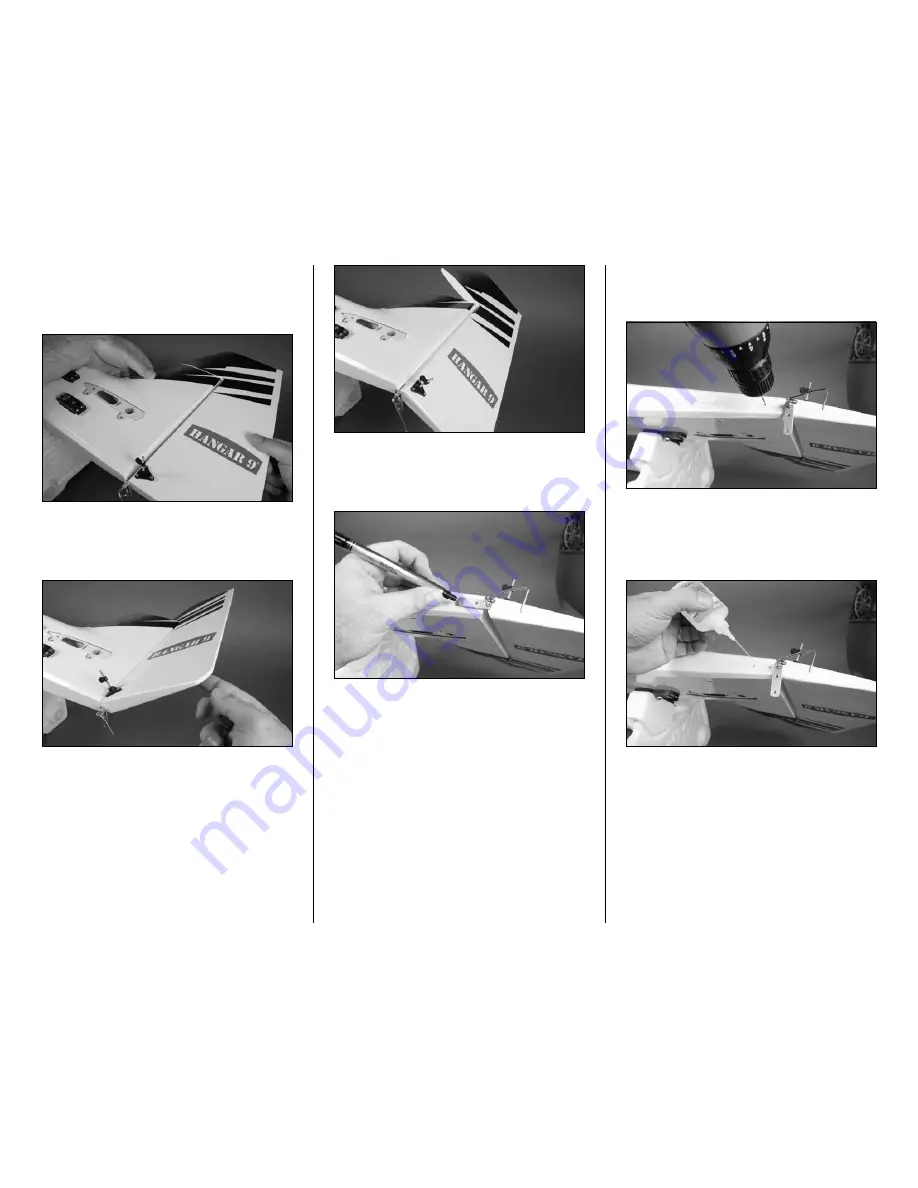
20
Hangar 9 Funtana 125 ARF Assembly Manual
Step 22
Gently pull on the rudder and fuselage to make sure each of
the hinges is secure. If not, reapply CA to the hinge that is
not secure.
Step 23
Flex the rudder through its range of motion a few dozen
times to break in the hinges.
Step 24
Use a felt-tipped pen to mark the locations for the two
screws that will secure the tail wheel bracket to the fuselage.
Step 25
Move the bracket out of the way and use a drill with a 1/16-
inch (1.5mm) drill bit to drill the two holes for the screws.
Step 26
Place 2–3 drops of thin CA into each hole to harden the
surrounding wood. This will keep the screws from pulling
out of the fuselage.