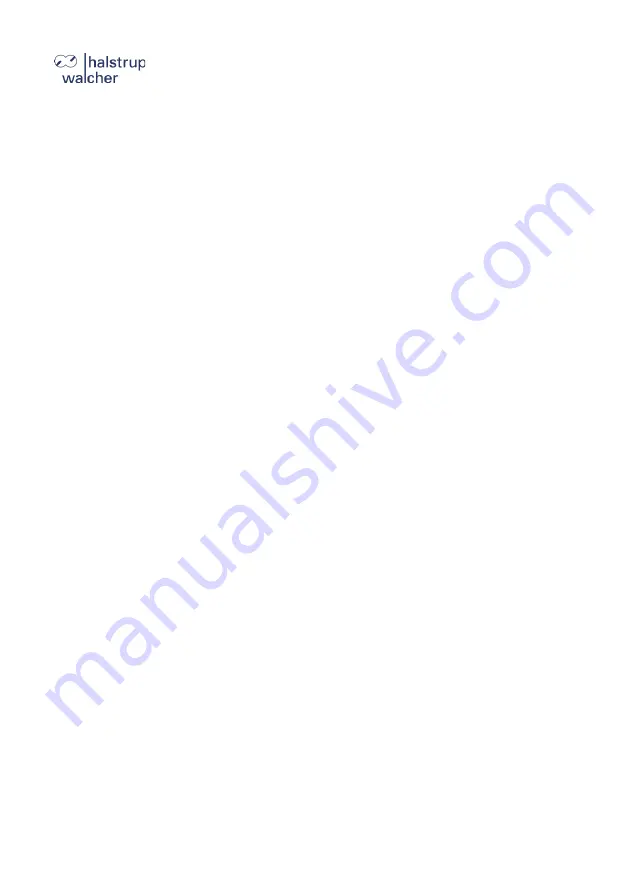
Description of IO-Link
7100.006434_Bus description_PSD4xx_IO_J_ENG
30
2022-09-13
Bit 6
Drive is running
This bit is set:
-
when the drive is rotating
This bit is reset:
-
when the drive is at a standstill
Bit 7
Temperature exceeded
This bit is set:
-
when the internal device temperature rises above the limit value from ISDU 180
This bit is reset:
-
when the internal device temperature falls below the limit value by 5 °C
Bit 8
Movement opposite loop direction
This bit is set:
-
after power up or a reset command
(any backlash in the driven spindle is not yet eliminated)
-
during manual runs in the direction opposite that of the positioning run
(a subsequent manual run in the direction of the positioning run will no longer
delete this bit)
-
during a positioning sequence in the direction opposite to that of the loop
direction
This bit is reset:
-
when a transferred target position has been reached successfully
(in the direction of the loop)
-
after the start-up reference loop
Bit 9
Error bit
This bit is set:
-
if an unrecoverable error in flash memory occurred
-
when an internal problem is detected when calculating the position
No more run commands may be transmitted when the error bit is set!
This bit is reset:
-
only by resetting the drive (reset command or switching off and on again)