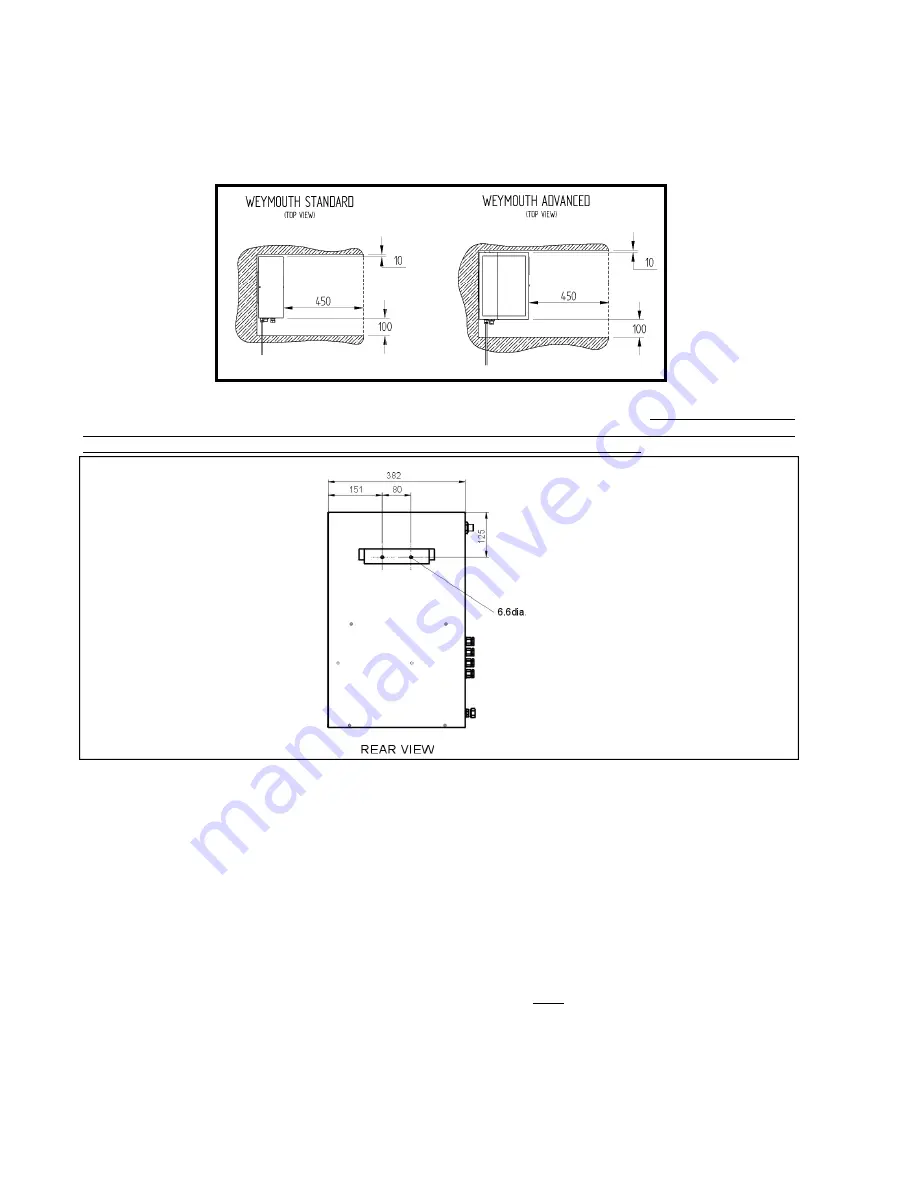
HAMWORTHY HEATING LTD
6
WEYMOUTH
500001112/C
6.0 INSTALLATION
The units are supplied inside strong cardboard boxes with foam padding and should be left in this packaging until
they arrive on site and are installed.
6.1 Location.
Figure 7 Recommended Clearance Dimensions
The units are designed for wall mounting. A mounting bracket is supplied inside the unit taped to the front of the
tank. It is intended that this bracket should be fixed to the wall and the unit hung from it. Each unit also has two
holes in the back of the chassis for extra security. The corresponding holes in the wall should be drilled to suit
once the unit is mounted on its bracket. The bracket dimensions are shown in fig 8 below.
The pressurisation units can be installed on the floor if they are secured to a wall or support using screws
through the holes in the chassis.
6.2 Pipework Connections (Shown in Figure 9)
1)
Mains water connection (½" BSP Male).
The units have a type ‘AF’ air gap to prevent backflow in accordance with Water Supply (Water Fittings)
Regulations 1999. The water supply connection must conform to all local WRAS regulations.
2) Overflow connection (22 mm and ¾” Female).
Overflow should be piped to where it will be safe but visible so it will be noticed and corrected.
3) System connection.
The system connection is via a 15MM compression fitting. The unit must be connected to the system by an
antigravity loop (see Figure 3). The antigravity loop must be made in pipe-work no smaller than the expansion
vessel connection, and have a minimum height of 2 metres. It should include a lock-shield (or lockable) valve at
the system connection point for servicing and an automatic air vent fitted at the highest point of the loop. The
antigravity loop must not be lagged but can be fitted with an optional kit to prevent freezing. Consult Hamworthy
Heating for details. The pipe-work and fittings must be pressure tested to 1.5 times the safety valve lift pressure.
Figure 8 - Mounting
Bracket Details