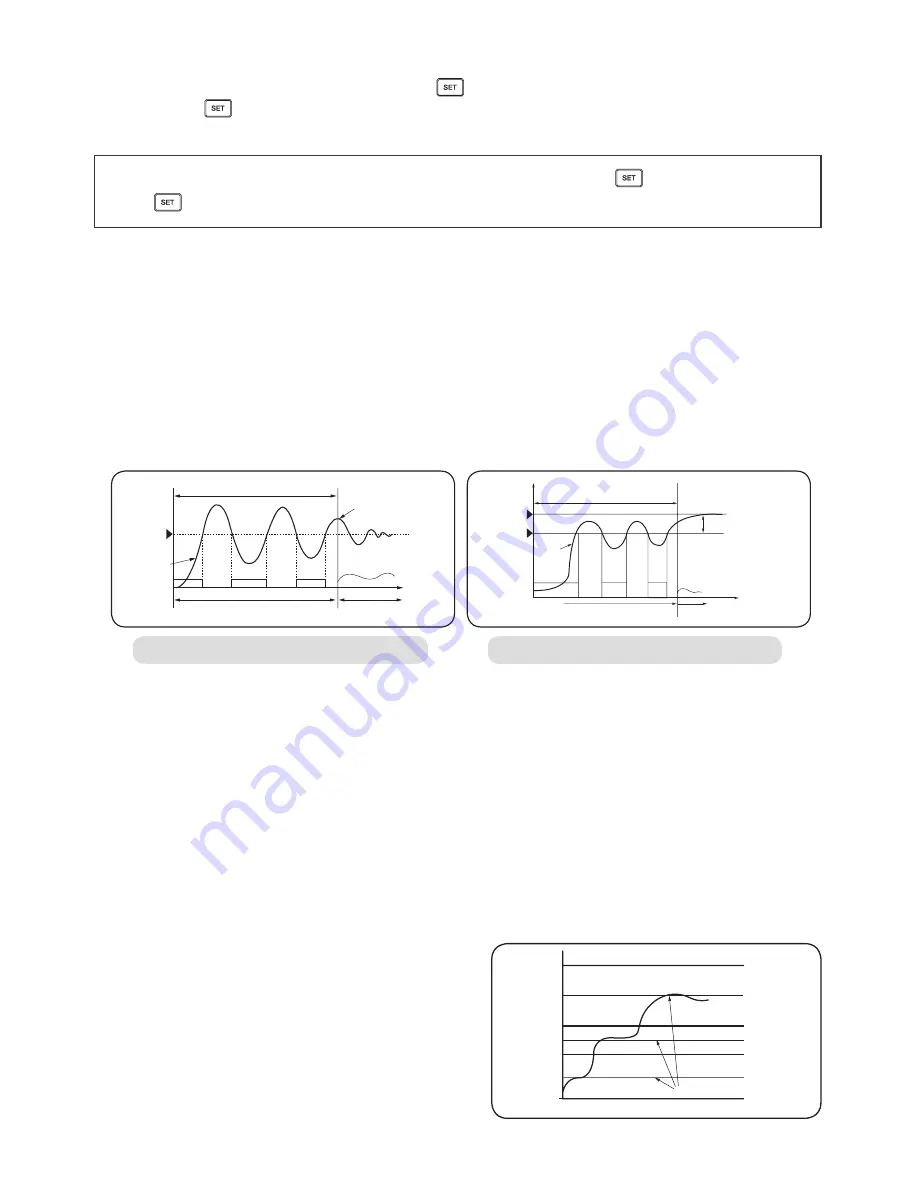
46
◼
Auto Tuning Group (G.AT)
10-2. Operation Menu (OPER)
●
Standard Auto-Tuning (AT.MD=STD)
• What is the Auto-Tuning?
The Auto-Tuning (AT) is used to let the controller measure process characteristics and automatically set the
most appropriate values for the PID parameters. During the default AT process, the control output will function
in an ON/OFF mode, and the controller will use the responses to calculate the needed PID values (For
instance, AT Gain is achieved as shown in Figures below; Cycle is 2.25). There are two types of Auto-Tuning
Mode (AT.MD)- Standard AT (STD) and Low PV AT (LOW PV).
1) LEVEL is OFF :
•Turn ON AT on Auto Tuning Group (G. AT) in Fixed Control (FIX) mode. Referring current SV and SVNO,
the AT is performed and the gain value is assigned in relevant PID GROUP.
【Ex.1】 If SV is 50 ℃ and SVNO is 2;
AT occurs at 50 ℃, and the gain value is assigned to relevant PID GROUP.
• Turn ON AT in Program Control mode.
AT is performed at NSV and the gain value is assigned in relevant PID GROUP.
【Ex.2】 If PID NO is 3 in Segment-3, SV is 20 ℃;
AT is performed in Segment-3 and the gain value is assigned in relevant PID GROUP-3.
【Standard Auto Tuning 】
【Low PV Auto Tuning】
Set Value - Maximum scale 10%
ON / OFF operation
PID Control
Time
AT = ON
ON
ON
OFF
OFF
ON
Control
Output
AUTO Tuning Process
ON / OFF operation
PID Control
Time
AT = ON
ON
ON
OFF
OFF
ON
Control
Output
Process Value
Set Value
AUTO Tuning Process
Auto Tuning finish
2) LEVEL is ON:
• Turn ON AT on Auto Tuning Group (G. AT) in Fixed
Control (FIX) mode. AT is performed at NSV and the gain
value is assigned in relevant PID GROUP.
【Ex.1】 If 1.LVL is 100'C, 2.LVL is 200'C, SV is 50'C, SV
NO is 2, AT is performed at 50'C and the gain value is
assigned to PID GROUP-1. (SVNO is ignored).
•Turn ON AT in Program Control mode. AT is performed
at NSV and the gain value is assigned in
relevant PID GROUP.
2.PID
2.LVL
1.LVL
1.PID
3.PID
Maximum
Indicating
Range
Minimum
Indicating
Range
TUNING POINT=n.LVL average value
◼
Quick group (G.QUICK)
PROG screen
Push ▲▼ key and go G.QUICK.
Push key
USE=OFF display. Change it to USE=ON?
by ▲▼ key. Push key to select it. Sequentially select other parameter and make up quick menu.
To cancel Quick Menu, PROG screen
Push ▲▼ key and go G.QUICK.
Push key > Set USE=OFF.
Push key to select it.
Summary of Contents for NP200
Page 2: ......