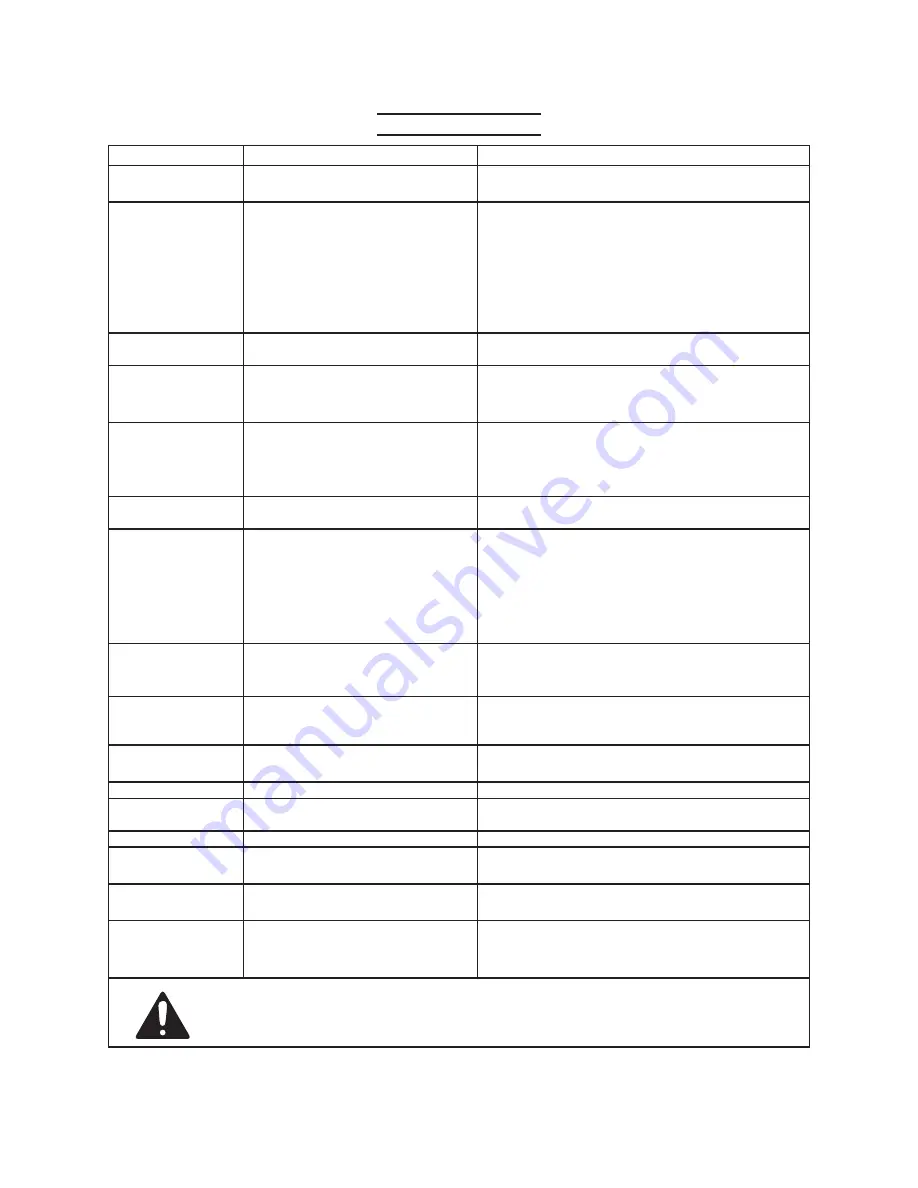
SKU 95082
For technical questions, please call 1-800-444-3353.
Page 15
troubleshooting
Problem
Possible causes
Likely Solutions
Tool will not start
No power at outlet.
1.
Cord not connected.
2.
Check power at outlet.
1.
Check that cord is plugged in.
2.
Gouging at ends of
board (snipe)
Dull Blades.
1.
Too little support of long boards.
2.
Uneven force on cutter head.
3.
Roller case not level with base.
4.
Lumber not butted properly.
5.
Replace blades.
1.
Provide better support for long boards.
2.
Adjust board when it is in contact with only one
3.
feed roller.
Adjust roller case.
4.
Butt each end of stock together evenly.
5.
Grain is ragged
Wood has a high moisture
1.
content.
Use dry wood.
1.
Torn grain
Cut is too heavy.
1.
Blades cutting against grain.
2.
Dull blades.
3.
Reduce depth of cut.
1.
Cut boards along grain.
2.
Replace blades.
3.
Rough, raised grain
Dull blades.
1.
Cut is too heavy.
2.
Moisture content is too high.
3.
Replace blades.
1.
Reduce depth of cut.
2.
Use dry wood or wood with lower moisture
3.
contents.
uneven side-to-side
depth of cut
Roller case not level with planer
1.
base.
Adjust so that roller case is level.
1.
Roller case
adjustment difficult
Sprockets or chain dirty.
1.
Screws or columns dirty.
2.
Screws worn.
3.
Friction between roller case and
4.
covers.
Roller case not parallel.
5.
Clean and lubricate sprockets and chain.
1.
Clean and lubricate screws and columns.
2.
Replace screws.
3.
Clean and lubricate roller case and cover.
4.
Adjust roller case.
5.
Board feeds in,
but will not move
through.
Out feed rollers are clogged.
1.
Too much pressure on cutter head
2.
from long board.
Clean Planer.
1.
Use supports to hold workpiece up.
2.
Board thickness
does not match
depth of cut scale.
Indicator not set correctly.
1.
Have indicator repaired by a qualified technician.
1.
Chain jumping
Sprockets worn.
1.
Chain worn.
2.
Have sprockets replaced.
1.
Have chain replaced.
2.
Belt Slipping
Belt is loose.
1.
Replace belt.
1.
Roller case will not
lower
Thickness gauge setting restricts
1.
roller case.
Reset thickness gauge.
1.
Excessive dust in air
Leaking bag or loose connection.
1.
Check connections or replace collection bag.
1.
Fan very loud
Debris caught in fan.
1.
Fan is loose.
2.
Remove debris.
1.
Tighten hardware on fan.
2.
Motor overheats
Motor overloaded.
1.
Motor not cooling right.
2.
Reduce depth of cut
1.
Clean sawdust from Planer.
2.
Circuit breaker or
fuse keeps tripping
Motor overloaded.
1.
Wrong circuit breaker or fuse.
2.
Dull blades.
3.
Reduce depth of cut.
1.
Use correct circuit breaker or fuse.
2.
Replace blades.
3.
Follow all safety precautions whenever diagnosing or servicing the
tool. disconnect power supply before service.