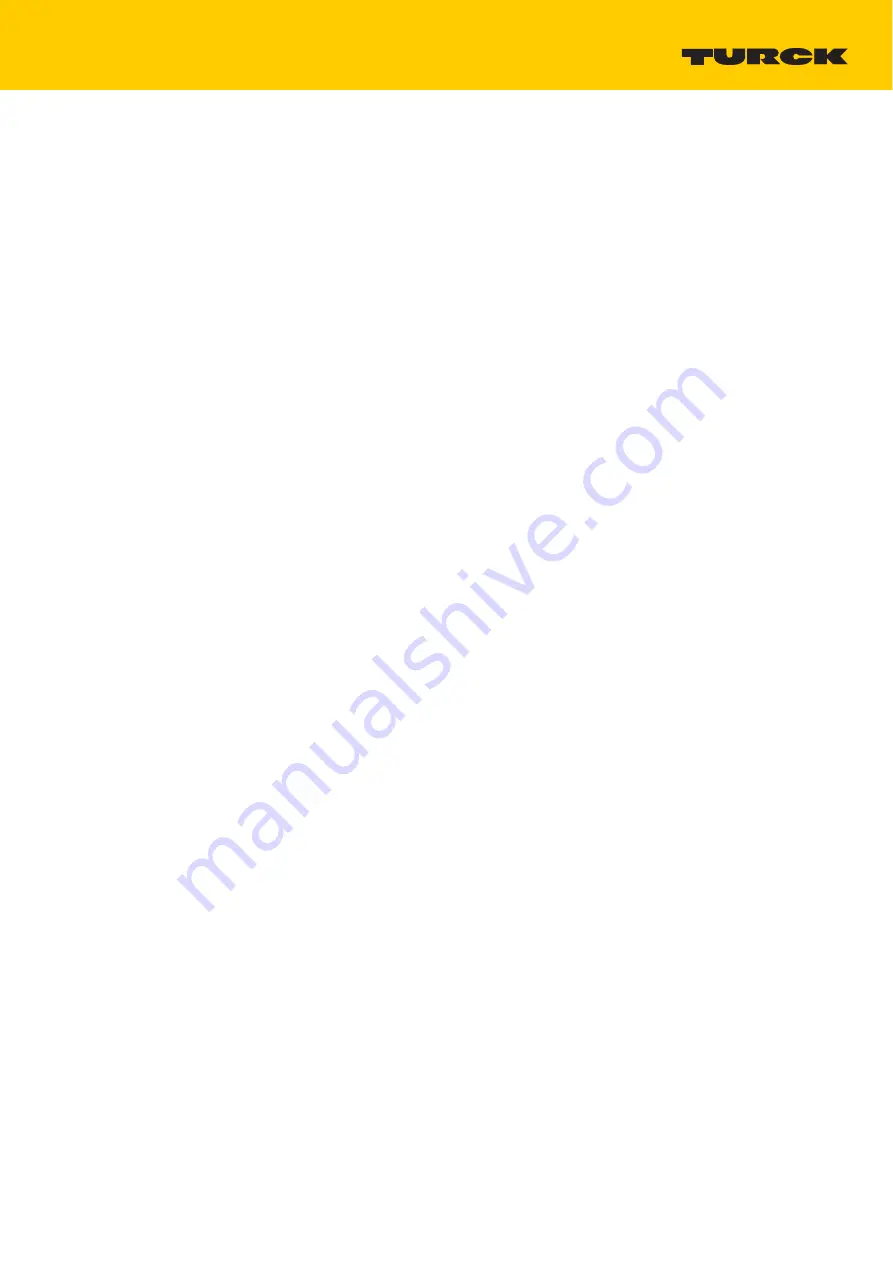
9
2020/09
3 For Your Safety
The product is designed according to state-of-the-art technology. However, residual risks still exist.
Observe the following warnings and safety notices to prevent damage to persons and property.
Turck accepts no liability for damage caused by failure to observe these warning and safety notices.
3.1
Intended use
The devices are only intended for use in industrial applications.
The BL20 gateway BL20-E-GW-CO is part of the BL20 system. It forms the interface to a CANopen
network and forwards the data collected from the field by the BL20 I/O modules within the BL20 sta
-
tion to the higher-level CANopen master.
The devices may only be used as described in these instructions. Any other usage shall be consid
-
ered improper and Turck shall not be held liable for any resulting damage.
3.2
General safety instructions
The device may only be assembled, installed, operated and maintained by professionally trained
personnel.
The device may only be used in accordance with applicable national and international regula
-
tions, standards and laws.
The device only meets the EMC requirements for industrial areas and is not suitable for use in res
-
idential areas.
Summary of Contents for BL20-ECO
Page 1: ...Your Global Automation Partner BL20 E GW CO ECO Gateway for CANopen Instructions for Use...
Page 2: ...2 Hans Turck GmbH Co KG T 49 208 4952 0 F 49 208 4952 264 more turck com www turck com...
Page 6: ...Hans Turck GmbH Co KG T 49 208 4952 0 F 49 208 4952 264 more turck com www turck com 4...