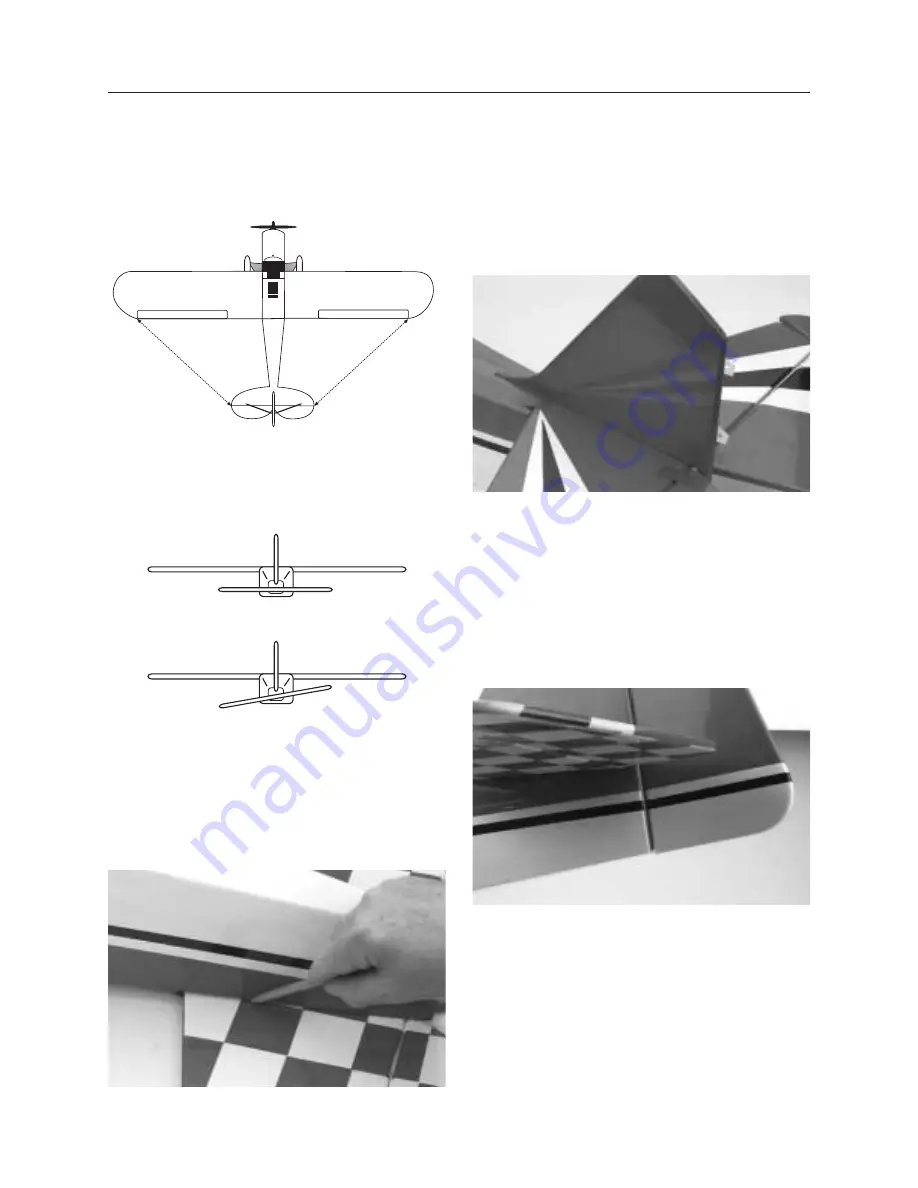
21
Step 6.
With the fuselage resting on a flat surface, align the
horizontal stabilizer by measuring from fixed points on the wing
to the outside of the trailing edge tip of the horizontal stabilizer.
Make sure the trailing edge of the horizontal stabilizer stays on
its center mark.
Step 7.
Adjust the horizontal stabilizer until you have an equal
distance on both the right and left side of the fuselage and that
the horizontal stabilizer is positioned correctly (not tilted) with
reference to the wing. Refer to the illustrations below.
Step 8.
When you're satisfied with the alignment of the
horizontal stabilizer with the wing, carefully mark the position
with a pencil at the junction where the horizontal stabilizer meets
the fuselage. The pencil should leave a slight indentation in the
covering. Mark the bottom of the horizontal stabilizer. Use
masking tape to hold it in position.
Step 9.
Trial fit the vertical stabilizer in position on the
fuselage, after removing the rudder and hinges. Set these aside
for now, as the rudder will be attached later in Section 8. Make
sure the vertical stabilizer is inserted completely. Some slight
trimming to the bottom of the fin may be necessary
Hint:
The back of the vertical stabilizer slides into a slot
at the back of the fuselage.
Step 10.
Carefully check the vertical stabilizer to make sure it's
aligned 90° to the horizontal stabilizer. A 90-degree triangle is
helpful in this step.
Hint:
When installing the vertical stabilizer, use the rudder
to check for proper stabilizer height so the rim of the rudder
matches trim scheme at fuselage rear. It may be necessary
to cut off a small amount from the bottom of the vertical
stabilizer to get the rudder to drop down to the proper
position so the rudder and the fuselage align.
Step 11.
Double-check the horizontal stabilizer and vertical fin
alignment. It may be necessary to slightly trim the balsa wood on
the fuselage or tail parts with a sharp hobby knife or sandpaper
to achieve exact alignment.
Section 6: Installing the Tail (Vertical and Horizontal Stabilizer)
CONTINUED
Correct
Incorrect
Summary of Contents for Clipped-wing Taylorcraft
Page 55: ...55 Notes ...