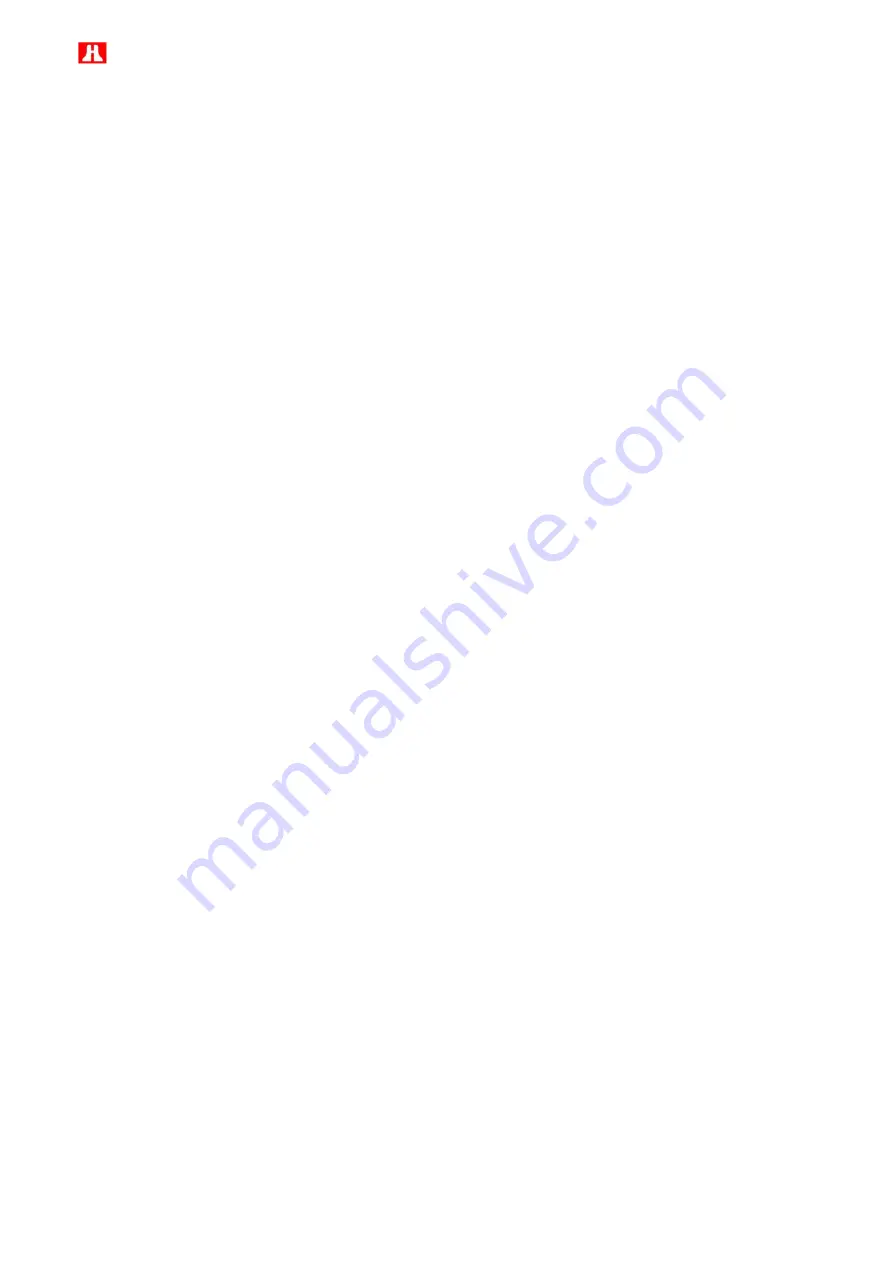
88
operating conditions. Otherwise this can indicate excessive liquid in the suction gas.
7. Avoid touching the compressor surface during compressor operation.
8. Don
’t remove any parts of compressor before release the compressor inner pressure.
9. The discharge temperature of compressor is recommended to be controlled at 80
℃
for R22 and HFC
application. Normally the discharge temperature doesn
’t increase quickly after starting. If it increases quickly
during commissioning, user should review the oil supply situation and additional cooling status.
10. The supply oil temperature should be kept below 60
℃
for R22 and HFC application.
11. The oil level in oil separator might slightly drop after the start-up. A lower level happened by gas or air spot
which is existed in oil circuit. If the level continuously goes down, an oil separator problem should be assumed.
User should check the working condition and find out the problem during the commissioning.
12. During the commissioning, user should listen if any abnormal noise comes from compressor
’s bearing seat or
compression casing. Normally a middle tone of rhythmical sound can be obtained. Irregular, high tone and
metallic noise show some abnormal conditions that the compressor is passing through. User should stop the
compressor immediately and find out the root cause of abnormal noise.
13. Vibration shall be checked carefully by using a vibration analyzer on compressor casing, the surface of the
base frame and piping. Compressor itself doesn
’t generate excessive vibration if mechanical condition and
shaft alignment are normal. Therefore, resonance should be often the cause of vibrations.
14. Normally the pressure drop at oil filter should be around 0 to 0.5 bar. If the pressure drop is continues rising
and reaches 1 bar. The oil filter cartridge should be cleaned or replaced to ensure a sufficient oil supply.
15. Normally the pressure drop at suction strainer is around 0 to 0.2 bar. If the pressure drop is continues rising
and reaches 0.5 bar. The suction strainer should be cleaned or replaced immediately.
16. Check sight glass on liquid line to see the supply condition of refrigerant.
17. Check suction gas superheat not only at 100% capacity, but also 75%, 50% and 25% capacity to ensure
sufficient superheat for system operation.
18. Avoid slugging compressor with liquid refrigerant. Make certain that adequate superheat or properly size
suction accumulator is applied to avoid dumping liquid refrigerant into compressor. Keeping liquid injection
valves properly adjusted and in good condition to avoid flooding compressor with liquid.
19. The whole plant, especially the pipelines and capillary tubes must be checked for abnormal vibrations.
Contact HANBELL or local distributor if any abnormal vibrations or noise found while the compressor is
running.
20. The running condition of compressor after commissioning at the job-site should be adjusted as; the discharge
temperature will be at least 20K above the saturated condensing temperature and the suction vapor
superheat should be within 10K to the saturated evaporating temperature.
21. Regularly check-up the plant according to national regulations and the following items should also be
checked:
-
Operating data of the machine
-
Check the lubrication/level of oil
-
All compressor monitoring parts
-
Check electrical cable connections and tightness
Summary of Contents for RC2-F Series
Page 6: ...5 2 2 Compressor outline...
Page 7: ...6...
Page 8: ...7...
Page 9: ...8...
Page 10: ...9...
Page 11: ...10...
Page 12: ...11...
Page 13: ...12...
Page 14: ...13...
Page 15: ...14...
Page 16: ...15...
Page 17: ...16...
Page 18: ...17...
Page 19: ...18...
Page 20: ...19...
Page 21: ...20...
Page 22: ...21...
Page 23: ...22...
Page 24: ...23...
Page 25: ...24...
Page 26: ...25...
Page 27: ...26...
Page 85: ...84 Horizontal External Oil Separator OS80 Horizontal External Oil Separator OS100 OS125 OS150...