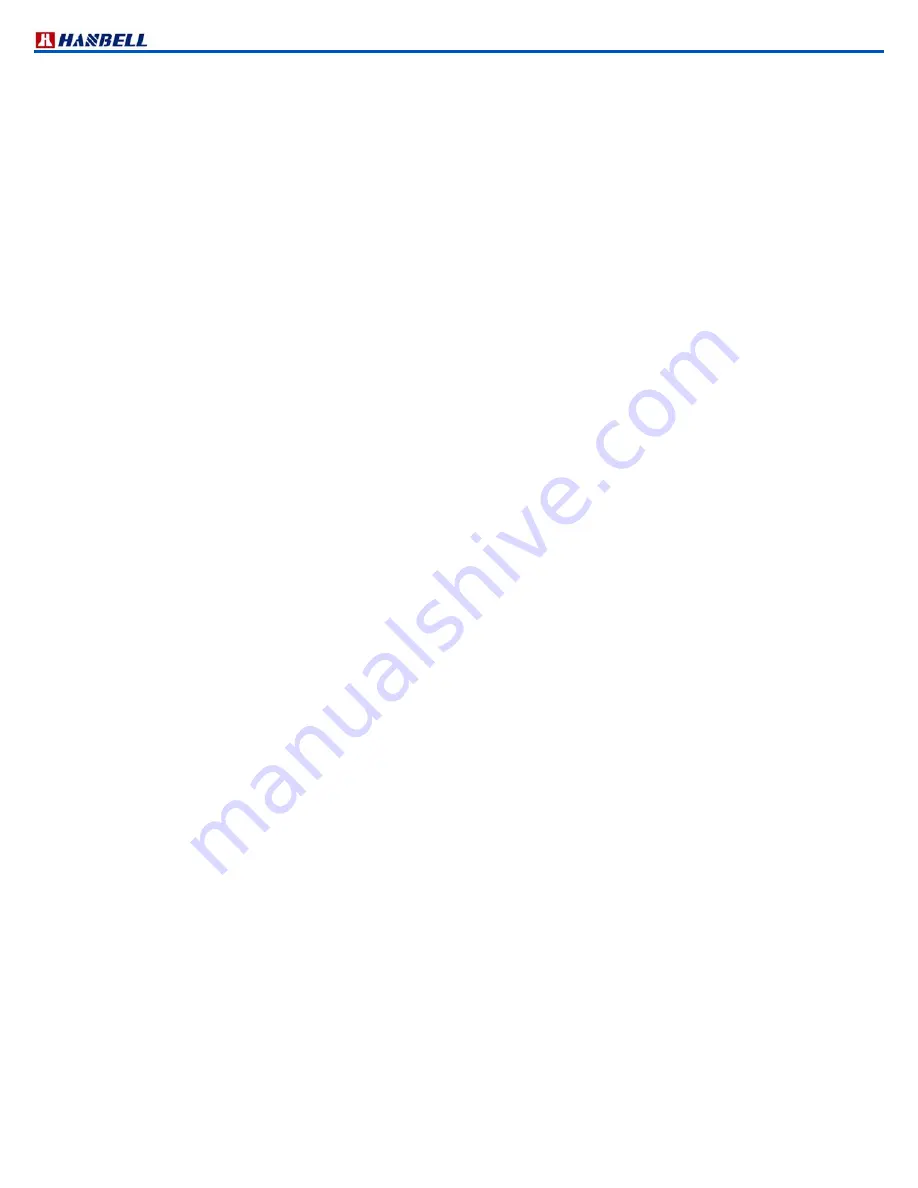
Technical Manual
VERSION 2.0 -10-18-2018
20
3.2 Precautions of changing oil
1. Use only qualified oil and do not mix different brands of oil together. Selection of oil should match characteristics of
the refrigerant used. Some types of synthetic oil are incompatible with mineral oil. Oil remained in the compressor
should be totally cleaned up in the system before charging different brands of oil. Charge the compressor with oil for
the first start and then change it into new oil again to ensure that there’s no mix at all.
2. When using polyester oil for chiller systems, please make sure not to expose oil to the atmosphere for prevention
of change in its property. Therefore, it is necessary to vacuum the system completely when installing the compressor.
3. In order to ensure no moisture inside the system, it is suggested to clean the system by charging it with dry Nitrogen
and then vacuum it repeatedly as long as possible.
4. It is a must to change the oil in motor burned out case, because acid debris may still remain inside the system.
Please follow the procedures mentioned above to change oil in the system. Check acidity of oil after 72 hours of
operation and then change it again until acidity of oil becomes normal.
5. Please contact Hanbell local distributors/agents for selection of oil.
3.3 Oil change
1. Change oil periodically: Check lubrication oil every 10,000 hours of continuous running. For the first operation of the
compressor, it is recommended to change the oil and clean the external oil filter after running 2,000 hours. Check the
system whether clean or not and then change oil every 20,000 hours or after 3 years’ continuous running while the
system operates in good condition.
2. Avoid clogging in oil filter with debris or swarf which may cause failure in bearings. An optional oil pressure
differential switch is recommended to be installed. The switch will trip when the oil pressure differential between the
primary and secondary sides reaches the critical point and then the compressor will automatically shut down to prevent
the bearings from damage due to oil loss.
Summary of Contents for RC2 Series
Page 24: ...Technical Manual VERSION 2 0 10 18 2018 24 UNIT SI mm Imperial in UNIT SI mm Imperial in ...
Page 25: ...Technical Manual VERSION 2 0 10 18 2018 25 SI mm Imperial in UNIT UNIT SI mm Imperial in ...
Page 26: ...Technical Manual VERSION 2 0 10 18 2018 26 SI mm Imperial in UNIT UNIT SI mm Imperial in ...
Page 27: ...Technical Manual VERSION 2 0 10 18 2018 27 UNIT SI mm Imperial in ...
Page 28: ...Technical Manual VERSION 2 0 10 18 2018 28 ...
Page 29: ...Technical Manual VERSION 2 0 10 18 2018 29 UNIT SI mm Imperial in ...
Page 30: ...Technical Manual VERSION 2 0 10 18 2018 30 ...
Page 31: ...Technical Manual VERSION 2 0 10 18 2018 31 ...
Page 32: ...Technical Manual VERSION 2 0 10 18 2018 32 ...
Page 33: ...Technical Manual VERSION 2 0 10 18 2018 33 ...
Page 34: ...Technical Manual VERSION 2 0 10 18 2018 34 UNIT SI mm Imperial in ...
Page 35: ...Technical Manual VERSION 2 0 10 18 2018 35 2 RC2 B outline drawings ...
Page 36: ...Technical Manual VERSION 2 0 10 18 2018 36 ...
Page 37: ...Technical Manual VERSION 2 0 10 18 2018 37 ...
Page 38: ...Technical Manual VERSION 2 0 10 18 2018 38 ...
Page 39: ...Technical Manual VERSION 2 0 10 18 2018 39 ...
Page 40: ...Technical Manual VERSION 2 0 10 18 2018 40 ...
Page 41: ...Technical Manual VERSION 2 0 10 18 2018 41 ...
Page 42: ...Technical Manual VERSION 2 0 10 18 2018 42 ...
Page 43: ...Technical Manual VERSION 2 0 10 18 2018 43 ...
Page 44: ...Technical Manual VERSION 2 0 10 18 2018 44 SI mm Imperial in UNIT ...
Page 60: ...Technical Manual VERSION 2 0 10 18 2018 60 ...
Page 83: ...Technical Manual VERSION 2 0 10 18 2018 83 NOTES ...