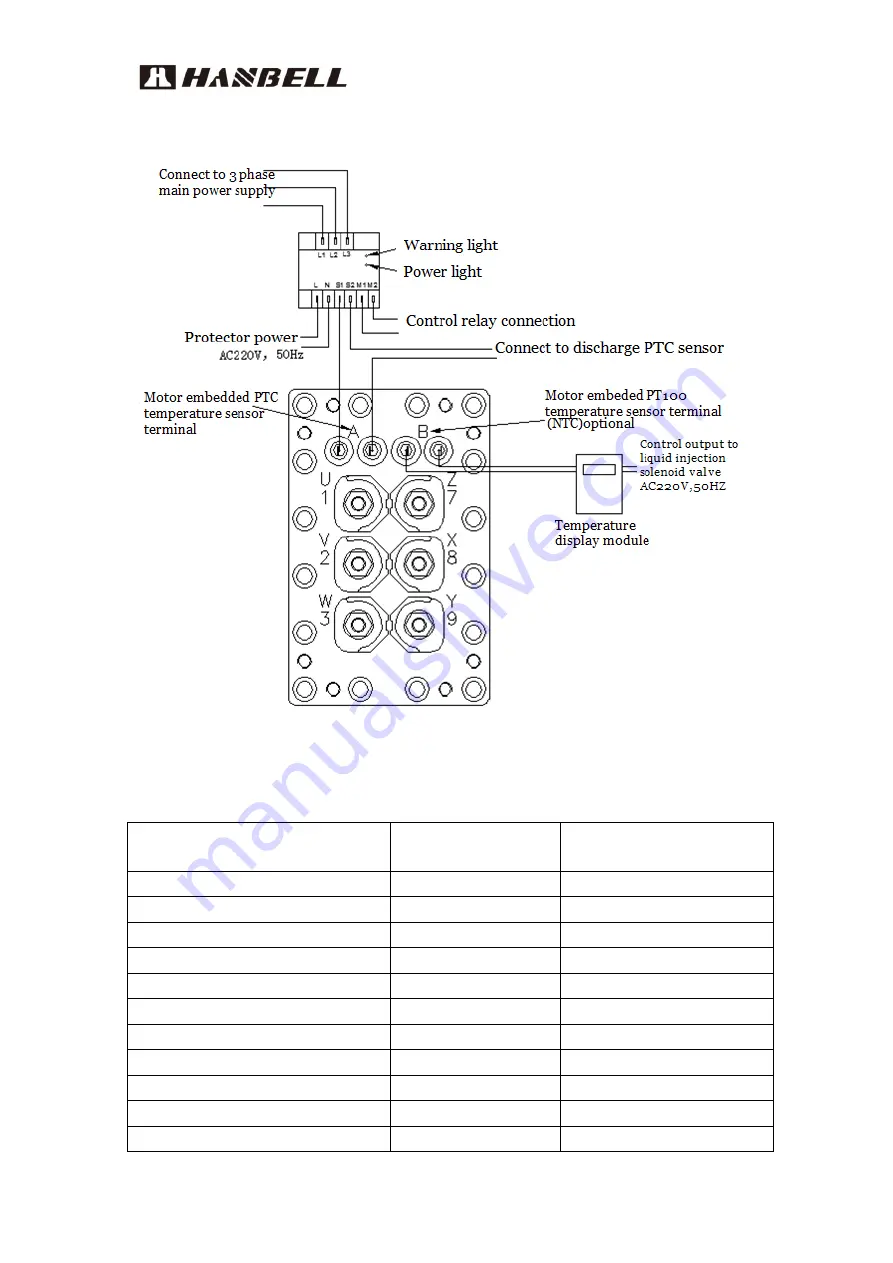
LT-S-(L) Technical manual
Terminal coverplate
Figure 6-3. Terminal cover plate graph
Fig 6-2.Nuts specification for bolts on terminal cover plate
Model
Specification
Torque
(
N.m
)
LT-S-20/10
M12 NUT
35
LT-S-30/12
M12 NUT
35
LT-S-45/20
M12 NUT
35
LT-S-55/25
M12 NUT
35
LT-S-65/32
M12 NUT
35
LT-S-83/41
M12 NUT
35
LT-S-20/10-L
M12 NUT
35
LT-S-45/20-L
M16 NUT
50
LT-S-55/25-L
M16 NUT
50
LT-S-65/32-L
M16 NUT
50
LT-S-83/41-L
M16 NUT
50