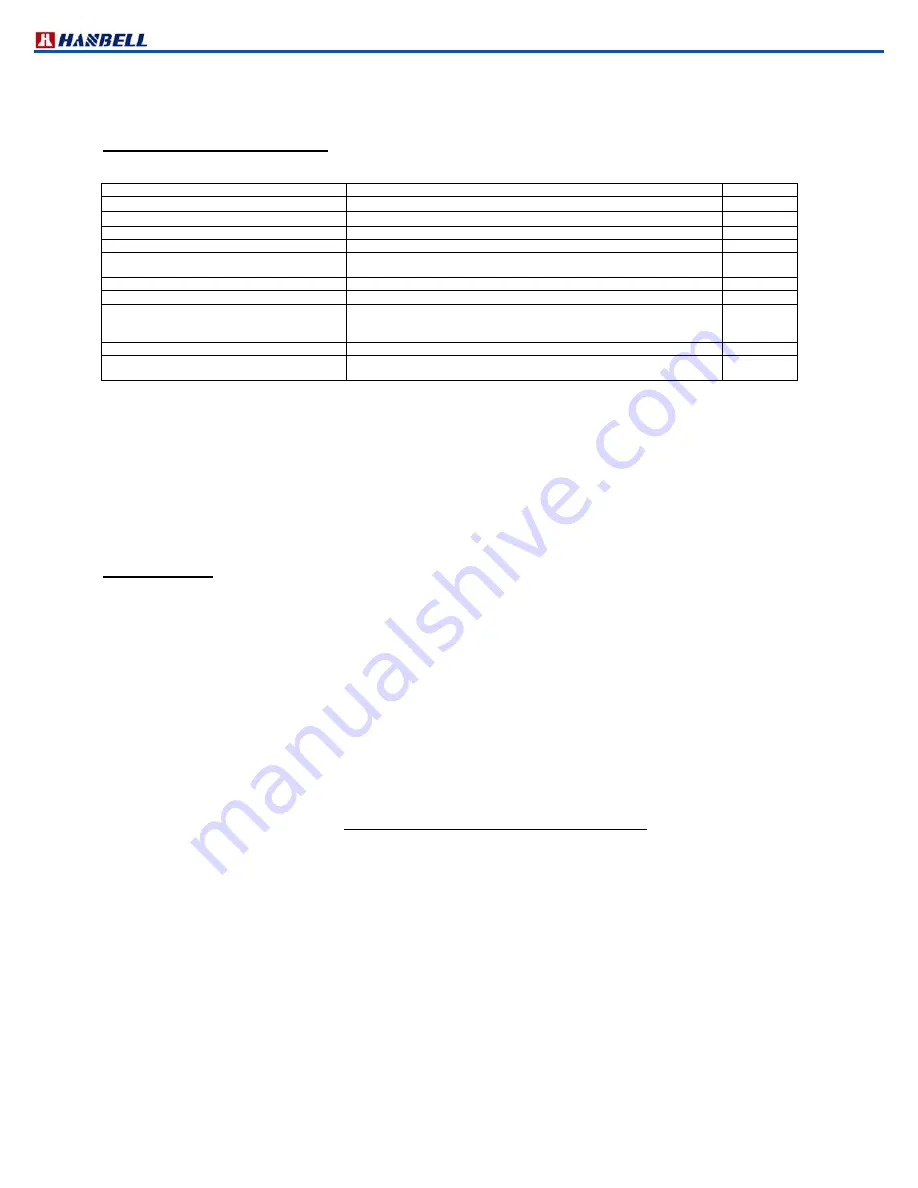
Technical Manual
VERSION 2.0 -10-18-2018
66
Caution: Ensure the power supply wiring and output motor wiring are connected to the correct terminals.
Any mistake could cause catastrophic failure to compressor motor.
5.2 Compressor protection devices
The table below shows the list of protection devices which are essential to protect the compressor and operate safely.
Follow the protection devices listed in the below table to ensure the compressor running under normal condition.
Protection device
Remark
Motor wiring temperature protector (PTC sensor) Cutout 110
℃
, cut in 100
℃
※
Standard
Discharge temperature protector (PTC sensor ) Cutout 110
℃
, cut in 100
℃
※
Standard
Phase reversal protector (INT69HBY)
Standard
Phase failure protector (INT69HBY)
Standard
Oil temperature sensor
Cutout 100
℃
, cut in 90
℃
(Aircooled, heat pump, or refrigeration system)
Cutout 80
℃
, cut in 70
℃
(Watercooled or flooded system)
Optional
Oil level switch
Time delay setting: 10~15 seconds
Optional
Oil filter pressure differential switch
Cutout 1.5 kg/cm
2
g
Optional
Oil pressure differential switch
Oil inlet pressure should be 4 kg/cm
2
g higher than the suction pressure.
When it is not 4kg/cm
2
g higher than the suction pressure, it is necessary to
add a minimum pressure valve or an oil pump to ensure proper oil supply
Optional
Oil flow switch
Time delay setting: 10~15 seconds
Optional
Pt100 or Pt1000 for liquid injection to motor
chamber.
Depends on customer’s application. Suggest Cut in 60
℃
, cut out 50
℃
Optional
※
Manual reset suggested
Motor thermistors and discharge thermistors are temperature sensors with quick response while the temperature
approach to their set point; thermistors must be connected in series to a controller (INT69HBY) in terminal box as a
guardian to protect compressor. Alarm lamp for this protector is required to be embedded on control panel as indicator.
Any intention to short controllers for starting of compressors is prohibited. It is beyond Hanbell’s warranty of
compressors if there is any action above mentioned found.
Note: when any protection device trips, please do troubleshooting and reset manually. Do not let the compressor reset
automatically after abnormal trip!
5.3 Power supply
1. Limitation of power supply
a. Voltage limitation b. Frequency :
Longterm running: rated voltage ±5% Rated frequency ±2%
Instant running: rated voltage ±10%
Note: In the region where the electricity power is unstable, install an additional hilow voltage protector with ± 5%
tolerance of normal voltage to ensure safe operating of the compressor.
2. Unbalanced voltages :
Unbalanced voltages usually occur because of variations in the load. When the load on one or more of the phases are
different from the other(s), unbalanced voltages will appear. This can be due to different impedances, or type and value
of loading in each phase. Unbalanced voltages can cause serious problems, particularly to the motor.
NEMA defines voltage unbalance as follows:
Percent voltage unbalance = 100 x
NEMA states that polyphase motors shall operate successfully under running conditions at rated load when voltage
unbalance at the motor terminals does not exceed 1%. Furthermore, operation of a motor with over 5% unbalance is
not recommended for it probably results in motor damage.
Unbalanced voltages at motor terminals cause phase current unbalance ranging from 6 to 10 times the percent of
voltage unbalance for a fully loaded motor. This causes motor over current resulting in excessive heat that shortens
motor life, and hence, eventual motor burnout. If the voltage unbalance is great enough, the reduced torque capability
might not be adequate for the application and the motor will not attain rated speed.
Some of the more common causes of unbalance voltages are :
●Unbalanced incoming utility supply
●Open delta connected transformer banks
●Large single phase distribution transformer in the system
●Open phase on the primary 3phase transformer in the distribution system
●Blow fuse on 3 phase bank of power factor improvement capacitors
●Unequal impedance in conductors of power supply wiring
●Unbalanced distribution of single phase loads such as lighting
●Unequal transformer tap settings
(maximum voltage deviation from average voltage)
(average voltage)
Summary of Contents for RC2 Series
Page 24: ...Technical Manual VERSION 2 0 10 18 2018 24 UNIT SI mm Imperial in UNIT SI mm Imperial in ...
Page 25: ...Technical Manual VERSION 2 0 10 18 2018 25 SI mm Imperial in UNIT UNIT SI mm Imperial in ...
Page 26: ...Technical Manual VERSION 2 0 10 18 2018 26 SI mm Imperial in UNIT UNIT SI mm Imperial in ...
Page 27: ...Technical Manual VERSION 2 0 10 18 2018 27 UNIT SI mm Imperial in ...
Page 28: ...Technical Manual VERSION 2 0 10 18 2018 28 ...
Page 29: ...Technical Manual VERSION 2 0 10 18 2018 29 UNIT SI mm Imperial in ...
Page 30: ...Technical Manual VERSION 2 0 10 18 2018 30 ...
Page 31: ...Technical Manual VERSION 2 0 10 18 2018 31 ...
Page 32: ...Technical Manual VERSION 2 0 10 18 2018 32 ...
Page 33: ...Technical Manual VERSION 2 0 10 18 2018 33 ...
Page 34: ...Technical Manual VERSION 2 0 10 18 2018 34 UNIT SI mm Imperial in ...
Page 35: ...Technical Manual VERSION 2 0 10 18 2018 35 2 RC2 B outline drawings ...
Page 36: ...Technical Manual VERSION 2 0 10 18 2018 36 ...
Page 37: ...Technical Manual VERSION 2 0 10 18 2018 37 ...
Page 38: ...Technical Manual VERSION 2 0 10 18 2018 38 ...
Page 39: ...Technical Manual VERSION 2 0 10 18 2018 39 ...
Page 40: ...Technical Manual VERSION 2 0 10 18 2018 40 ...
Page 41: ...Technical Manual VERSION 2 0 10 18 2018 41 ...
Page 42: ...Technical Manual VERSION 2 0 10 18 2018 42 ...
Page 43: ...Technical Manual VERSION 2 0 10 18 2018 43 ...
Page 44: ...Technical Manual VERSION 2 0 10 18 2018 44 SI mm Imperial in UNIT ...
Page 60: ...Technical Manual VERSION 2 0 10 18 2018 60 ...
Page 83: ...Technical Manual VERSION 2 0 10 18 2018 83 NOTES ...