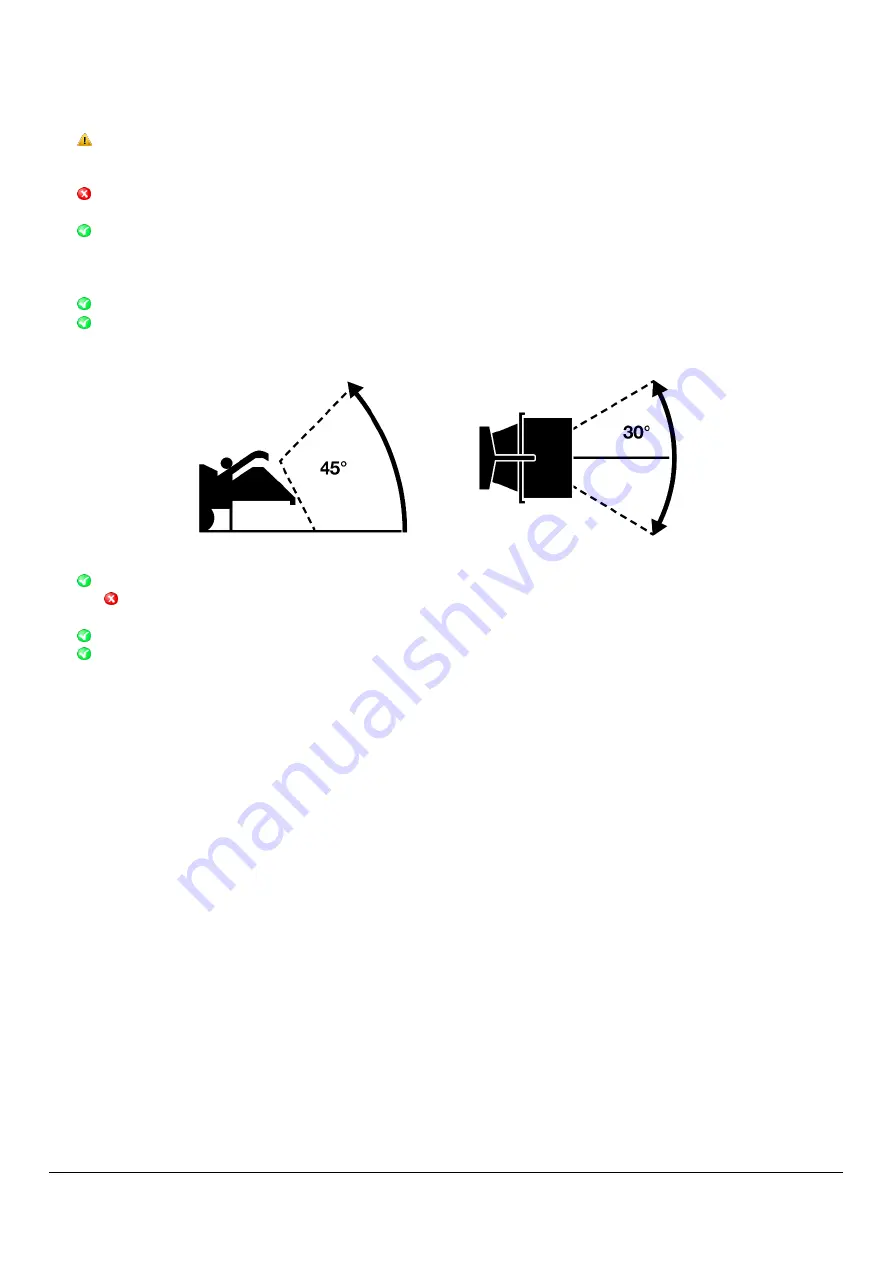
Hansa C65RX O&M Manual
–
OM-029 First Release 4/05/2021
© Hansa Chippers 2021
6
Winch operation safety
Winch operation safety:
Be careful when retracting the winch.
Do NOT
retract the winch hook in past the rollers at the end of the winch boom
The winch does not automatically stop once it reaches the rollers. Retracting the winch too far may damage the
hook or rollers
Do NOT
attempt to lift/pull objects that weigh more than 1400 kg.
Ensure you are familiar with the capabilities and weight of the machine before winching particularly heavy objects
Ensure the winch rope is fully retracted and attached to the keeper hook before feeding material into the chipper
This is to ensure the feed roller/cutting rotor does not pull in the winch rope. The rotor is rotating at high speed
and if it does pull the winch rope in, it will do so rapidly and has the potential to cause serious injury or death to
operators and/or result in damage to the machine
Ensure both stabiliser feet are lowered while operating the winch
Ensure the pull angle of the winch is within the safe operating envelope. This is outlined below:
Ensure the rope wraps around the drum at least five times
Do NOT
extend the rope past this point
Winches operate on the friction principle; with less than five wraps, the rope will separate from the drum
Ensure both stabiliser feet are lowered while operating the winch
If a replacement winch rope is required, the rope must be of equal or greater strength than what is specified (see the
‘Operation –
Hydraulic Winch’ section of this manual). Contact Hansa fo
r more information
Chipping safety
Checklist before operation
Engine:
✓
Check oil level in engine
✓
Check condition of air cleaner
✓
Refer to engine manual for more details
Check Hydraulics:
✓
Check level of hydraulic fluid
✓
Check all hydraulic components for leaks
General:
✓
Check drive belt and pump belt for proper tension
✓
Check machine for proper lubrication
✓
Check nuts and bolts to ensure they are tight
✓
Check diesel level
✓
Check that the fuel cap is secured and there is no fuel leaking from the tank
✓
Check the tracks are tight and in good condition
✓
Check direction of the discharge chute
✓
Check guards are all in place and in good condition
✓
Check all labels are legible. Replace if necessary (contact Hansa for replacements)
✓
Refer to maintenance section for more details
Safe operating envelope (vertical)
Safe operating envelope (horizontal)