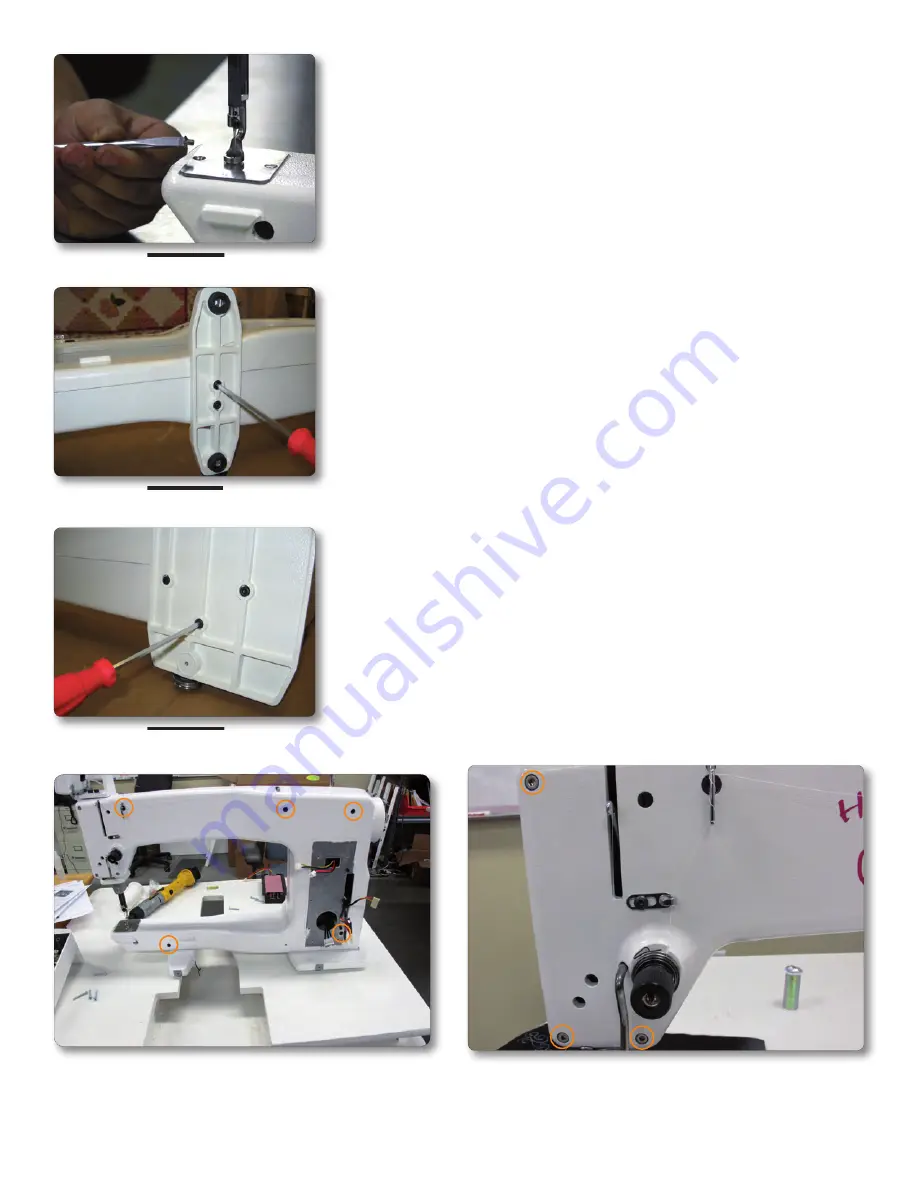
Page 18
HQ Sweet Sixteen Service Manual
Figure 2.20
Figure 2.21
Figure 2.22
Figure 2.24
7. Remove the needle plate. (
Figure 2.20
) (#3 fl at
screwdriver)
8. Loosen both the front and rear base plates a couple
turns to allow the front cover to be removed. (
Figures
2.21 and 2.22
) (Tools needed: 5 mm handle Allen wrench)
9. Remove the 5 frame screws shown circled in
Figure
2.23
. Note: The fi fth screw is behind the C-pod and was
removed in step 4.
(4 mm handle Allen. May need 4 mm L Allen tool to break
screws loose.) Note: The three small screws (shown cir-
cled in
Figure 2.24
) were removed in step 2.
10. Separate the front frame cover. Make sure the take-up
lever does not get caught in the frame slot.
Important Note: The take-up lever is very hard and will
break, not bend.
Figure 2.23
2. Removal of the Front Cover -
Continued