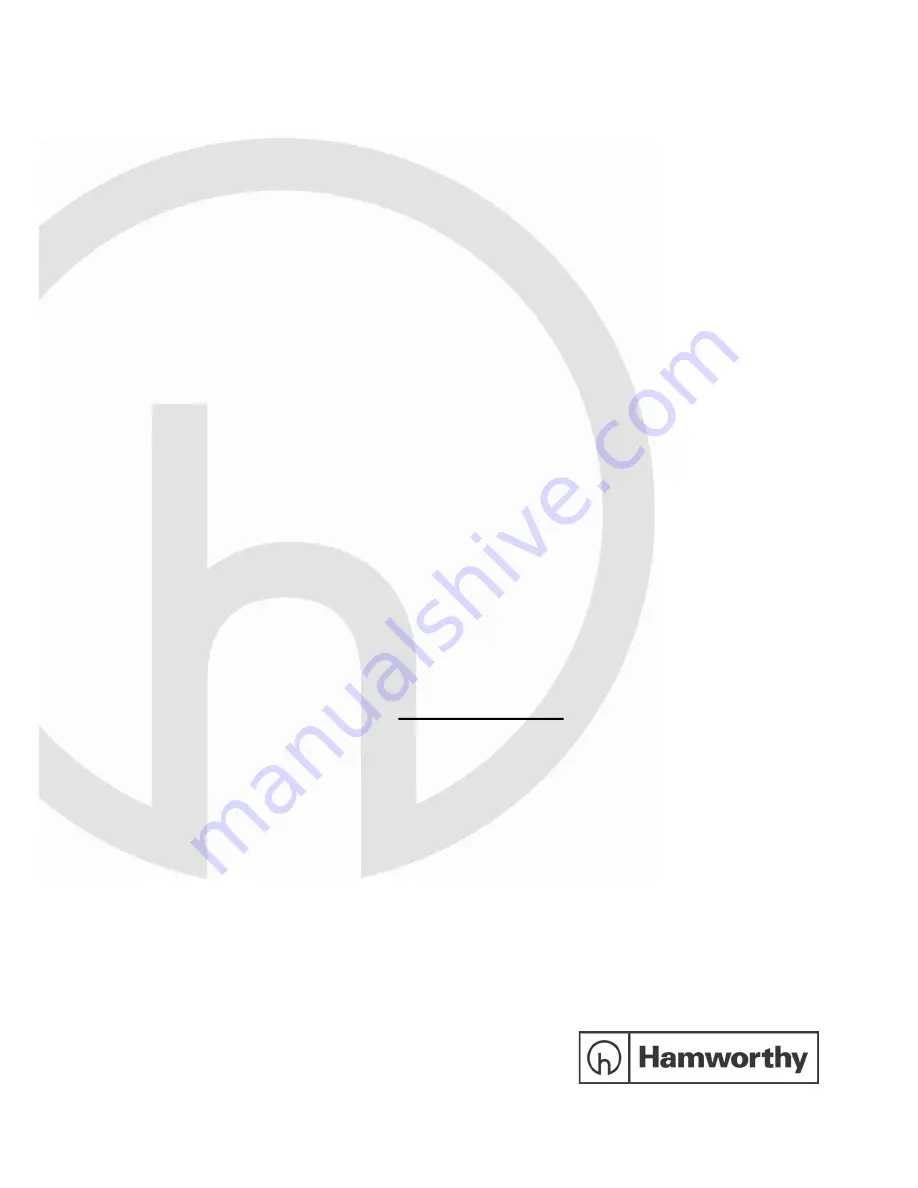
UPTON SERIES BOILERS
Floor Standing, Condensing , Open Flue,
Fully Modulating, Pre
-
Mix,
Gas Fired Boilers for Heating & Domestic
Hot Water Installations
Installation, Commissioning
and Operating Instructions
Models:
UF100
-
1, UF150
-
1, UF200
-
1, UF250
-
1, UF300
-
1 UF350
-
1
UF200
-
2, UF300
-
2, UF400
-
2, UF500
-
2, UF600
-
2 UF700
-
2
UF300
-
3, UF450
-
3, UF600
-
3, UF750
-
3, UF900
-
3 UF1050
-
3
NATURAL GAS I
2H
LPG Propane I
3P
IMPORTANT NOTE
THESE INSTRUCTIONS MUST BE READ AND
UNDERSTOOD BEFORE INSTALLING,
COMMISSIONING, OPERATING OR SERVICING
EQUIPMENT