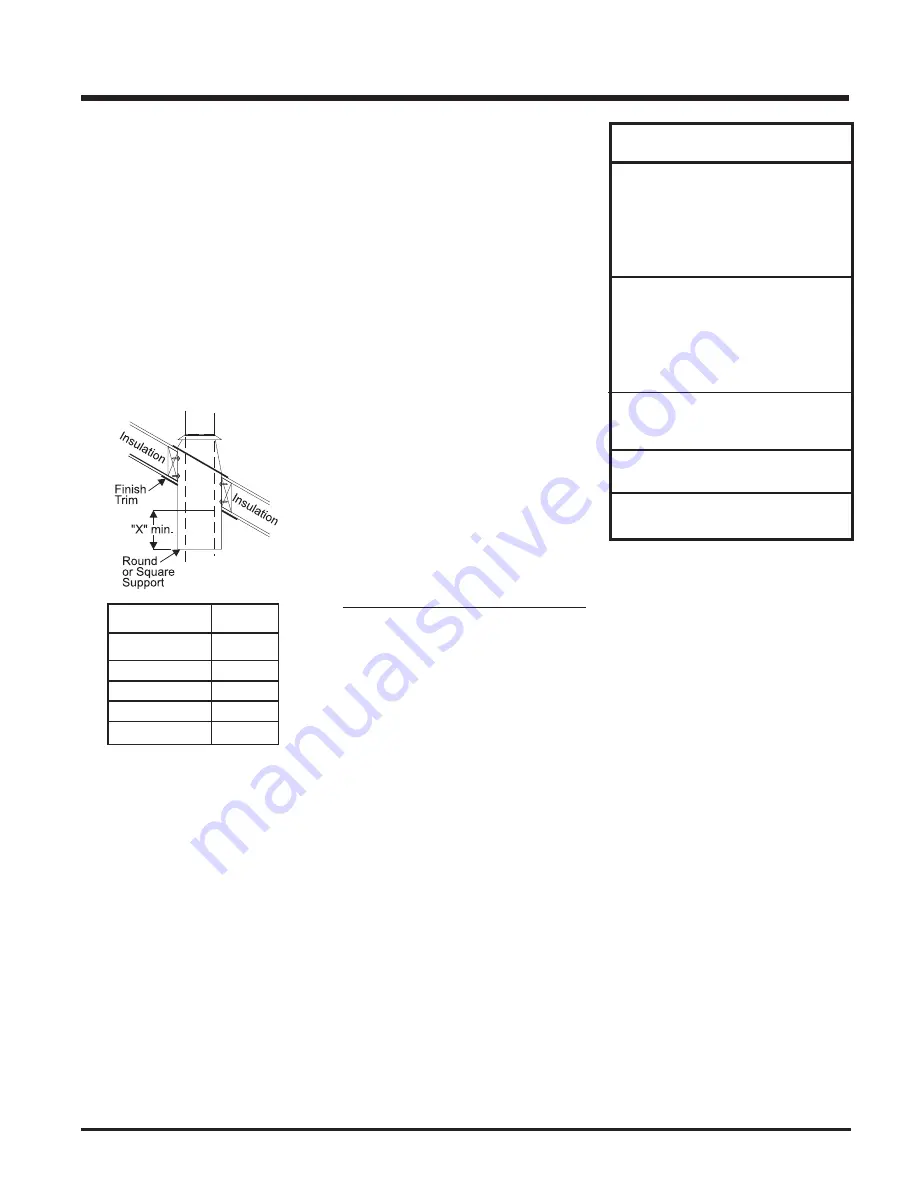
Hampton HG35-1 Direct Vent Freestanding Gas Stove
19
SYSTEM DATA
For 0 to 4500 feet altitude
Natural Gas
Max. Input Rating 34.7 mj.
Min. Input Rating 18 mj.
Orifi ce Size #33 DMS
Convertible to:
Max. Input Rating 31.6 mj.
Min. Input Rating 15 mj.
Orifi ce Size #37 DMS
LPG
Max. Input Rating 37 mj.
Min. Input Rating 20 mj.
Orifi ce Size #51 DMS
Convertible to:
Max. Input Rating 30.6 mj.
Min. Input Rating 16.8 mj.
Orifi ce Size #52 DMS
ULPG
Max. Input
30.6 mj.
Min. Input
16.8 mj.
Orifi ce Size
#52 DMS
Supply Pressure
Natural Gas
min. 1.13 kPa
LPG & ULPG
min. 2.75 kPa
Manifold Pressure
Natural Gas
0.95 kPa
LPG & ULPG
2.64 kPa
3)
Use appropriate roof fl ashing. Place the
fl ashing under the upper shingles and on top
of the lower shingles approximately half of
the fl ashing should be under the shingles.
4)
Assemble the desired lengths of Black Pipe
and Elbows necessary to reach from the
appliance adapter up through the support
box and fl ashing to proper height as per
Dia. 12, local codes or page 10. Ensure
that all pipe and elbow connections are in
their fully twist lock position.
5)
Ensure
fl ue is vertical and secure fl ashing to
the roof with roofi ng nails. Slide the storm
collar over the pipe section and seal with a
mastic.
6)
Twist lock the fl ue cap on to the last sec-
tion.
Support Extensions
Round (RDSE) or Square (SQSE)
Steep pitched cathedral ceilings may require
the use of a support extension. This piece fi ts
down inside the support and can be adjusted to
increase the support's length by up to 22". The
extension is attached to the support using the
eight metal screws provided. Be sure there is
at least a 2 inch overlap where the extension
joins the support.
CATHEDRAL CEILING
Round Support (RDS) &
Square Support (SQS)
If your home has a cathedral ceiling (no attic
space between the ceiling and the roof), install
the chimney and support as follows.
1)
Situate the chimney in a convenient loca-
tion as near as possible to the appliance
outlet. Cut and frame a hole in the roof for
the support. The sides of this hole must be
vertical with 1 1/4" clearance.
2)
Place the support in the opening. Lower it
to the correct height as determined by the
table and diagram below.
Using a level, make sure the support is
vertical. If the support extends above the
roof, cut it fl ush with the top of the roof.
Nail the support to the frame opening using
(8) 3" spiral nails or #8 x 1-1/2" screws.
Note: If you are using a 6" square support
you may fi nd it diffi cult to screw it
in place because it is fairly small
inside.
Simpson Dura-Vent has provided angle
brackets with this support which can be
screwed to the outside of the support
box and nailed to surrounding framing as
required. Use a minimum of four #8 x 1/2"
screws per bracket. In some cases these
brackets may need to be trimmed (e.g.:
to fi t under a fl ashing). Place the Finish
Collar around the support and fasten it to
the ceiling using the screws provided.
INSTALLATION
Slope
"X"
0/12 -
2/12
4"
2/12 -
7/12
5-1/2"
7/12 -
12/12
6-3/4"
12/12 - 24/12
7-1/2"
24/12+
12-1/2"
GAS CONNECTION
The gas line should be rigid pipe. Copper may
also be used if approved by AS5601-2004.
The gas connection at the valve is 1/2 male.
For minimum and maximum supply pressure
see the System Data Table.