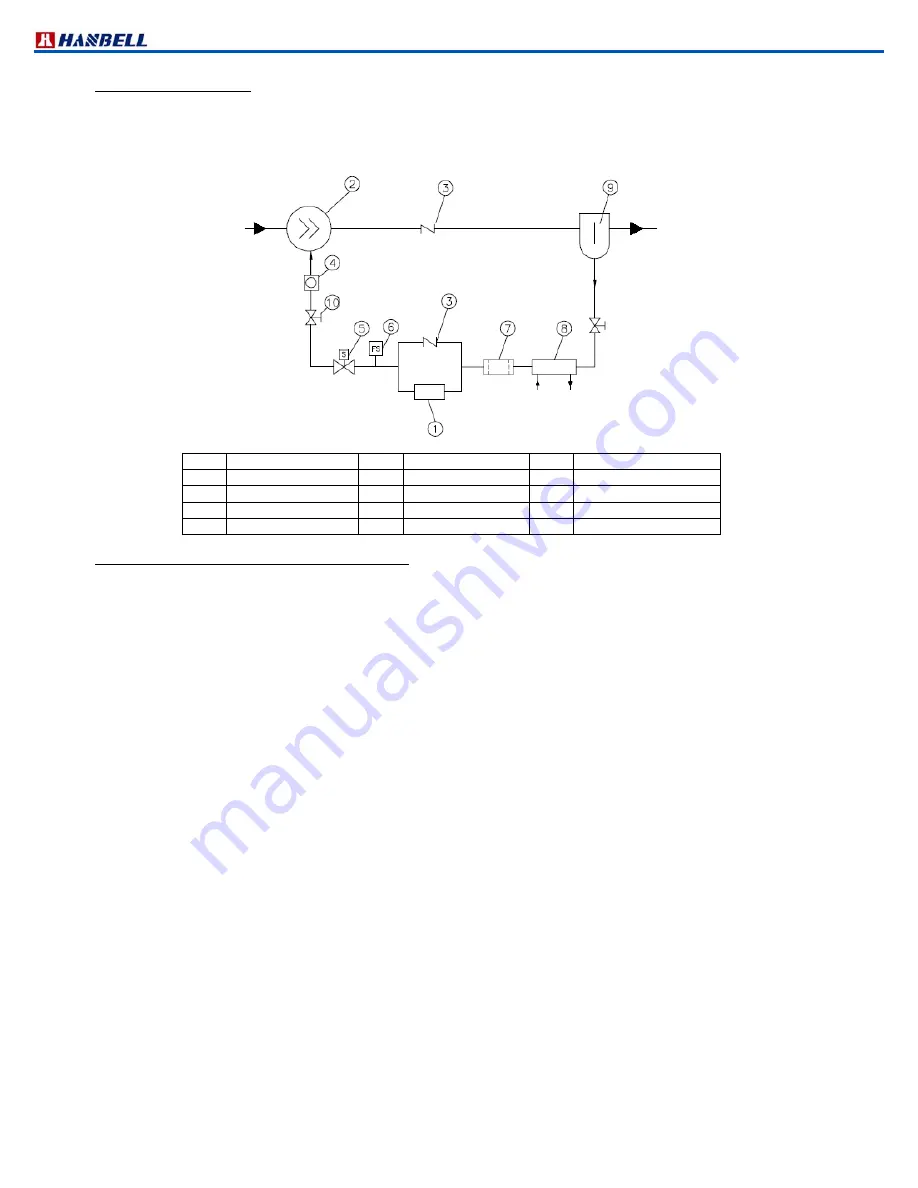
Technical Manual
VERSION 2.0 -10-18-2018
75
7.4 Oil pump application
An additional oil pump is recommended to install to the system when the differential pressure of oil pressure and
suction pressure is less than 4bar ( for example: water cooled flooder chiller). If compressor is operating at the
mentioned condition, the failure of modulation and lubrication will be happened and will seriously damage the
compressor. Besides the installation of additional oil pump, a high – low pressure differential switch is also
recommended to install to this kind of system. Please contact with Hanbell for more detailed information of oil pump.
Figure 72 Additional oil pump
Item Description
Item Description
Item Description
1
Oil pump
5
Solenoid valve
9
External oil separator
2
Compressor
6
Flow switch
10 Service valve
3
Check valve
7
Oil filter cartridge
4
Sight glass
8
Oil cooler
7.5 Important note of applications of compressor
1. Pump down
Do not
pump down the compressor on the chiller as a routine operation except only for temporary maintenance or a
long term shut down. Because pump down will cause extremely high temperature in the compression chamber and
overheat of the motor as well due to less amount of refrigerant in the suction side. When doing the pump down, be
sure to take notice of the items listed below :
a. Pump down should be done once each time, as it may be dangerous to the compressor, compression chamber for
pumping down repeatedly.
b. The minimum suction pressure when doing the pump down should be over 15 psig for R134a and 25 psig for R22.
c. Take notice of compressor running noise. If there is any abnormal noise happened, then emergently stop the pump
down.
2. Long term partial load operation
If compressors have to run at partial load below 50% continuously, though maybe within operation limits under such
operation condition and with temperature of motor below trip setting for overheating, insufficient dissipation of heat in
motor will occur due to lower flow rate of suction gas at partial load. If compressors operate under high temperature for
a long time, insulation of motor will deteriorate gradually at risk of serious motor damage finally. In such severe
operation conditions, Hanbell strongly recommends installation of liquid injection system to cool motor coil and use of
Pt100 or Pt1000
sensor as described in chapter 4.4s, to effectively control temperature of motor while running. It is
suggested to switch on liquid injection when temperature of motor coil is higher than 60 and turn off liquid injection
℃
when it’s lower than 50 .
℃
3. Low pressure receiver
When a compressor operates in the following application conditions, installation of a low pressure receiver is
recommended in order to prevent massive liquid refrigerant from returning to the compressor under momentary
changes of operation condition.
●
Heat pump
●
Parallel system
●
system with long piping
●
operating in the low ambient temperature area
●
system heating load varies extremely
Summary of Contents for RC2 Series
Page 24: ...Technical Manual VERSION 2 0 10 18 2018 24 UNIT SI mm Imperial in UNIT SI mm Imperial in ...
Page 25: ...Technical Manual VERSION 2 0 10 18 2018 25 SI mm Imperial in UNIT UNIT SI mm Imperial in ...
Page 26: ...Technical Manual VERSION 2 0 10 18 2018 26 SI mm Imperial in UNIT UNIT SI mm Imperial in ...
Page 27: ...Technical Manual VERSION 2 0 10 18 2018 27 UNIT SI mm Imperial in ...
Page 28: ...Technical Manual VERSION 2 0 10 18 2018 28 ...
Page 29: ...Technical Manual VERSION 2 0 10 18 2018 29 UNIT SI mm Imperial in ...
Page 30: ...Technical Manual VERSION 2 0 10 18 2018 30 ...
Page 31: ...Technical Manual VERSION 2 0 10 18 2018 31 ...
Page 32: ...Technical Manual VERSION 2 0 10 18 2018 32 ...
Page 33: ...Technical Manual VERSION 2 0 10 18 2018 33 ...
Page 34: ...Technical Manual VERSION 2 0 10 18 2018 34 UNIT SI mm Imperial in ...
Page 35: ...Technical Manual VERSION 2 0 10 18 2018 35 2 RC2 B outline drawings ...
Page 36: ...Technical Manual VERSION 2 0 10 18 2018 36 ...
Page 37: ...Technical Manual VERSION 2 0 10 18 2018 37 ...
Page 38: ...Technical Manual VERSION 2 0 10 18 2018 38 ...
Page 39: ...Technical Manual VERSION 2 0 10 18 2018 39 ...
Page 40: ...Technical Manual VERSION 2 0 10 18 2018 40 ...
Page 41: ...Technical Manual VERSION 2 0 10 18 2018 41 ...
Page 42: ...Technical Manual VERSION 2 0 10 18 2018 42 ...
Page 43: ...Technical Manual VERSION 2 0 10 18 2018 43 ...
Page 44: ...Technical Manual VERSION 2 0 10 18 2018 44 SI mm Imperial in UNIT ...
Page 60: ...Technical Manual VERSION 2 0 10 18 2018 60 ...
Page 83: ...Technical Manual VERSION 2 0 10 18 2018 83 NOTES ...