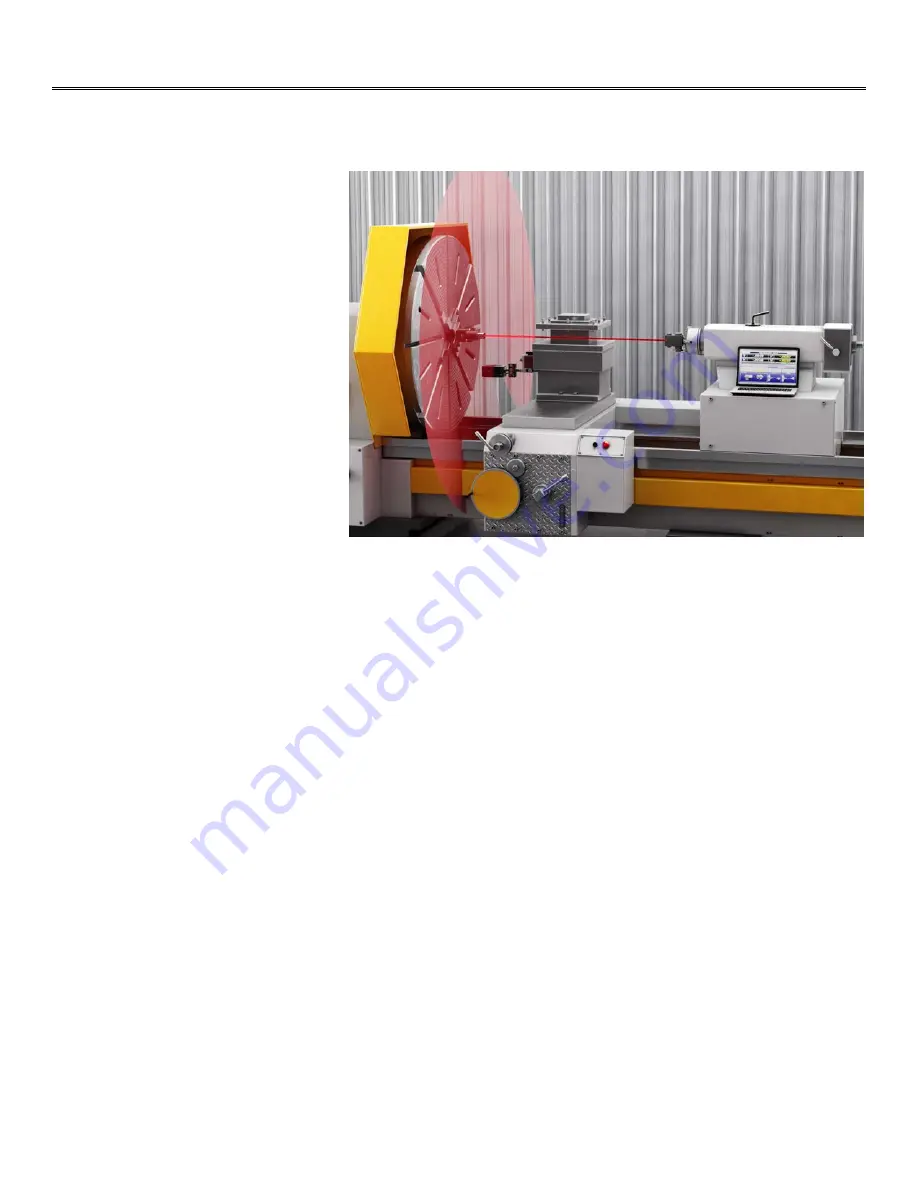
1
L-702/L-702SP Spindle and Multi-Turn Alignment System
The L-702/L-702SP 4-Axis Spindle & Multi-Turn Machine Alignment System is a complete alignment system for
aligning spindles on lathes, turning centers and multi-turn machines. There are two configurations:
•
L-702
– This version is used only to
align spindles to subspindles, check
flatness and straightness of the lathe
and turning-center guideways, and
alignment of headstocks to tailstocks.
It can also be used to check the
parallelism of the headstock to the
lathe-bed guideways.
•
L-702SP
– This version adds an
automatically rotating turret that
sweeps a laser scan plane that is
perpendicular to the spindle laser,
which allows the capability to check
squareness of cross slides or
machining axes on lathes and multi-
turn machines. With an added
magnetic leveling base accessory, the
L-702SP can also be used to check
machine leveling, alignment and axis
squareness.
System Features
•
Fast
: Easy setups let you do a quick alignment check in 20 minutes and get full alignment data in 30-40 minutes
on most machines.
•
Easy
: Laser and target mount directly into the spindle and tailstock, respectively, allowing the entire length of
even the largest lathes to be quickly and easily aligned without changing setups, replacing cumbersome and
impractical alignment test bars. With built-in squareness capability, checking cross-slide squareness is a 5-
minute operation
•
Accurate
: Ultra-high resolution of up to .00001 in. (0.00025 mm) combined with software to correct mounting
errors produces a very accurate alignment, less than .0001 in. (0.0025 mm) and .0001 in/ft (0.0083 mm/m) under
good environmental conditions.
•
Lathe9 Software:
Large, easy-to-read alignment displays, live alignment data and spindle graphics, and a six-
step procedure that guides users through the alignment with on-screen help instructions.
•
Spindle8 Software:
Designed for transfer-line spindle alignments, Spindle8 features large, easy-to-read
alignment displays, live alignment data and spindle graphics, and a four-step procedure that guides users through
aligning spindles to master parts on transfer-line spindle applications
Summary of Contents for L-702
Page 1: ......
Page 7: ...4 L 702 L 702SP Laser Dimensions...