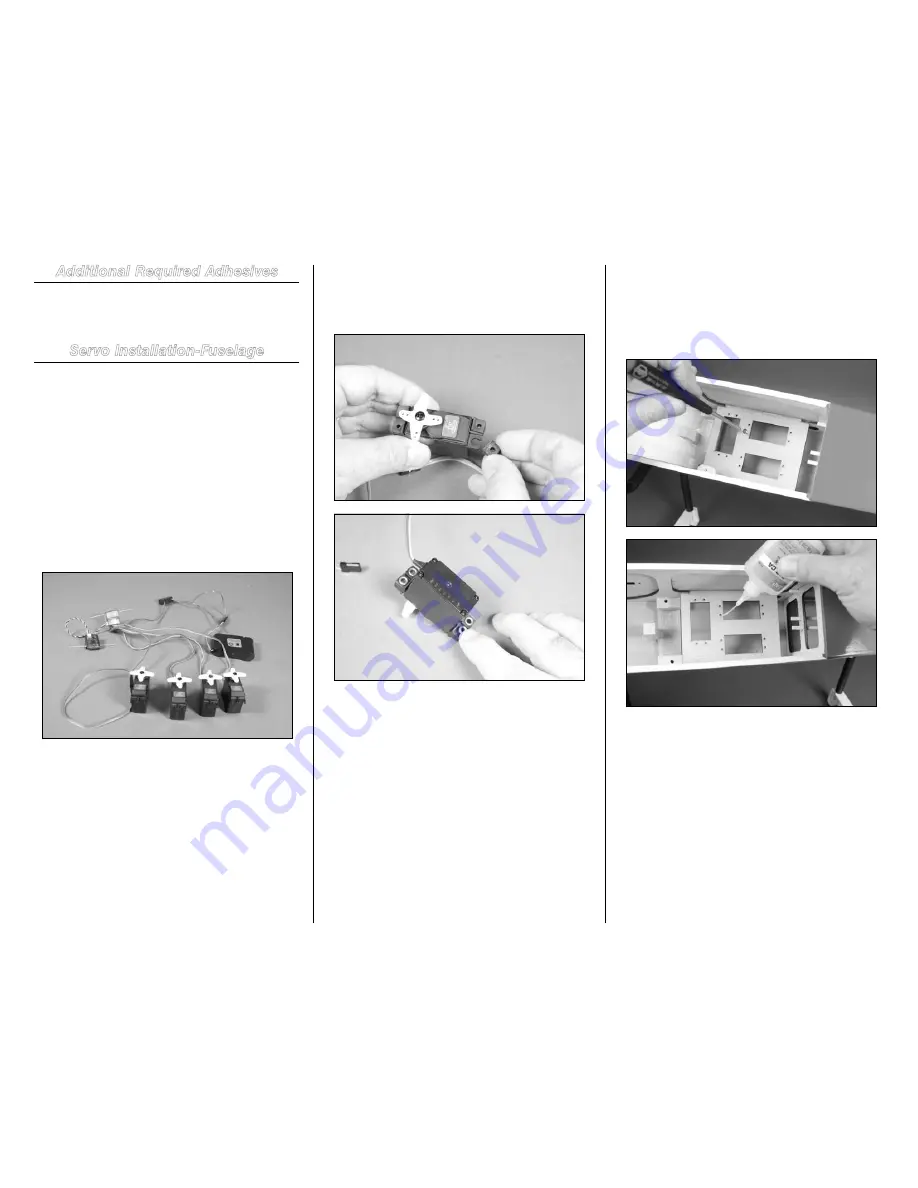
6
Hangar 9 Alpha 40 ARF Assembly Manual
Additional Required Adhesives
30-Minute Epoxy
(HAN8002)
Medium CA
(PAAPT02)
Thin CA
(PAAPT08)
Servo Installation-Fuselage
Required Parts
Fuselage
Servo with hardware (4)
Receiver
Receiver battery
Switch harness
6-inch (152mm) servo extension
Required Tools and Adhesives
Phillips screwdriver: #1
Thin CA
Step 1
Locate the necessary items for your radio system. Plug the
servos and switch harness in the receiver. Plug a battery into
the switch harness. Check that all the servos work properly.
Note
: You may need to bind your radio system if you
are using a 2.4GHz system. Follow the instructions
provided with your radio system to do so.
Note
: Make sure to turn off both the transmitter and
receiver before unplugging the servos.
Important
: You will need to connect a 6-inch (152mm)
extension in the Aileron port of the receiver to connect
to the servo used for the Ailerons. Leave the extension
plugged into the receiver when unplugging the servos.
Step 2
Prepare the servos by installing the rubber grommets and
brass eyelets in the servos. Note that the eyelets are inserted
from the bottom of the servo.
Step 3
Use a #1 Phillips screwdriver to thread a servo mounting
screw into the holes in the servo tray inside the fuselage.
Apply 2–3 drops of thin CA in the holes to harden the
surrounding wood. This makes the screws more secure and
less likely to vibrate loose.