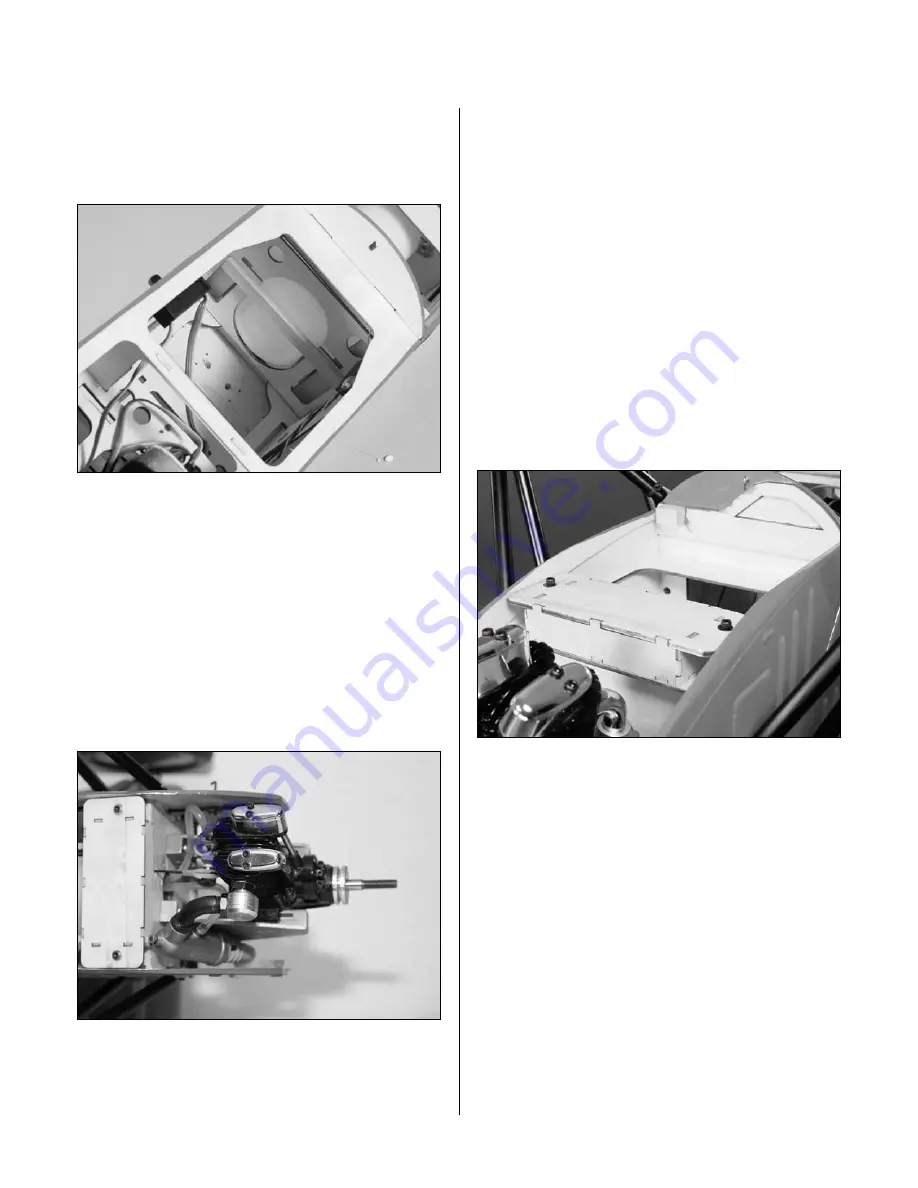
35
Step 16
Slide the fuel tank into the fuselage. Position the fuel
tank brace in the fuselage as shown and secure with
medium CA.
Important
: Make sure clunk line inside
the fuel tank is not looped around the vent
line which can occur during shipping. If
the clunk does not move freely, you will
have fuel delivery issues in flight.
Step 17
Attach a 90-degree adapter to the engine, then attach the
muffler to the adapter. Connect the lines from the fuel tank
to the carburetor and muffler. Use an exhaust deflector to
direct the exhaust out the bottom of the fuselage.
Note
: The red tube from the fuel tank attaches
to the muffler, and the blue to the carburetor.
Note
: We used a fuel dot (HAN115) to allow
fueling the tank from outside the cowling.
Hint
: Use a Remote Glow Plug Adapter
(HAN3025) to allow starting the
engine without cutting a hole in the
dummy motor for the glow igniter.
Step 18
The weight box is attached to the fuselage using two
4-40 x 1
1
/
4
-inch socket head screws and two #4
washers. It will be necessary to add weight when
balancing your model.
Important
: Make sure to use
threadlock on the screws to prevent
them from vibrating loose.
Summary of Contents for fokker D.VII
Page 53: ...53 Building and Flying Notes ...