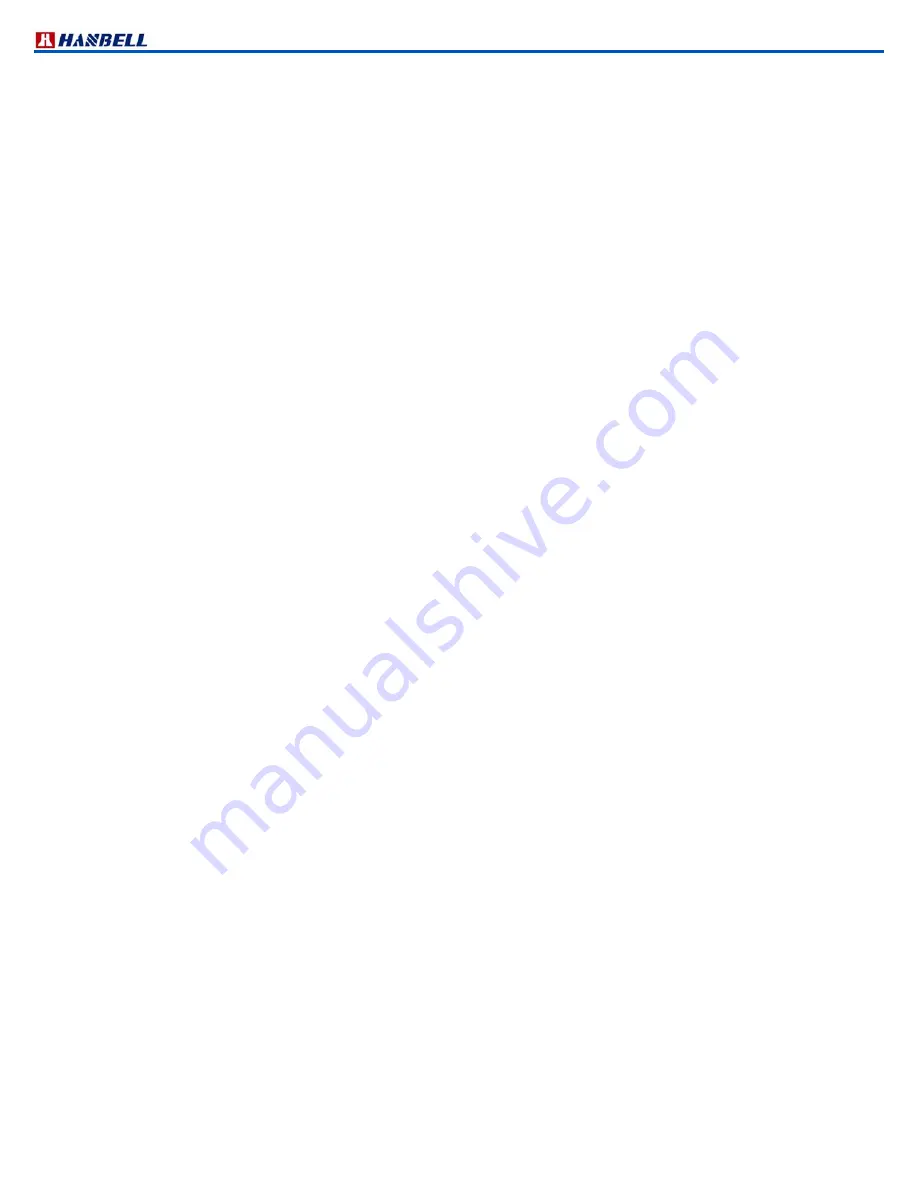
Technical Manual
VERSION 2.0 -10-18-2018
80
Hanbell Maintenance
Version 1.0
DQGZHOGLQJVODJPLJKW¿QGLWVZD\WRFRPSUHVVRU¶VVXFWLRQVLGH:LWKWKHKHOSRIWKHVXFWLRQVWUDLQHUGHEULV
will be gathered inside the strainer to protect the compressor from rotor damage. Technicians should check
the suction strainer at the
HQGRIFRPPLVVLRQLQJDQGDIWHUKRXUVRILQLWLDOUXQQLQJ
. Any dirt and
unwanted material should be removed during the checking. Wash the strainer basket in solvent and blow
clean with air.
1.2.2 Oil Analysis
At the
HQGRIFRPPLVVLRQRUDIWHUKRXUVRILQLWLDOUXQQLQJ
, oil analysis is recommended to be executed
at jobsite. The purpose of doing oil analysis is to understand the compressor’s working environment and
ensure the oil quality. If moisture contamination exists in the system, this will lead to changing of oil quality
and cause poor lubrication for internal moving parts which can cause severe damage to the compressor
in the future. Technicians should replace the oil immediately to protect the internal moving parts with good
lubrication and recheck the oil
DJDLQDIWHUKRXUVRSHUDWLRQ
. If the oil analysis shows the oil is in good
condition,
UHFKHFNWKHRLOHYHU\PRQWKV
to ensure the condition remains safe.
In the case of being unable to do the oil analysis periodically, consult Hanbell oil change schedule because
the interval of oil change varies by the oil type and compressor operating condition.
Check the oil acidity periodically and change the oil if the oil acidity value measures lower than pH6.
1.3. Long Term Maintenance
The information below is focusing on standard long term maintenance. Technicians should understand that
these items are not assumed to take over all the necessary routine checks. Daily check for operation conditions
is also very important to have a stable operating system.
Please refer to the recommended maintenance schedule found on the following pages. This schedule is only
for the technician’s reference and should be considered as the minimum guideline to maintain the system’s nor-
mal operation. Technicians still can do any examination by their own that will ensure a stable system
operation. In case of any irregular situation or abnormal condition that takes place on the compressor
system, Technicians should stop the compressor and contact the contractor who installed the unit.
1.3.1 Mechanical Seal
The Shaft seal leakage should be observed everyday and be inspected by removing the cover at least once
per year when doing other regular maintenance. Special attention should be given to hardening and cracking
of the O-ring, wear, scoring, material deposits, oil coke and copper plating. The purpose of checking the
mechanical seal every year is to ensure the stable operation for the following year. Wearing parts of shaft
seal are recommended to be changed with a new one.
1.3.2 Piston Sealing
The Piston is also recommended to be inspected every year to ensure the function of capacity control. If
abnormal wearing is found, the corresponding part should be replaced by a new one. Prior to replacing, the
technicians should do an inspection and determine what is causing the wearing problem.
1.3.3 Vibration Analysis
9LEUDWLRQDQDO\VLVFDQKHOSWRGHWHFWEHDULQJZHDUDQGRWKHUPHFKDQLFDOIDLOXUHV$FHUWL¿HG+DQEHOO7HFKQLFLDQ
should perform this check.
Overhaul Review
Overhaul review is recommended to be done at least
HYHU\\HDUV
. It is the best time to review the internal parts
DQGUHSODFHDOOZHDULQJSDUWVIRUWKHIROORZLQJORQJWHUPRSHUDWLRQ$FHUWL¿HG+DQEHOO7HFKQLFLDQVKRXOG
perform this review.
3
Summary of Contents for RC2 Series
Page 24: ...Technical Manual VERSION 2 0 10 18 2018 24 UNIT SI mm Imperial in UNIT SI mm Imperial in ...
Page 25: ...Technical Manual VERSION 2 0 10 18 2018 25 SI mm Imperial in UNIT UNIT SI mm Imperial in ...
Page 26: ...Technical Manual VERSION 2 0 10 18 2018 26 SI mm Imperial in UNIT UNIT SI mm Imperial in ...
Page 27: ...Technical Manual VERSION 2 0 10 18 2018 27 UNIT SI mm Imperial in ...
Page 28: ...Technical Manual VERSION 2 0 10 18 2018 28 ...
Page 29: ...Technical Manual VERSION 2 0 10 18 2018 29 UNIT SI mm Imperial in ...
Page 30: ...Technical Manual VERSION 2 0 10 18 2018 30 ...
Page 31: ...Technical Manual VERSION 2 0 10 18 2018 31 ...
Page 32: ...Technical Manual VERSION 2 0 10 18 2018 32 ...
Page 33: ...Technical Manual VERSION 2 0 10 18 2018 33 ...
Page 34: ...Technical Manual VERSION 2 0 10 18 2018 34 UNIT SI mm Imperial in ...
Page 35: ...Technical Manual VERSION 2 0 10 18 2018 35 2 RC2 B outline drawings ...
Page 36: ...Technical Manual VERSION 2 0 10 18 2018 36 ...
Page 37: ...Technical Manual VERSION 2 0 10 18 2018 37 ...
Page 38: ...Technical Manual VERSION 2 0 10 18 2018 38 ...
Page 39: ...Technical Manual VERSION 2 0 10 18 2018 39 ...
Page 40: ...Technical Manual VERSION 2 0 10 18 2018 40 ...
Page 41: ...Technical Manual VERSION 2 0 10 18 2018 41 ...
Page 42: ...Technical Manual VERSION 2 0 10 18 2018 42 ...
Page 43: ...Technical Manual VERSION 2 0 10 18 2018 43 ...
Page 44: ...Technical Manual VERSION 2 0 10 18 2018 44 SI mm Imperial in UNIT ...
Page 60: ...Technical Manual VERSION 2 0 10 18 2018 60 ...
Page 83: ...Technical Manual VERSION 2 0 10 18 2018 83 NOTES ...