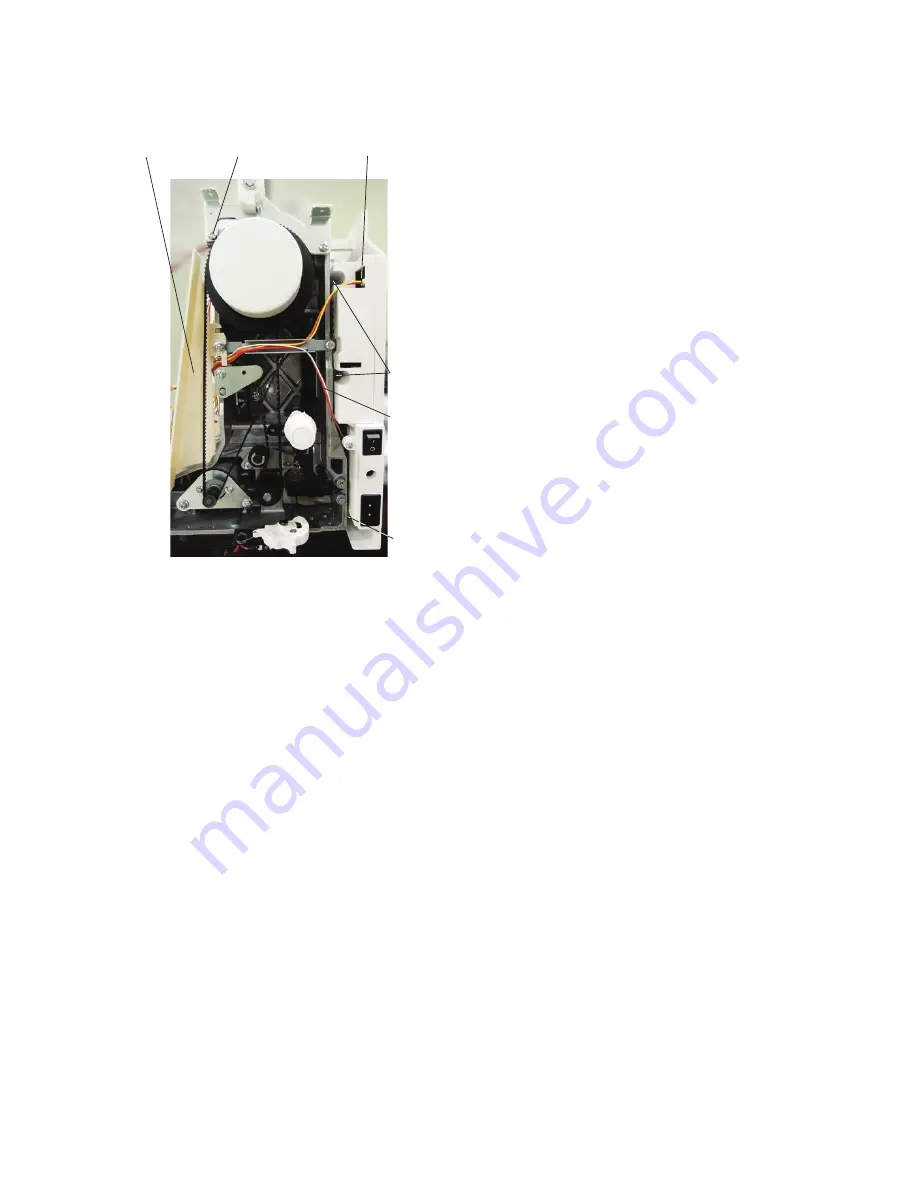
9
Switching power supply unit
To remove:
1. Remove the belt cover, the top cover and the front
cover (see page 1, 2 and 5).
2. Loosen the setscrew A. Remove the cord guide plate.
3. Disconnect the power supply connector from the
switching power supply unit.
4. Remove the foot control connector from the printed
circuit board A.
5. Remove the setscrews B, and switching power supply.
To attach:
1. Follow the above procedure in reverse.
Replacing electronic components
Switching power
supply connector
Setscrew A
Setscrew B
Foot control
connector
(cord)
Cord guide plate
Setscrew B