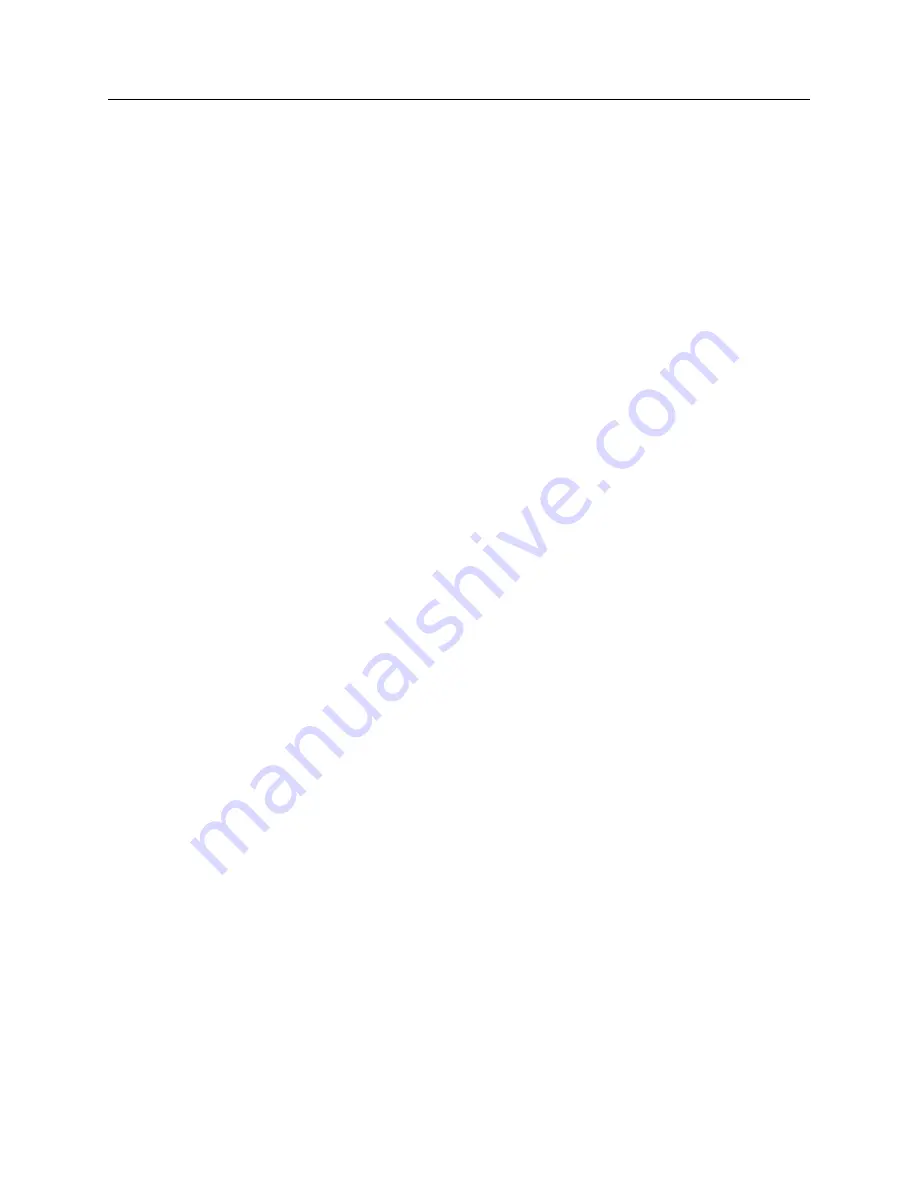
4
Tools and Supplies Required
Adhesives
Thin CA (Cyanoacrylate) glue
Thick CA (Cyanoacrylate) glue
6-Minute Epoxy (HAN8000)
30-Minute Epoxy (HAN8002)
Tools
Drill
Drill bits: 1/16'', 1/18'', 5/32'', 1/14''
Soldering iron
Phillips screwdriver
Z-bend pliers
CA remover/debonder
Standard pliers
Mixing sticks
5/32” hex wrench
Medium sandpaper
Moto-tool with sanding drum and cut-off wheel
Hobby knife with #11 blade
Masking tape
Threadlock Z-42 (Pacer)
Canopy Glue (Pacer PAAPT56)
Silver Solder (Staybrite)
Epoxy brushes
Scissors
Straight edge
Rubbing alcohol
1/16” hex wrench
Sanding stick (medium)
Small round file
Paper towels
Felt-tipped pen or pencil
90-degree triangle
Measuring device (36”)
Summary of Contents for EDGE 540
Page 52: ...52 ...
Page 53: ...53 Template Cut Out of Cowl Bottom MDS 1 48 ...
Page 54: ...54 ...
Page 55: ...55 ...
Page 56: ... 2000 Horizon Hobby Inc www horizonhobby com ...
Page 57: ...57 ...
Page 58: ...58 ...
Page 59: ...59 ...