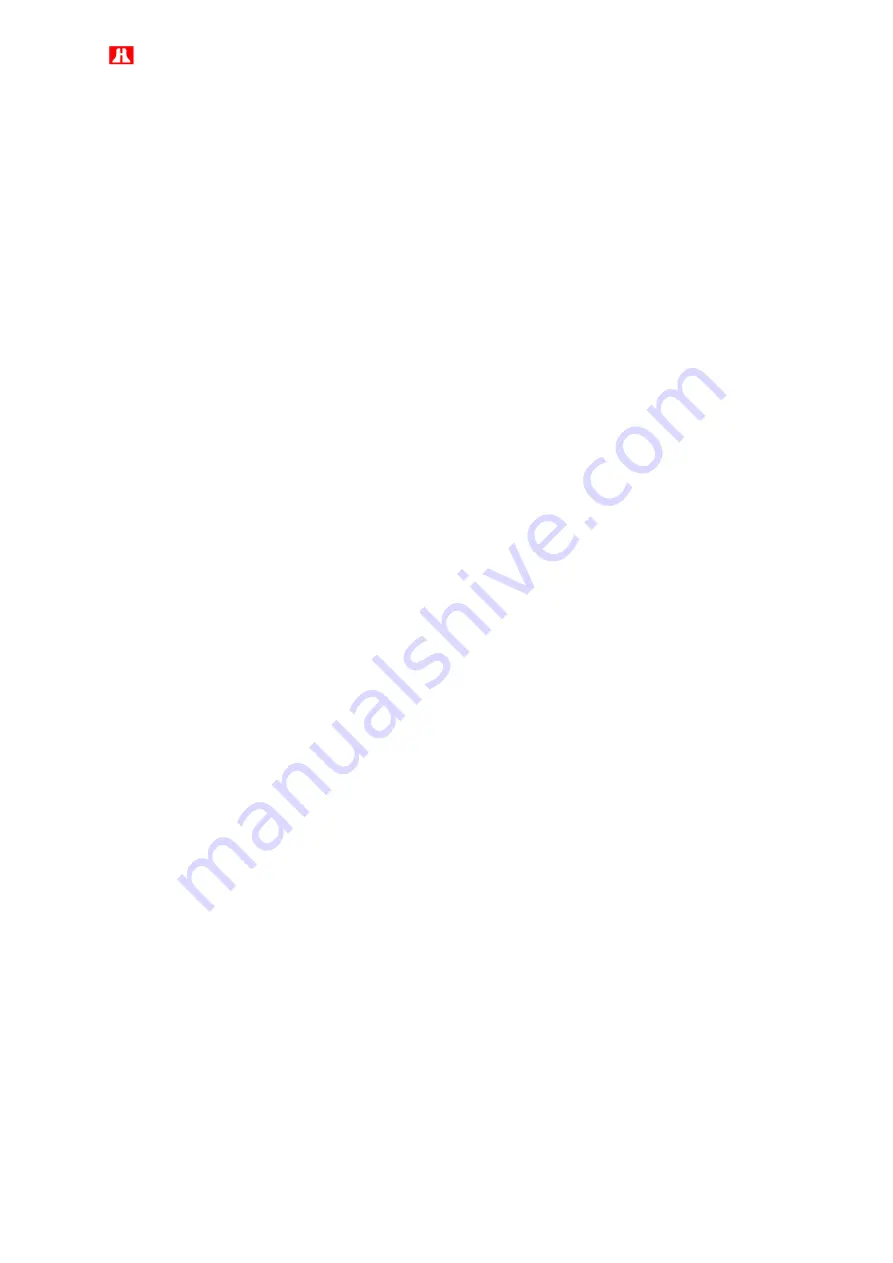
95
Vol. 2.6 © 2020 Hanbell Precise Machinery Co., Ltd. All rights reserved
1. The replacement of compressor internal parts should be performed by qualified service
technicians only.
2.When reclaiming liquid refrigerant, chilled water pump and cooling water pump can be off;
when reclaiming , make sure chilled water pump and cooling water pump are running (or
drain out chilled water or cooling water); when reclaiming refrigerant(liquid or gas), make
sure start circuit of the compressor is open and oil heater must be powered. When
reclaiming refrigerant till 1~2psi, it’s recommended to drain out refrigerant and charge
nitrogen to establish positive pressure and during repair keep purging some amount of
nitrogen; if the job of greater opening is done(dismantle gas return pipe of motor cover), it’s
recommended to reclaim refrigerant and charge nitrogen to positive pressure, vacuum
again (below 5 torr) and then charge nitrogen to positive pressure (within 8 hours, it cannot
increase above 1.33torr ) to ensure remain of refrigerant in the system to the minimum.