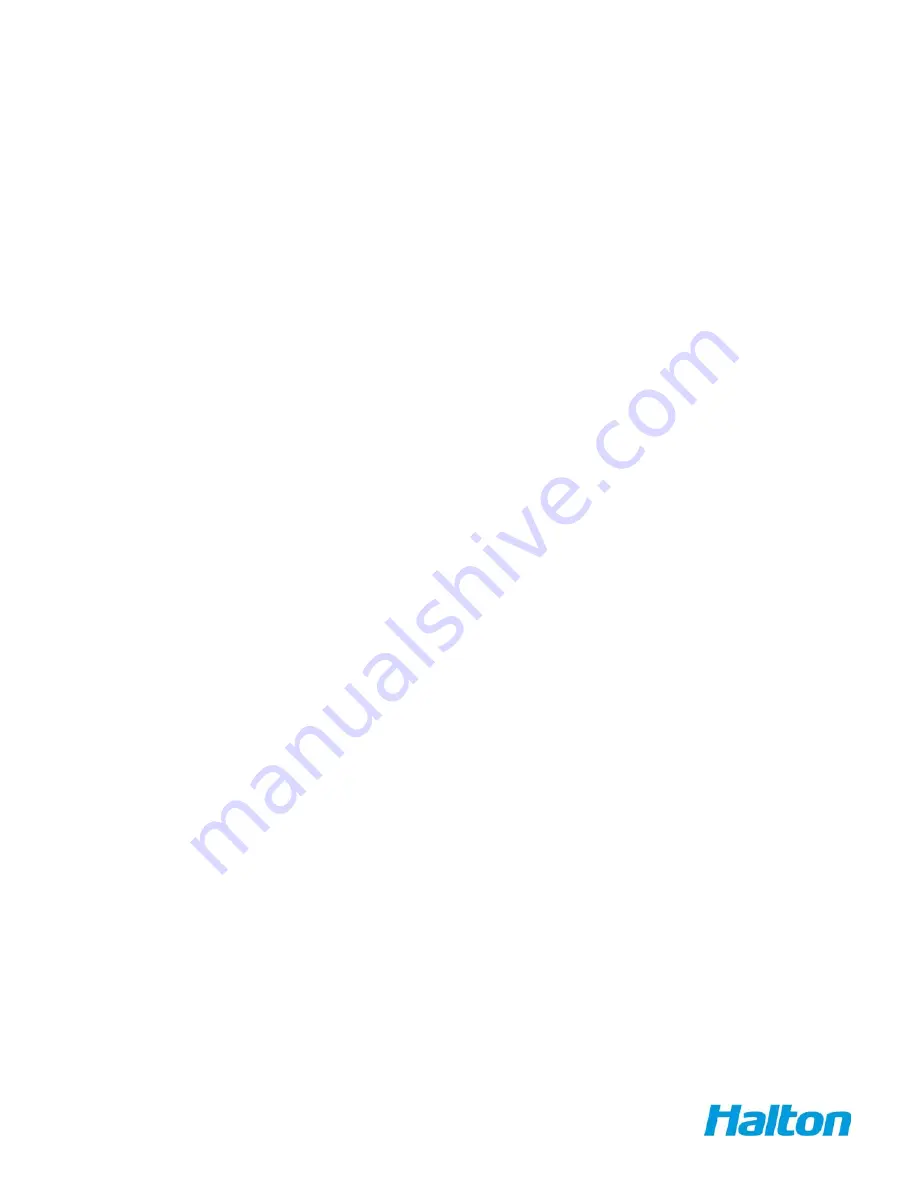
21
Capture Jet
®
Water Wash
Operation & Maintenance & Service Manual
CJ
O
WWM/0
120
09/re
v1/EN
CONTROL PANEL COMPONENT FUNCTIONS
Water Shut Off Valves:
There are two water shut off valves on both the hot and cold water lines, so that the components
in both hot and cold water lines can be isolated for easy removal.
Pressure Reducing Valves:
These valves are located in the hot and cold water lines to reduce the operating pressure to
25 PSI (172 kPa).
Solenoid Valves:
There is a solenoid valve in both the hot and cold water lines to automatically control the water flow.
Detergent Pump:
This pump is used to inject a controlled amount of the detergent into the hot water line when in wash
mode.
Fuse Block & Terminal Strip:
To provide a 5 amp fuse to to protect the electrical components in the control panel.
Cold Water Pressure Gauge:
This gauge is used to check the cold water pressure on the outlet side of the pressure
reducing valve. Should read 25 PSI (138 kPa) while in operation.
Plug Hot Water Line:
This plug can be removed and a pressure gauge or thermometer screwed inot the hole for field
termperature and pressure reading.
Cold Water and Hot Water Strainers:
The strainers located in the PRV valve are used to strain out dirt from the water
flow and to protect the solenoid valves and water nozzles from plugging up.
Detergent PUmp Check Valves:
This valve stops the detergent in the pump and tube from draining back down into the
detergent tank when the pump is not in operation, eliminating the need to continually prime the pump.
PLC Siemens:
Controls all functions of the panel. The PLC takes care of alarms as well.
Display - TD200:
Displays all messages, for system operation and alarms in the system.
METHODS OF MOUNTING CONTROL PANEL
Location of control panel is determined by the kitchen equipment contractor. The recommended mounting height above
the finished floor and type (recessed or surface) is indicated on the show drawing.
RECESSED CONTROL PANEL
Recessed mounted models. The panel can be shipped early to allow cabinet to be built into wall. Fastening as per surface
mount units.
SURFACE MOUNT CONTROL PANEL
Surface mounted models are shipped as complete units. The installer must drill holes in the back of the cabinet and com-
ponents plate to suire wall structure and securely fasten pabel to wall with lag or butterfly bolts.