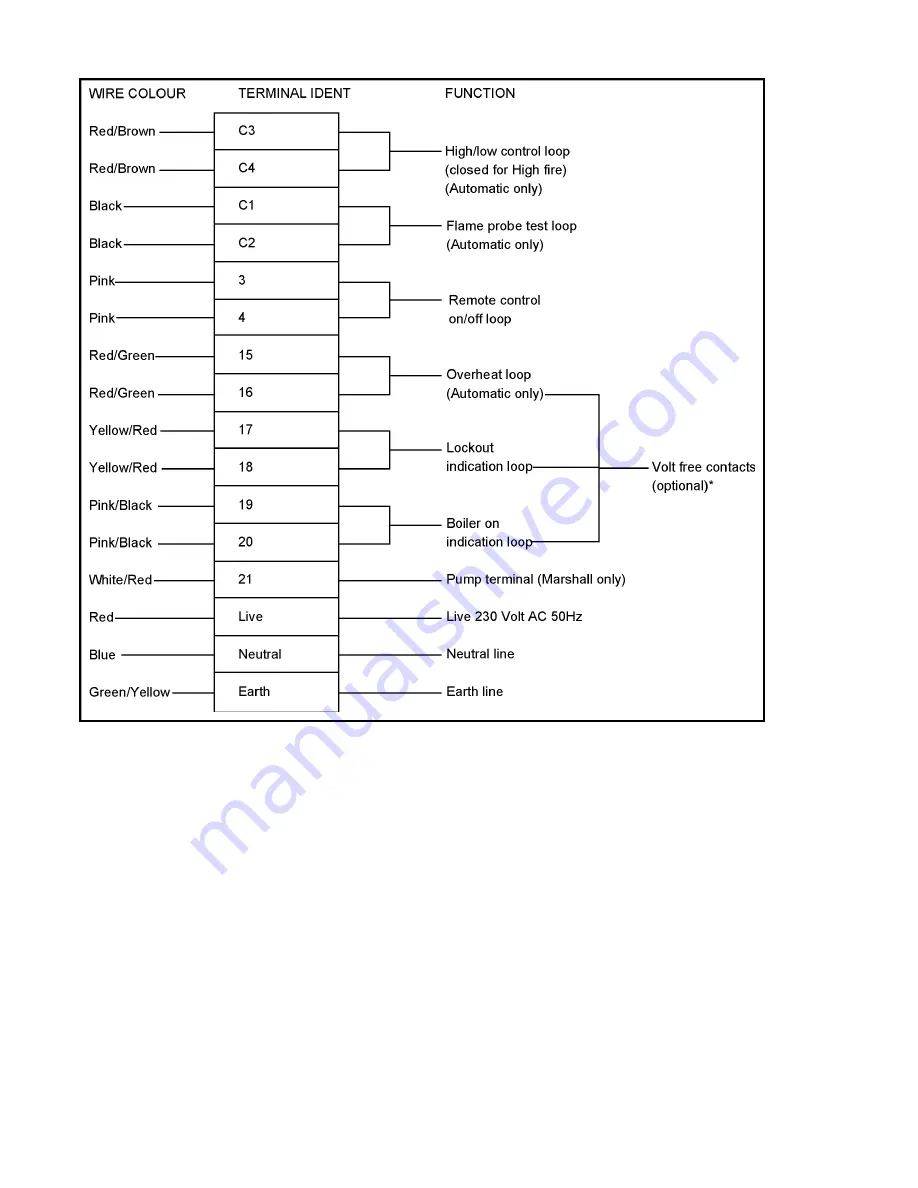
HAMWORTHY HEATING LTD. PUREWELL AUTOMATIC IGNITION 500001035/G
24
Figure No. 12 - Purewell Boiler Site Wiring Diagram (Automatic)
NOTE!....Maximum rating of a volt free contact(s) is : 3 Amperes Resistive
WARNING! External voltage MUST NOT be applied to remote stop/start terminals 3 & 4 or
high/low control loop terminals C3 & C4 or any terminals on the fascia.
NOTE! * Volt free contacts may have separate supply. Ensure all power supplies are
completely isolated prior to working on the electrical circuits of this appliance.