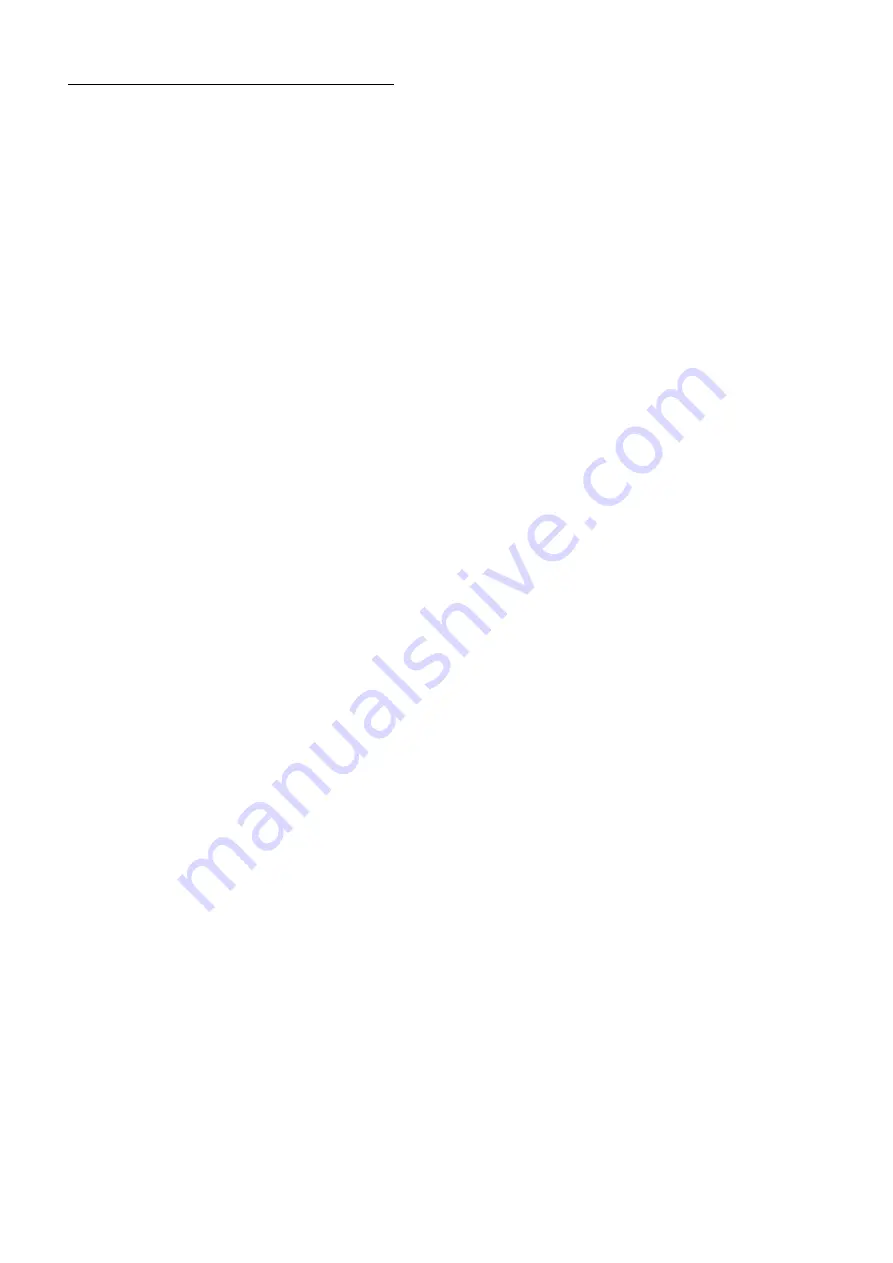
HAMWORTHY HEATING LTD
41
PUREWELL
Vari
Heat c
500001169/T
11.0 REPLACEMENT OF FAILED COMPONENTS
There are a number of components listed below which can be replaced simply and quickly by following the
given procedure. In each case carry out the appropriate part of the commissioning procedure & check the
operation of each component replaced. See
Section
7.3:Commissioning and Testing
NOTE: Isolate electrical supply to the boiler and turn off the gas supply after removing controls cover
and before commencing any servicing or component exchange procedure.
11.1 Igniter and Flame Probe Assembly
Both Igniter and flame probe are secured in the same manner.
Reference to Figure 11.1 shows position of
igniter assembly. To remove assembly disconnect the plug/socket on the supply lead and remove the screw
securing the igniter to the burner front panel. Figure 11.1 shows diagram of igniter assembly and relevant
components. Generally remove any loose sooty deposits and clean as required. Before renewing the Hot Surface
Igniter ensure the protective sleeve is removed from the new Igniter
(care is required as the Igniter element is
Fragile)
. Ensure positions of components are as recommended in Figure 11.1.
11.2 Safety Temperature Limiter (Limit Stat)
With the boiler front cover removed, the Limit Stat is situated on the rear of the control panel fascia bracket to the
left hand side of the main PCB. Remove the 'push on' spade connections from the temperature limiter body noting
position of coloured cables. Remove plastic cover (if fitted) and unscrew holding nut to detach temperature limiter
from housing. Gently feed the capillary back through the controls bulkhead. Re-set temperature limiter to 95°C.
Check the operation of the device by carefully applying a heat source to the bulb. Re-assemble temperature
limiter into controls housing ensuring correct cable notation. Refer to Figure 9.0.
11.3 Main Gas Valve.
NOTE!
Hamworthy Heating strongly recommend that a new gas valve assembly is fitted to ensure safe,
reliable operation of the boiler.
The gas valve is supplied as a factory set component & must not be tampered
with.
1)
Disconnect the gas valve electrical plug.
Remove the four socket head screws securing the gas valve inlet flange. Take the weight of the gas valve and
remove the four socket head screws securing the gas valve to the airbox lid (PV70c/90c/110c), welded bracket
with pipe (PV140c/PV180c) . Withdraw the gas valve.
2)
Always fit new ‘O’ rings to both inlet and outlet when replacing the gas valve.
Always test for gas soundness after replacement parts have been fitted.
Refer to
Section 7.1,
if necessary for valve integrity check procedure.
3)
Re-light the boiler using instructions on the inside of the door. Check for correct operation. If necessary, refer
to
Section 7.4 Commissioning the Boiler
, for correct procedures.
11.4 Combustion Fan
NOTE! To remove the fan, it is necessary to remove the gas valve & airbox (PV70c/90c/110c), or remove the
metal bracket fixing the venturi to the fan (PV140/PV180c).
Replacement on Models PV70c/PV95c/PV110c
1)
Disconnect the gas valve plug assembly from the gas valve. Disconnect the gas valve inlet flange from the gas
valve. Disconnect the 3 & 5 way electrical plugs from the fan body.
2)
Disconnect the fan/gas valve assembly from the burner body by removing the 4 M8 nuts securing the transition
duct to the burner.
3)
Remove the screws securing the airbox lid to the airbox and carefully store the lid & gas valve assembly.
4) Note correct orientation of the venturi with baffle
& remove the screws of the venturi. Remove the
screws securing the airbox to the fan. Carefully store all of the air inlet box components.
5)
Remove the screws securing the fan outlet to the burner transition duct. Beware there is a non return valve
fitted between these components.
6)
Re-assemble in reverse order using new gaskets where appropriate. After assembly and prior to re-fitting the
assembly to the burner, check for correct and free operation of the non return valve in the burner transition duct.
Replacement on Models PV140c - PV180c
1)
Repeat Steps 1 & 2 above.
2)
Unscrew the metal bracket from the gas valve & fan. See Figure 11.4.
Summary of Contents for Purewell VariHeat 70c
Page 2: ......
Page 43: ...HAMWORTHY HEATING LTD 37 PUREWELL VariHeat c 500001169 T Figure 8 3 11 Operating phases ...
Page 44: ...HAMWORTHY HEATING LTD 38 PUREWELL VariHeat c 500001169 T Figure 9 0 Boiler Wiring Schematic ...
Page 65: ...HAMWORTHY HEATING LTD 59 PUREWELL VariHeat c 500001169 T Figure E1 2 Typical Piping Layouts ...
Page 70: ...HAMWORTHY HEATING LTD 64 PUREWELL VariHeat c 500001169 T NOTES ...
Page 71: ......